13 Benefits of Computerized Maintenance Management Systems (CMMS)
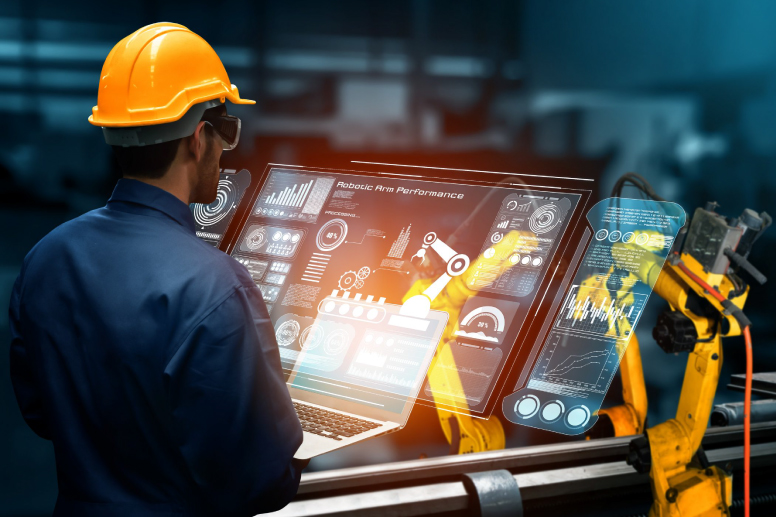
13 Benefits of Computerized Maintenance Management Systems (CMMS)
A CMMS eliminates the inefficiencies of manual maintenance tracking, ensuring that equipment remains reliable, costs stay controlled, and operational disruptions are minimized.
Due to disorganized scheduling, businesses that rely on outdated maintenance methods often face unexpected breakdowns, high repair expenses, and lost productivity. A structured approach to maintenance improves efficiency, extends asset lifespan, and enhances decision-making.
Implementing a CMMS helps businesses optimize work order management, track asset performance in real time, and reduce maintenance-related administrative burdens. With a centralized platform that automates preventive maintenance and streamlines reporting, organizations can achieve greater control over maintenance processes while reducing downtime and operational costs.
What is a CMMS?
A Computerized Maintenance Management System (CMMS) is a software solution designed to streamline and automate maintenance operations across industries. It provides a centralized platform for scheduling, tracking, and managing maintenance tasks, ensuring that assets and equipment remain in optimal working condition. CMMS software replaces traditional paper-based maintenance tracking with a digital system, allowing real-time monitoring, work order management, and historical data analysis.
By implementing a CMMS, organizations gain better control over preventive maintenance, reducing equipment failures and unplanned downtime. The system stores comprehensive asset records, tracks work orders, manages inventory, and provides analytics to improve decision-making. Industries such as manufacturing, healthcare, facility management, and transportation rely on CMMS to enhance operational efficiency, extend equipment life, and maintain compliance with regulatory requirements.
Why CMMS is Important
Effective maintenance management directly affects operational efficiency, cost savings, and asset longevity. A CMMS eliminates the inefficiencies of manual tracking, helping businesses organize maintenance tasks, reduce downtime, and ensure equipment reliability. Without a structured system, unplanned failures lead to production delays, unexpected repair costs, and unnecessary administrative work.
A well-implemented CMMS provides a centralized database that keeps track of maintenance schedules, work orders, asset history, and inventory. This level of organization helps reduce errors, prevent missed maintenance, and improve compliance with safety regulations. Businesses that invest in a CMMS gain greater visibility into asset performance, making it easier to allocate resources, plan preventive maintenance, and extend the useful life of critical equipment.
13 Benefits of CMMS
A CMMS provides structured maintenance management, ensuring that assets remain in peak condition while minimizing operational disruptions. Organizations that rely on outdated tracking methods face unnecessary downtime, excessive repair costs, and inefficient scheduling. A well-implemented CMMS centralizes asset data, optimizes work orders, and automates maintenance planning to improve efficiency.
