11 Considerations for
Choosing an MES
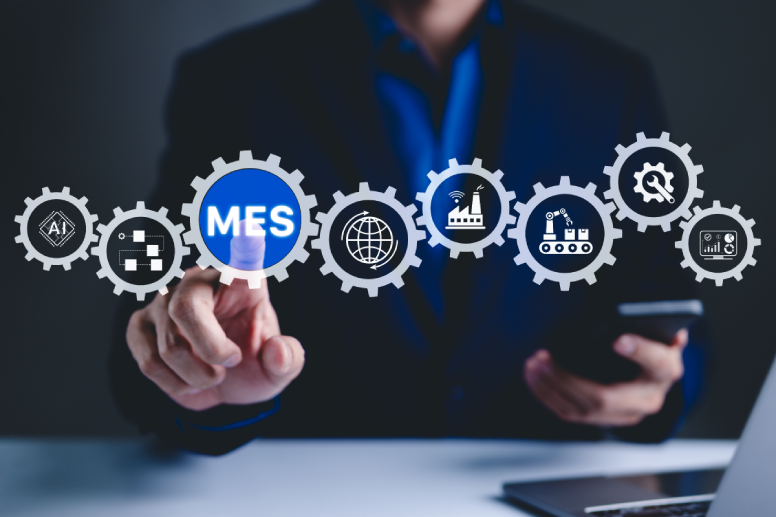
11 Considerations for Choosing an MES
Selecting a manufacturing execution system (MES) is one of the most impactful decisions a manufacturing company can make.
With new manufacturing technologies, an MES provides the tools needed to streamline processes, facilitate compliance, and drive data centric decisions. However, not all MES solutions are created equal, and choosing one requires careful consideration of various factors to meet your unique business needs. A well-chosen MES can optimize workflows, enhance visibility, and empower your factory to achieve its full potential.
What is an MES?
A manufacturing execution system is an advanced digital platform designed to manage and optimize production processes in real time. Acting as the connective tissue between enterprise resource planning (ERP) systems and the shop floor, an MES provides unparalleled visibility into production workflows while automating and standardizing key operations. This ensures efficiency, reduces errors, and allows for proactive problem-solving.
Its core functionalities include real-time tracking of production data, quality control management, and end-to-end product traceability. An MES integrates seamlessly with equipment and software across the factory, creating a unified ecosystem that enables informed decision-making. An MES facilitates adherence to regulations while maintaining robust documentation and audit trails for industries with stringent compliance needs—such as medical devices, aerospace, and automotive.
Beyond operational oversight, an MES delivers actionable insights through advanced analytics, allowing manufacturers to predict equipment maintenance needs, refine scheduling, and optimize resource allocation. Whether managing multi-site operations or scaling production, an MES is an indispensable tool for achieving consistency and productivity in manufacturing.
Why Should You Implement an MES?
Implementing an MES is a transformative step for any manufacturing organization seeking to streamline operations, improve quality, and stay innovating. Operational inefficiencies and compliance risks within manufacturing ecosystems can quickly escalate costs and hinder growth. An MES addresses these challenges by offering a real-time centralized platform to monitor and manage production, ensuring seamless coordination between teams, systems, and machinery.
- Real-time visibility: Full transparency into production processes, enabling quick responses to potential bottlenecks.
- Improved quality control: Automated inspections and traceability tools to reduce defects and enhance product standards.
- Regulatory compliance: Built-in features to support adherence to industry regulations.
- Operational efficiency: Reduction in downtime and waste, with improved resource utilization.
- Global standardization: Consistency in operations across plants, regardless of location.
- Enhanced decision-making: Data-driven insights to refine planning, scheduling, and forecasting.
- Better customer satisfaction: Faster delivery times and reliable quality outcomes.
Leveraging the capabilities of an MES enables manufacturers to achieve higher productivity, minimize risks, and drive profitability while ensuring long-term scalability and innovation. An MES resolves immediate operational pain points and positions manufacturers for future success through improved agility, enhanced analytics, and scalable technology infrastructure.
