15 MES Applications by Industry
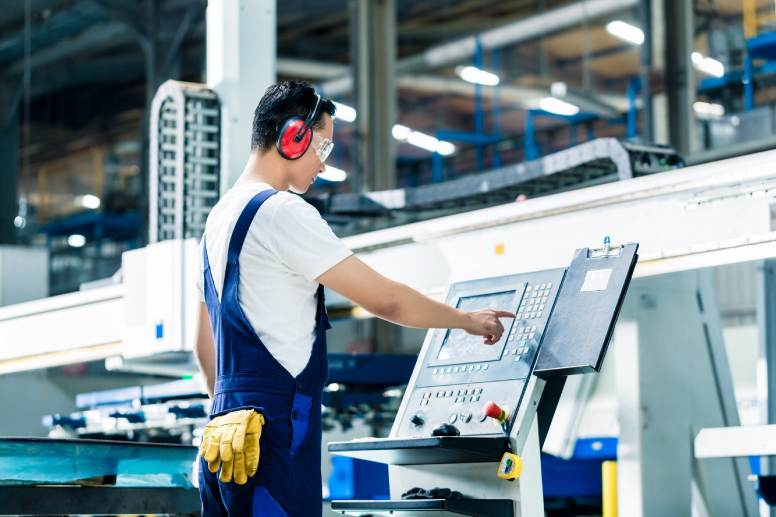
15 MES Applications by Industry
Manufacturers constantly seek ways to improve efficiency, reduce costs, and maintain high-quality production standards.
Manufacturing Execution Systems (MES) provide a critical solution by integrating real-time monitoring, automation, and data analytics into production workflows. These applications help manufacturers across various industries track production, optimize resource utilization, and ensure compliance with industry regulations. With the ability to reduce waste, improve traceability, and enhance operational control, MES applications play a key role in modernizing manufacturing and driving long-term growth.
Importance of MES in Manufacturing
Manufacturing Execution Systems (MES) play an essential role in modern production by connecting, monitoring, and controlling complex manufacturing processes. These systems bridge the gap between enterprise resource planning (ERP) and production equipment, ensuring accurate data flow and operational efficiency. As industries strive for greater agility, MES applications provide real-time insights that help you minimize downtime, improve quality, and maximize production output.
Integrating MES applications supports key operational areas, including production scheduling, traceability, quality management, and resource allocation. MES applications make data-driven by providing a centralized view of manufacturing activities, reducing errors, and optimizing workflows. This level of control is significant for industries that rely on precision and compliance, such as automotive, medical devices, and aerospace.
Beyond immediate operational improvements, MES applications also contribute to long-term scalability and cost reduction. With greater visibility into production processes, manufacturers can identify inefficiencies, enhance workforce productivity, and respond more effectively to fluctuations. These advantages make MES applications a critical investment for companies looking to optimize their operations and remain adaptable in data-driven manufacturing.
15 MES Applications by Industry
Manufacturing Execution Systems (MES) provide essential tools for industries that require precision, compliance, and efficiency in production. These applications help manufacturers monitor production in real-time, automate quality control, and improve operational workflows. Below are 15 MES applications categorized by industry, each addressing unique challenges while optimizing manufacturing processes.
Automotive Industry
Automotive manufacturers rely on MES applications to manage complex assembly lines, track components, and improve production efficiency. These systems help optimize workflows, minimize defects, and improve compliance with regulatory standards.
1. Real-Time Production Monitoring
Production inefficiencies result in lost time and increased operational costs. MES applications track production in real-time, collecting data from machinery and operators to identify bottlenecks, optimize throughput, and reduce delays. Manufacturers gain complete visibility into work orders, cycle times, and output, allowing quick adjustments that improve production efficiency.
Effective production monitoring also helps reduce scrap and rework. Immediate alerts notify operators of quality deviations, preventing defective parts from advancing further in the assembly process. This improves overall product consistency and reduces material waste.