1: Organized Maintenance Scheduling
Unplanned maintenance leads to unexpected downtime, costly repairs, and inefficient resource allocation. A CMMS eliminates these risks by automating preventive maintenance schedules, ensuring critical equipment receives servicing at the proper intervals.
Automated scheduling reduces the reliance on manual tracking, preventing missed inspections that could lead to mechanical failures. Maintenance teams receive real-time alerts for upcoming tasks, allowing them to allocate resources efficiently and avoid last-minute disruptions. Standardizing maintenance timelines improves asset reliability and extends equipment lifespan, ultimately lowering operational costs.
2: Access to Asset Information in Real Time
Maintenance decisions require accurate and immediate asset data. A CMMS provides instant access to equipment specifications, maintenance history, warranty details, and real-time performance updates, eliminating the inefficiencies of manual record-keeping.
Technicians no longer need to search paper logs or spreadsheets to retrieve asset information. With digital access to comprehensive records, they can diagnose issues faster, perform timely maintenance, and reduce unnecessary downtime. Having real-time visibility into asset conditions improves response times and enhances operational efficiency.
3: Superior Work Order and Request Management Capabilities
Manual work order management leads to miscommunication, scheduling conflicts, and delays in task completion. A CMMS streamlines this process by automating work order creation, assignment, and tracking, ensuring that maintenance requests are processed efficiently.
Technicians receive detailed instructions, priority levels, and asset histories within the system, eliminating confusion and reducing response times. Digital tracking improves accountability by providing clear timelines and completion records. Efficient work order management enhances team coordination, leading to faster repairs and optimized resource allocation.
4: Streamlined Tracking of Cost and Purchase Orders
Uncontrolled maintenance expenses and inefficient purchasing processes lead to unnecessary spending. A CMMS records all maintenance-related costs, tracks purchase orders, and provides visibility into spending trends.
With accurate cost tracking, organizations can identify budget overruns, analyze repair versus replacement costs, and forecast future expenses. The system ensures that spare parts are reordered before stock levels become critically low, preventing equipment downtime due to unavailable components. A structured financial approach to maintenance leads to better cost control and improved financial planning.
5: Less Administrative Hassle
Managing maintenance operations with paper-based systems or spreadsheets increases administrative workload, leading to data entry errors and inefficient reporting. A CMMS reduces these burdens by automating routine administrative tasks, allowing maintenance staff to focus on operational priorities.
Automated record-keeping simplifies compliance documentation, work order processing, and asset tracking. Instead of manually logging repairs and inventory updates, technicians input data directly into the system, ensuring accuracy and consistency. Reducing administrative tasks increases productivity and allows maintenance teams to concentrate on keeping equipment in optimal condition.
6: Simplified Record-Keeping
Accurate record-keeping is essential for compliance, audits, and long-term asset management. A CMMS maintains a comprehensive history of all maintenance activities, including repairs, inspections, and part replacements, ensuring that data is readily available when needed.
Digitized records eliminate the risk of lost paperwork and inconsistencies in maintenance logs. Businesses can track asset performance over time, identifying patterns that help refine maintenance strategies. Well-organized documentation supports regulatory compliance and improves planning for future maintenance needs.
7: Reduced Downtime
Unscheduled downtime disrupts operations, reduces productivity, and increases costs. A CMMS minimizes downtime by optimizing maintenance schedules, detecting issues before failures occur, and ensuring that necessary repairs are completed on time.
Preventive maintenance strategies keep equipment running smoothly, reducing the likelihood of sudden breakdowns. When repairs are required, the system prioritizes urgent work orders and ensures that technicians have access to asset histories, streamlining the repair process. Improved maintenance planning keeps production schedules on track and prevents revenue losses caused by unexpected outages.
8: Increased Equipment Longevity
Equipment failure often results from inadequate maintenance or delayed servicing. A CMMS prevents premature wear by enforcing structured maintenance plans based on manufacturer recommendations and operational usage.
Regular servicing reduces the strain on machinery, preventing minor issues from escalating into significant failures. Tracking asset conditions and scheduling timely inspections help businesses extend the lifespan of critical equipment. Longer-lasting assets reduce capital expenditures, lowering the frequency of costly replacements and improving overall return on investment.