11 Considerations for Choosing an MES
Selecting the right MES is not just about addressing immediate manufacturing needs—it’s a strategic decision that will impact operational efficiency, scalability, and long-term growth. The process involves evaluating numerous factors to ensure the solution aligns with your unique workflows, compliance requirements, and business goals.
1. Define Your Business Needs
Understanding your business's unique requirements is the foundation of selecting an MES. Start by assessing your manufacturing goals, production challenges, and existing processes to determine the specific capabilities you need in a system.
Consider whether your operations prioritize high-volume production, customization, regulatory compliance, or advanced analytics. Do you need specific functionality like equipment integration, product traceability, or defect tracking? If you operate across multiple locations, assess whether centralized visibility is a priority.
Defining these needs ensures the MES you choose aligns with your operational goals and delivers measurable outcomes. A clear understanding of your priorities narrows your options and sets the stage for long-term success.
Key takeaway: The right MES starts with deeply understanding your operational pain points and strategic goals. Defining these allows you to focus on solutions that deliver tangible benefits and align with your growth trajectory.
2. Evaluate Customization Options
Manufacturing operations vary widely between industries, and a one-size-fits-all MES rarely delivers the efficiency and precision modern manufacturers require. Customization ensures the system adapts to your workflows rather than forcing your processes to fit rigid software constraints.
Look for an MES that allows configurable workflows, tailored reporting templates, and adjustable dashboards to meet the specific demands of your production environment. Assess whether the vendor offers industry-specific features, such as compliance tracking for medical devices or batch traceability for food manufacturing. This flexibility helps ensure the MES changes with your business, addressing current and future needs.
Standardization across facilities may also require some degree of customization. For companies managing multi-location operations, the ability to implement site-specific configurations without losing overarching visibility is critical. Flexibility in adapting to unique process flows can reduce the need for costly workarounds or third-party integrations.
Key takeaway: A customizable MES aligns directly with your processes, enabling seamless adoption and maximizing ROI. Systems that fail to adapt to your operations risk inefficiencies, employee resistance, and higher operational costs.
3. Assess Integration Capabilities
An MES does not operate in isolation—it must integrate seamlessly with your existing technology ecosystem. Manufacturing environments often involve a complex web of ERP systems , warehouse management systems (WMS), and various types of shop-floor equipment. Ensuring smooth integration is essential for leveraging the full potential of an MES.
Evaluate whether the MES supports standard integration protocols, such as APIs or OPC Unified Architecture (UA). Compatibility with your existing ERP is especially critical, as these systems often share production schedules, inventory, and order fulfillment data. Additionally, assess whether the MES can communicate with legacy equipment and newer Industry 4.0 technologies like IoT devices or predictive maintenance tools.
Effective integration minimizes data silos, enabling real-time data flow across all connected systems. This connectivity drives more informed decision-making and reduces manual interventions, increasing operational efficiency.
Key takeaway: The MES you choose should integrate effortlessly with existing systems and equipment to create a unified ecosystem. Poor integration can lead to costly delays, inefficiencies, and missed opportunities for optimization.
4. Consider Scalability Features
Manufacturing is rarely static, and your MES should accommodate current and future needs. Scalability ensures the system can support business growth through increased production volume, new product lines, or expanding operations across multiple sites.
Cloud-based MES solutions often provide the most flexible scalability. These systems allow you to add users, modules, or functionalities without significant infrastructure investment. On-premise solutions, while still viable for some manufacturers, may lack this flexibility and require costly upgrades to expand capabilities.
Scalability is significant for industries experiencing seasonal production peaks or unpredictable demand fluctuations. A robust MES should handle workload surges without compromising performance, ensuring seamless operations regardless of production demands.
Key takeaway: A scalable MES grows with your business, preventing costly system replacements and ensuring long-term alignment with your operational goals.
5. Prioritize Regulatory Compliance
For manufacturers in regulated industries, compliance is non-negotiable. An MES must include features that enable traceability, documentation, and audit readiness to facilitate adherence to industry standards and legal requirements.