2. Quality Assurance and Defect Tracking
Automotive manufacturers must maintain strict quality control throughout production. MES applications integrate with inspection systems to detect defects at early stages, preventing faulty parts from reaching final assembly. Real-time defect tracking making manufacturers to analyze failure trends, improving quality processes over time.
Detailed defect reports allow teams to implement corrective actions quickly, reducing scrap rates and minimizing the risk of expensive recalls. Capturing quality data at every step helps ensure compliance with automotive safety regulations while maintaining high production standards.
3. Traceability and Component Serialization
Manufacturers must track each component through the production cycle to ensure compliance with regulatory standards. MES applications provide full traceability by assigning serial numbers to components and recording their history, from supplier sourcing to final vehicle assembly.
Serialized traceability simplifies recall management by identifying specific batches of defective parts rather than requiring full-scale product recalls. This improves accountability while reducing liability risks for manufacturers and suppliers.
4. Just-in-Time (JIT) Inventory Management
Managing inventory efficiently prevents production delays and minimizes unnecessary costs. MES applications coordinate material deliveries with production schedules, ensuring that parts arrive when needed. This reduces excess stock, prevents shortages, and optimizes warehouse space.
Automated inventory tracking helps reduce lead times and improves supply chain reliability. Keeping inventory levels aligned with production grow minimizes waste while supporting lean manufacturing principles.
5. Workforce and Task Allocation
Optimizing labor allocation improves productivity and reduces idle time. MES applications assign tasks based on worker availability, skill levels, and production priorities, ensuring that each station operates efficiently.
Smart scheduling improves resource utilization by aligning work assignments with operational needs. Skill-based allocation reduces human errors, while digital work instructions provide operators with step-by-step guidance to improve efficiency.
Medical & Pharmaceutical Industry
Strict regulatory requirements make MES applications essential in medical and pharmaceutical manufacturing. These systems ensure compliance, track product quality, and improve documentation accuracy.
6. Electronic Batch Record (EBR) Management
Paper-based record-keeping increases the risk of human errors and non-compliance. MES applications digitize batch records, ensuring accurate and complete documentation for every production run.
Electronic batch records improve traceability and simplify audit preparation. Manufacturers can store, retrieve, and update production data in a centralized system, reducing paperwork and ensuring compliance with industry standards such as FDA 21 CFR Part 11.
7. Real-Time Process Monitoring
Precise control over production conditions ensures product safety and consistency. MES applications monitor temperature, pressure, and humidity in real-time, preventing deviations that could compromise product integrity.
Automated alerts notify operators of variations in process conditions, reducing the risk of contamination or defective batches. This level of monitoring supports Good Manufacturing Practices (GMP) and improves regulatory compliance.
8. Regulatory Compliance Support
Regulatory agencies require detailed production records and audit trails. MES applications automate compliance reporting, reducing the manual effort needed to prepare for audits.
Automated compliance tracking helps ensure that all manufacturing processes adhere to industry regulations. Digital logs provide transparency and prevent errors in documentation, reducing the risk of regulatory violations.
9. Equipment Calibration and Maintenance Tracking
Maintaining properly calibrated equipment is essential for consistent product quality. MES applications track calibration schedules and log maintenance activities to prevent equipment failures.
Automated maintenance reminders reduce unplanned downtime and extend asset lifespan. Preventive maintenance ensures machines operate at peak performance, supporting reliable and repeatable production processes.
10. Batch and Product Traceability
Tracking raw materials and final products improves product safety and recall management. MES applications provide complete traceability from ingredient sourcing to final packaging.
Automated traceability reduces risks associated with contamination or defects. When recalls are necessary, manufacturers can quickly identify affected batches, reducing financial losses and protecting consumer safety.
Food and Beverage Industry
Food manufacturers use MES applications to improve safety, maintain quality standards, and optimize production workflows. These systems provide real-time process monitoring and automate compliance tracking.
11. Recipe and Ingredient Management
Precision in ingredient measurements ensures product consistency. MES applications store digital recipes and track ingredient usage to prevent formulation errors.
Standardized recipe management reduces variability between batches. Automated recipe enforcement helps manufacturers maintain uniform product quality across different production facilities.