9: Reduced Maintenance Backlog
A growing maintenance backlog results in delayed repairs, asset inefficiencies, and increased downtime. A CMMS prevents this by automating work order prioritization, ensuring that urgent tasks are completed without unnecessary delays.
Maintenance teams gain visibility into pending tasks, allowing them to manage workloads effectively. Preventive maintenance reduces the accumulation of overdue repairs, ensuring that equipment remains operational. Keeping maintenance schedules organized improves productivity and prevents disruptions caused by neglected servicing.
10: Streamlined Reporting
Maintenance data is only valuable when it leads to actionable insights. A CMMS generates detailed reports on work order completion rates, asset performance, and cost tracking, helping organizations refine their maintenance strategies.
Comprehensive reporting highlights inefficiencies, identifies recurring equipment issues, and supports budget planning. Decision-makers gain a clear understanding of maintenance trends, allowing them to allocate resources effectively. Data-driven insights improve long-term planning and help businesses optimize maintenance operations.
11: Accessibility to Historic Data
Analyzing past maintenance records provides valuable insights into asset performance and servicing patterns. CMMS stores complete maintenance histories, allowing organizations to track repairs, part replacements, and operational trends.
Having access to detailed records simplifies troubleshooting, as technicians can reference past issues to diagnose current problems. Historical data also helps organizations determine the most effective maintenance schedules, improving efficiency and reducing repair costs. Well-documented records support better long-term asset management and operational planning.
12: Improved Team Communication
Effective communication between maintenance teams, technicians, and management ensures that work orders are processed efficiently and equipment servicing remains on schedule. A CMMS provides a centralized platform for tracking task status, sharing updates, and coordinating responsibilities.
Technicians receive real-time updates on task assignments, reducing the risk of duplicated efforts or miscommunication-related delays. Managers can monitor maintenance progress, ensuring that high-priority tasks receive immediate attention. Strengthened communication improves workflow efficiency and enhances overall team coordination.
13: Enhanced Employee Morale
A structured maintenance system benefits not only equipment performance but also workforce efficiency. A CMMS reduces frustration caused by unclear work orders, last-minute emergency repairs, and inefficient task management.
Technicians operate more effectively when they have precise maintenance schedules, access to asset histories, and well-defined responsibilities. Reducing unplanned repairs and administrative workload improves job satisfaction, creating a more productive work environment. A well-organized system increases morale and enhances overall operational efficiency.
A CMMS offers measurable benefits that improve maintenance effectiveness, extend asset longevity, and optimize operational costs. Organizations that invest in structured maintenance management gain better visibility into equipment performance, reduce unexpected failures, and improve overall productivity.
Financial Benefits of CMMS
A well-implemented CMMS directly impacts financial performance by reducing maintenance costs, optimizing resource allocation, and extending asset life. Businesses that rely on outdated maintenance tracking methods often face excessive repair expenses, unplanned downtime, and inefficient labor management. Implementing a structured maintenance system improves cost control and increases operational efficiency.
A CMMS reduces maintenance expenses by automating preventive maintenance schedules, minimizing emergency repairs, and improving inventory management. Tracking asset performance and maintenance history helps identify cost-saving opportunities, such as reducing over-maintenance or strategically planning equipment replacements. Improved work order management reduces labor inefficiencies, ensuring maintenance teams complete tasks efficiently without unnecessary delays.
Long-term cost savings come from increased equipment longevity and reduced downtime. Keeping assets in peak condition prevents expensive breakdowns and lowers capital expenditures on premature replacements. A CMMS provides data-driven insights that help businesses plan maintenance budgets effectively, reducing unexpected expenses and improving overall financial stability.
Best Practices for Implementing CMMS Systems
A successful CMMS implementation requires careful planning and execution to maximize its benefits. Poor setup and inadequate training often lead to underutilization, which requires following best practices to ensure a smooth transition and long-term success.
- Define Clear Objectives: Establish goals for the CMMS, such as reducing downtime, improving work order efficiency, or lowering maintenance costs. Clear objectives guide system configuration and ensure alignment with business needs.