Evaluate whether the system offers automated record-keeping, electronic signatures, and audit trail functionality. For example, medical device manufacturers may require compliance with ISO 13485 or FDA 21 CFR Part 11, while automotive manufacturers may need features supporting IATF 16949 standards. Ensure the MES can handle regional and global regulations if your business operates across multiple jurisdictions.
Non-compliance can lead to severe penalties, operational disruptions, or damage to your reputation. An MES with built-in compliance features reduces the risk of human error and simplifies the process of maintaining regulatory standards.
Key takeaway: Choose an MES with comprehensive compliance tools tailored to your industry, safeguarding your business against legal and operational risks.
6. Analyze Cost vs ROI Potential
Investing in an MES requires careful consideration of both initial costs and long-term returns. While upfront expenses such as licensing fees, implementation, and training are essential, the system's ability to deliver measurable benefits over time is the fundamental determinant of its value.
Begin with a detailed cost analysis that includes both direct and indirect expenses. Direct costs encompass software licenses, hardware (if needed), and consulting fees. Indirect costs, such as lost productivity during implementation or maintenance requirements, should also be considered. Balance these expenses against the potential ROI, including reductions in downtime, enhanced quality control, and improved productivity.
A strong MES often pays for itself through operational efficiencies. For instance, reducing scrap rates, minimizing errors, and accelerating production cycles directly impact the bottom line. Evaluate whether the vendor provides ROI estimates or case studies showcasing measurable outcomes from similar deployments in your industry.
Key takeaway: Choose an MES that delivers long-term value through enhanced efficiency and measurable financial gains. An upfront investment that results in sustained cost savings and increased productivity ensures the system pays for itself over time.
7. Review Vendor Support Quality
The success of an MES implementation depends heavily on the level of support the vendor provides. Comprehensive training, prompt troubleshooting, and proactive updates are essential for ensuring smooth operations after deployment.
Research the vendor’s reputation for customer service, including response times and problem-resolution rates. Evaluate whether they offer dedicated support teams, live assistance, or self-service resources. Some vendors provide additional services like continuous training or on-site visits, which can be invaluable during the early stages of adoption.
Ongoing support is equally important. You may require system updates, additional training, or new integrations. A vendor with a proven track record for long-term partnership ensures your MES remains relevant and functional as your business grows.
Key takeaway: Reliable vendor support ensures seamless adoption and consistent performance, minimizing downtime and maximizing the system’s effectiveness.
8. Plan Implementation Timeline
A well-structured implementation plan minimizes disruptions and ensures a successful MES rollout. Before selecting a system, assess whether the vendor provides a clear timeline with milestones and deliverables. An accelerated implementation may be beneficial but should not come at the expense of system reliability or thorough testing.
Collaborate with stakeholders to align the timeline with production schedules, ensuring minimal impact on operations. A phased rollout, where the MES is deployed to select departments or locations before full implementation, can help identify potential challenges early.
An effective timeline should include post-implementation support, user training and initial troubleshooting. Ensuring your team is comfortable with the system prevents delays and maximizes its impact.
Key takeaway: A realistic implementation plan tailored to your operations ensures a smooth transition and reduces downtime, allowing you to achieve faster results without compromising reliability.
9. Ensure Security Standards Compliance
As manufacturing highly relies on digital systems, cybersecurity has become a critical consideration. An MES must protect sensitive production data, intellectual property, and customer information from potential breaches or cyberattacks.
Choose a system with robust security features, including data encryption, user authentication, and role-based access controls. If the MES is cloud-based, confirm that it complies with industry security standards such as ISO 27001 or SOC 2. Manufacturers handling government contracts or regulated industries should also evaluate the system’s compliance with regional standards, such as ITAR or GDPR.
Proactive security measures prevent costly disruptions and protect your business’s reputation. Additionally, built-in disaster recovery and backup capabilities ensure operational continuity during a cyber incident.
Key takeaway: A secure MES protects critical data and operations from external threats, safeguarding your business and reputation.
10. Monitor Analytics and Reporting Tools
Real-time analytics and robust reporting capabilities are essential features of any MES. These tools provide actionable insights that help manufacturers identify inefficiencies, track performance, and make informed decisions.