12. Food Safety and Compliance Tracking
Food manufacturers must meet strict safety regulations. MES applications monitor processing conditions, track ingredient sources, and automate compliance reporting.
Automated food safety tracking prevents contamination risks and simplifies regulatory audits. Digital logs provide proof of compliance with safety standards, reducing legal and financial risks for manufacturers.
13. Production Scheduling and Workflow Optimization
Optimizing production workflows improves efficiency and reduces operational costs. MES applications balance workloads, align production with market, and prevent bottlenecks.
Real-time scheduling adjustments help manufacturers meet order deadlines without unnecessary delays. Better workflow management improves labor efficiency and reduces raw material waste.
14. Waste Reduction and Yield Optimization
Minimizing waste lowers costs and improves profitability. MES applications analyze production data to identify inefficiencies, allowing manufacturers to optimize ingredient usage and reduce overproduction.
Data-driven insights help manufacturers refine processes to maximize yields. Reduced food waste improves sustainability efforts while increasing operational efficiency.
15. Packaging and Labeling Verification
Accurate labeling is essential for regulatory compliance and consumer safety. MES applications automate packaging processes, verifying ingredient lists, expiration dates, and nutritional information.
Automated label verification prevents mislabeling errors, reducing product recalls. Consistent labeling ensures that consumers receive accurate information while meeting compliance requirements.
Benefits of Implementing MES Applications
Manufacturing Execution Systems (MES) improve production efficiency, reduce operational costs, and enhance product quality by providing real-time visibility and process automation. These applications support manufacturers in industries where precision, compliance, and scalability are critical. Implementing MES applications leads to measurable improvements across production lines, supply chain operations, and workforce management.
- Improved Production Efficiency: Automating workflows reduces manual data entry, minimizes human errors, and accelerates production cycles. MES applications provide real-time monitoring of manufacturing activities, allowing manufacturers to identify bottlenecks and optimize machine utilization. A data-driven approach to production management helps reduce downtime, improve throughput, and streamline daily operations.
- Enhanced Product Quality and Traceability: Tracking materials, monitoring process parameters, and logging quality inspections at every production stage ensures consistent product quality. MES applications detect deviations in real-time, allowing operators to make immediate corrections. Full traceability simplifies compliance with industry regulations and improves response times for recalls or quality-related investigations.
- Cost Reduction Through Waste Minimization: Manufacturing waste leads to unnecessary costs and inefficiencies. MES applications analyze production data to identify where waste occurs, helping manufacturers adjust processes to improve material usage. Automating defect detection and optimizing workflows reduces scrap rates while ensuring that raw materials are used efficiently.
- Regulatory Compliance and Audit Readiness: Industries with strict compliance requirements benefit from automated documentation and compliance tracking. MES applications generate and store digital production records, ensuring that all manufacturing data is readily available for audits. Standardized reporting reduces the risk of regulatory violations and simplifies certification processes.
- Better Workforce Utilization: Assigning tasks based on skill levels, availability, and production priorities optimizes labor resources. MES applications automate workforce scheduling, reducing idle time and improving overall productivity. Digital work instructions help operators complete tasks more efficiently, reducing training time and minimizing errors.
- Seamless Integration With Supply Chain Operations: Synchronizing production schedules with material deliveries prevents disruptions caused by shortages or excess inventory. MES applications provide real-time updates on stock levels, helping manufacturers manage materials efficiently. Improved coordination between suppliers, manufacturers, and distributors ensures that production stays aligned with orders.
- Predictive Maintenance for Equipment Reliability: Equipment downtime disrupts production and increases costs. MES applications track machine performance data, detecting signs of wear or potential failures before breakdowns occur. Predictive maintenance reduces unplanned downtime, extends asset lifespan, and helps manufacturers maintain consistent production output.
- Scalability for Expanding Operations: Standardized processes and centralized data management allow manufacturers to scale operations without unnecessary complexity. Cloud-based MES applications provide multi-site visibility, allowing manufacturers to monitor and manage production across multiple facilities. Consistent workflows improve efficiency while supporting long-term growth.