- Involve Key Stakeholders: Engage maintenance teams, IT personnel, and management early in the process. Their input helps customize the system to match operational requirements and ensures widespread adoption.
- Conduct a Comprehensive Asset Inventory: Gather detailed asset data, including maintenance history, specifications, and manufacturer recommendations. Accurate records improve scheduling and asset management.
- Standardize Workflows and Processes: Establish consistent work order management, preventive maintenance, and inventory tracking procedures. Standardization enhances efficiency and minimizes confusion.
- Provide Adequate Training: Ensure technicians, supervisors, and administrators receive thorough training on system functionality. Well-trained users maximize the CMMS’s potential and prevent misuse.
- Ensure Data Accuracy: Verify that asset details, maintenance schedules, and historical records are correct before migration. Inaccurate data leads to inefficiencies and unreliable reporting.
- Set Up Automated Alerts and Notifications: Configure automated reminders for preventive maintenance, overdue work orders, and inventory restocking. These alerts help maintenance teams stay proactive.
- Monitor Key Performance Indicators (KPIs): Track essential metrics such as work order completion rates, downtime reduction, and maintenance costs. Continuous monitoring allows for ongoing system improvements.
- Integrate with Other Business Systems: Connect the CMMS with enterprise resource planning (ERP) software, procurement systems, and inventory management tools to streamline workflows and improve data accuracy.
- Perform Regular System Audits: Review CMMS usage periodically to identify gaps, improve efficiency, and adjust maintenance strategies. System audits help maintain long-term effectiveness.
Following these best practices ensures that a CMMS delivers measurable improvements in maintenance efficiency, cost savings, and asset performance. Proper planning and ongoing optimization help businesses maximize their return on investment while maintaining a well-organized and effective maintenance strategy.
Manufacturers worldwide are adopting cloud-based solutions to improve efficiency, accuracy, and scalability. At 42Q, we combine decades of manufacturing expertise with innovative technology to deliver smart connected manufacturing. Our flexible, cloud-native MES platform enhances visibility, streamlines operations, and accelerates digital factory transformation. Explore how our solutions can optimize your factory’s performance and drive measurable results.
Key Takeaways
- A CMMS automates preventive maintenance scheduling, reducing downtime and preventing unexpected equipment failures.
- Real-time asset tracking improves efficiency, helping maintenance teams diagnose and resolve issues faster.
- Automated work order management streamlines task assignments, improves communication, and enhances team productivity.
- Tracking maintenance costs and inventory prevents budget overruns and ensures essential supplies are always available.
- Data-driven reporting helps businesses analyze trends, optimize maintenance strategies, and improve long-term asset management.
FAQs
A CMMS improves maintenance efficiency by automating scheduling, tracking asset performance, and managing work orders. It reduces downtime, extends equipment lifespan, and helps control costs by optimizing resource allocation. Businesses also benefit from streamlined reporting, real-time data access, and better compliance with maintenance regulations.
Automated preventive maintenance schedules prevent costly emergency repairs and unexpected breakdowns. A CMMS tracks maintenance expenses, analyzes repair versus replacement costs, and ensures that parts and supplies are efficiently managed. This structured approach lowers unnecessary spending while extending the life of critical equipment.
Many CMMS solutions integrate with enterprise resource planning (ERP) systems, procurement software, and inventory management tools. Integration ensures seamless data flow, allowing businesses to synchronize maintenance operations with broader financial and operational strategies. This connectivity enhances efficiency and eliminates manual data entry errors.
Manufacturing, healthcare, facility management, and transportation industries benefit significantly from CMMS implementation. Any organization that relies on machinery, equipment, or infrastructure maintenance can improve efficiency, reduce downtime, and optimize maintenance schedules with a CMMS.
A CMMS maintains detailed records of maintenance history, inspections, and repairs, helping businesses meet regulatory requirements. Digitized record-keeping ensures that compliance documentation is always up to date, simplifying audits and reducing the risk of penalties due to incomplete maintenance records.