Look for systems with customizable dashboards, automated reporting, and real-time data visualization. Advanced analytics capabilities, such as predictive maintenance or quality trend analysis, enhance decision-making and operational efficiency.
An effective MES should integrate with business intelligence platforms to consolidate data from multiple sources. This integration enables a holistic view of operations, empowering leadership teams to develop strategies based on accurate, real-time information.
Key takeaway: An MES with strong analytics and reporting capabilities enhances visibility, supports informed decision-making, and drives continuous improvement in manufacturing processes.
11. Align with Long-Term Business Goals
Selecting an MES is not just a tactical decision—it’s a strategic investment. The system must align with your company’s long-term objectives, such as scaling production, entering new markets, or adopting emerging technologies like IoT or AI.
Evaluate whether the MES vendor offers a roadmap for future enhancements, including new modules or integrations. A system that changes with your business ensures sustained value and eliminates the need for costly replacements. Consider how the MES can support broader goals, such as sustainability initiatives or digital transformation strategies.
When an MES aligns with your vision, it becomes a foundational tool for achieving both short-term gains and long-term growth.
Key takeaway: An MES that supports your long-term objectives ensures scalability and sustained competitiveness, enabling your business to adapt.
Considerations when choosing an MES should address a specific element of manufacturing complexity, from ensuring seamless system integration to prioritizing regulatory compliance and long-term scalability. Whether you operate a single facility or manage global operations, selecting the best MES is critical to driving measurable improvements and supporting your growth vision.
Measuring Successful MES Implementation
A successful MES implementation is measured by how well it integrates into existing operations and by the tangible improvements it delivers over time. Key performance indicators (KPIs) provide a clear framework for evaluating the system’s impact on productivity, quality, and overall operational efficiency.
Critical metrics to track include production cycle times, defect rates, and equipment utilization rates. For companies focusing on compliance, metrics like audit readiness and traceability coverage are essential indicators of success. Employee adoption rates should also be monitored to ensure the system is used effectively across departments.
Beyond immediate metrics, the accurate measure of success lies in how well the MES supports long-term goals. For instance, improved scalability, better decision-making enabled by real-time analytics, and enhanced customer satisfaction reflect the broader value of a well-chosen MES. Regularly revisiting these metrics ensures the system continues to align with business objectives, providing sustained benefits over time.
Manufacturers worldwide embrace cloud-based solutions to achieve efficiency, precision, and scalability. At 42Q, we combine decades of manufacturing expertise with cutting-edge technology to deliver smart connected manufacturing. Our flexible, cloud-native MES platform enhances visibility, streamlines operations, and accelerates digital transformation. Discover how our solutions can empower your factory to achieve its full potential.
Key Takeaways
- Identifying specific business needs ensures the MES aligns with your manufacturing goals and addresses unique challenges effectively.
- Customizable and scalable MES platforms support long-term growth by adapting to changing processes and production demands.
- Seamless integration with existing ERP systems, IoT devices, and legacy equipment maximizes the value of the MES.
- Built-in compliance features ensure regulatory requirements are met, reducing risks and maintaining operational continuity.
- Real-time analytics and robust reporting tools empower data-driven decision-making and continuous process improvement.
FAQs
An MES is designed to monitor and manage manufacturing processes in real time, bridging the gap between enterprise resource planning systems and shop-floor operations. It ensures production efficiency, enforces quality standards, and provides actionable insights to optimize workflows.
MES software automates manual processes, tracks real-time production data, and identifies inefficiencies such as downtime or bottlenecks. This leads to faster cycle times, reduced waste, and better resource utilization, making operations more efficient and cost-effective.
Industries like automotive, aerospace, medical devices, and consumer electronics see significant value from an MES due to their need for traceability, quality control, and compliance. However, any manufacturer aiming to streamline production and improve scalability can benefit.
A cloud-based MES offers greater scalability, faster deployment, and reduced upfront costs compared to on-premise systems. It also enables global visibility and real-time access to data, making it ideal for multi-plant or growing businesses.
Focus on integration capabilities, customization options, scalability, compliance features, and ROI potential. These elements ensure the MES aligns with your operational goals and supports current and future business needs.