Implementing MES applications allows manufacturers to improve efficiency, reduce operational risks, and maintain high-quality production standards. These systems provide a foundation for data-driven helping companies optimize resources while meeting industry compliance requirements. MES adoption supports manufacturers in achieving greater operational control, cost savings, and long-term scalability.
Future Trends in MES Applications
Manufacturing Execution Systems (MES) continue to move with advancements in automation, data analytics, and cloud computing. As manufacturers seek greater efficiency, flexibility, and visibility across operations, MES applications are integrating new technologies to meet industry grows.
Artificial intelligence (AI) and machine learning improve predictive analytics in MES applications, allowing manufacturers to optimize production scheduling, identify potential failures before they occur, and enhance quality control through automated defect detection. AI-driven insights help manufacturers make data-backed decisions that improve efficiency and reduce costs.
Cloud-based MES solutions provide multi-plant connectivity, allowing manufacturers to manage global operations through a centralized platform. Cloud deployment reduces infrastructure costs while ensuring real-time access to production data from any location. This shift supports manufacturers looking for scalable, remote-accessible solutions that improve collaboration between production sites.
Integration with the Industrial Internet of Things (IIoT) is improving data collection and equipment monitoring. Smart sensors connected to MES applications provide real-time machine performance data, helping manufacturers track overall equipment effectiveness (OEE), automate maintenance scheduling, and reduce unplanned downtime.
Augmented reality (AR) and digital twin technology enhance training and troubleshooting capabilities. AR-enabled MES applications allow technicians to visualize production processes, receive step-by-step guidance, and interact with digital representations of equipment for more efficient maintenance and problem-solving.
Cybersecurity is becoming a priority as MES applications handle increasing production data. Enhanced security features, including multi-factor authentication, encryption, and secure cloud storage, ensure manufacturers protect sensitive information while complying with industry regulations.
MES applications will continue integrating with emerging technologies to improve manufacturing efficiency, quality control, and supply chain coordination. As automation and data-driven processes advance, manufacturers will rely on MES solutions to maintain operational agility and optimize production.
Manufacturers worldwide embrace cloud-based solutions to achieve efficiency, precision, and scalability. At 42Q, we combine decades of manufacturing expertise with cutting-edge technology to deliver smart, connected manufacturing. Our flexible, cloud-native MES platform enhances visibility, streamlines operations, and accelerates digital transformation. Discover how our solutions can empower your factory to achieve its full potential.
Key Takeaways
- MES applications improve production efficiency by automating workflows, reducing errors, and optimizing machine utilization to minimize downtime and maximize output.
- Real-time monitoring and quality tracking enhance product consistency by detecting defects early and ensuring compliance with industry standards.
- Automated inventory and supply chain management prevent material shortages and overstocking, improving operational agility and cost efficiency.
- Regulatory compliance and audit readiness are simplified through digital records, automated reporting, and process standardization.
- Predictive maintenance features reduce equipment downtime by monitoring performance data and scheduling proactive maintenance before failures occur.
FAQs
An MES application is a software solution that monitors, tracks, and controls production processes in real time. It provides manufacturers with visibility into operations, automates data collection, and optimizes production workflows to improve efficiency and quality.
MES applications reduce manual data entry, minimize errors, and streamline workflows by automating production monitoring and scheduling. Real-time insights help manufacturers identify bottlenecks, allocate resources effectively, and minimize downtime to improve overall efficiency.
Industries such as automotive, aerospace, medical devices, food and beverage, and electronics manufacturing benefit significantly from MES applications. These sectors require precision, regulatory compliance, and real-time traceability, all of which MES applications provide.
MES applications automate documentation, track production data, and generate audit-ready reports. By maintaining digital records and enforcing process controls, MES solutions help manufacturers meet regulatory requirements in industries with strict compliance standards.
MES focuses on shop floor execution, providing real-time visibility into production processes, equipment performance, and quality control. ERP systems manage broader business functions such as finance, procurement, and supply chain management. Integrating MES with ERP ensures seamless coordination between production and enterprise operations.