7 Benefits of Traceability in Manufacturing
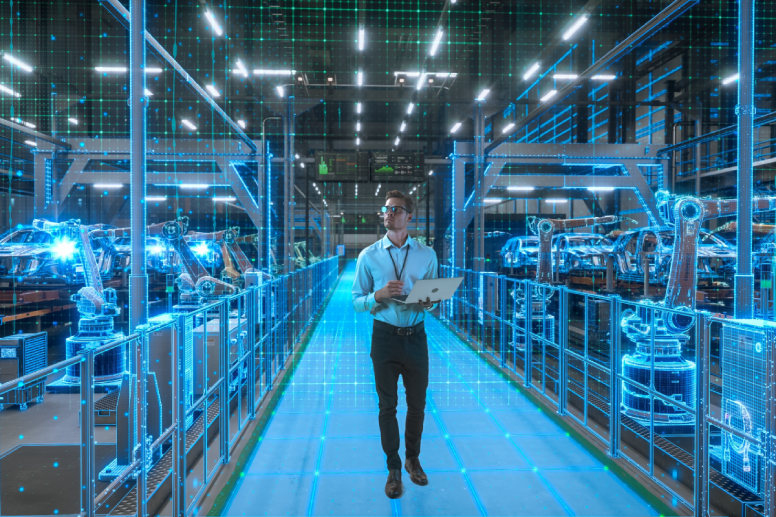
7 Benefits of Traceability in Manufacturing
Manufacturing traceability is one of the most effective strategies for achieving operational excellence while meeting rising demands for transparency and accountability.
It enables manufacturers to track every aspect of a product’s lifecycle, from sourcing raw materials to delivering the final product, offering unparalleled insights into production workflows. As industries highly prioritize quality, compliance, and efficiency, implementing traceability systems has become essential for optimizing processes, safeguarding reputation, and ensuring customer satisfaction.
What is Traceability in Manufacturing?
Traceability in manufacturing refers to the ability to track and document every stage of a product's lifecycle, from sourcing raw materials to final delivery. This process encompasses capturing data related to production, assembly, testing, and distribution, creating a detailed and comprehensive product history. With manufacturing traceability, businesses ensure every component and process is accounted for, providing the visibility needed to identify inefficiencies, maintain compliance with industry standards, and enhance overall operational effectiveness.
At its core, traceability focuses on building transparency throughout the supply chain by ensuring seamless information flow. This clarity plays a crucial role in mitigating production risks, reducing quality control issues, and improving accountability. Manufacturing traceability benefits extend beyond operations, as it also strengthens relationships with stakeholders by providing confidence in the accuracy and reliability of the production process.
Why Traceability in Manufacturing Matters
Traceability is an essential factor in maintaining operational efficiency and protecting product quality in manufacturing environments. It serves as a cornerstone for achieving compliance with strict regulatory requirements, improving workflow transparency, and addressing operational risks before they escalate. By enabling manufacturers to retain accurate and detailed records at every stage of production, traceability fosters proactive decision-making and continuous process improvement. These benefits of traceability in manufacturing contribute directly to a company’s ability to meet customer expectations and adhere to industry demands.
Furthermore, manufacturing traceability benefits include safeguarding brands from financial and reputational risks tied to recalls and quality failures. Traceability systems help manufacturers quickly trace and isolate issues without interrupting production lines, ensuring that operations continue without compromise. This level of accountability is essential for meeting the expectations of regulators, supply chain partners, and consumers who demand greater visibility into the origins and handling of products.
7 Benefits of Traceability in Manufacturing
Traceability in manufacturing is a critical enabler of operational excellence, regulatory compliance, and customer trust. It provides manufacturers with the tools to monitor and document every step of production, from sourcing raw materials to delivering finished products. This capability enhances visibility across the supply chain, ensures adherence to quality standards, and supports faster decision-making when issues arise. As industries continue to demand higher levels of accountability and transparency, traceability emerges as an essential practice, not just an advantage.
The benefits of traceability in manufacturing extend beyond quality control. Organizations can improve efficiency, reduce operational risks, and respond more effectively to market needs. Whether it’s minimizing the costs associated with product recalls or building confidence with consumers through transparency, traceability creates tangible value across all levels of operations. This overview highlights the seven most significant benefits that traceability brings to manufacturing environments, underscoring its role in driving success.
1. Improves Product Quality and Consistency
Consistent product quality is essential for manufacturers operating in highly regulated industries. Traceability systems enable real-time monitoring of production processes, allowing manufacturers to identify deviations or anomalies at any stage. This capability minimizes defects and enhances the uniformity of outputs, creating products that consistently meet quality standards.
Detailed tracking of materials, equipment usage, and operator activities allows manufacturers to pinpoint the root causes of defects. Identifying and resolving recurring issues leads to continuous improvement, reducing waste and strengthening production reliability. Manufacturers can elevate customer satisfaction and reduce the financial losses associated with defective goods by standardizing quality assurance across the entire production cycle.
2. Enhances Supply Chain Transparency
The modern supply chain often involves multiple vendors, geographies, and production sites, creating a complex ecosystem of interdependencies. Traceability simplifies this complexity by providing an end-to-end view of material and product flows, ensuring stakeholders can monitor every step in real-time. Transparency reduces the risks of delays, miscommunication, and inefficiencies while fostering greater accountability among suppliers and partners.
Supply chain visibility ensures manufacturers can trace raw materials back to their source, confirming compliance with ethical and regulatory standards. Additionally, clear documentation enables businesses to identify and resolve potential disruptions quickly, avoiding costly downtime. This level of oversight strengthens supply chain resilience and improves collaboration across all tiers of the manufacturing network.
3. Reduces Recall Costs and Risks
Product recalls are one of the most significant financial and reputational risks manufacturers face. Traceability systems allow manufacturers to act quickly and decisively when issues arise, effectively isolating affected products. This targeted approach significantly reduces the scale and costs of recalls compared to less efficient methods.
The ability to trace products and materials back through the production process streamlines investigations into quality or safety concerns. Manufacturers can respond swiftly to regulatory inquiries, mitigating potential penalties and reinforcing consumer trust. Minimizing recall-related expenses also protects the bottom line, helping manufacturers allocate resources toward innovation and growth.
4. Facilitates Regulatory Compliance
Industries such as automotive, aerospace, and medical devices must adhere to stringent regulatory standards to ensure product safety and reliability. Traceability systems provide the documentation and tracking capabilities necessary to meet these requirements. Detailed records of material origins, production conditions, and testing data make compliance audits seamless and efficient.
Manufacturers that invest in traceability systems demonstrate their commitment to accountability and responsibility. This proactive approach reduces the risk of legal penalties, delays, or loss of certifications. Meeting compliance standards consistently also strengthens relationships with customers, partners, and regulators, enhancing a manufacturer’s reputation as a reliable and ethical business.
5. Boosts Operational Efficiency
Operational inefficiencies can result in costly delays, wasted materials, and dissatisfied customers. Traceability offers manufacturers the tools to optimize production by identifying workflow bottlenecks and inefficiencies. Access to real-time data enables teams to make quick adjustments, ensuring processes run smoothly, and resources are used effectively.
Efficiency gains from traceability extend to inventory management, as manufacturers can monitor stock levels, reduce waste, and prevent overproduction. These improvements lower operational costs and enhance production speed without compromising quality. A streamlined, efficient operation ultimately positions manufacturers to respond more effectively to market demands and customer expectations.
6. Enables Improved Decision Making
Traceability systems generate a wealth of data manufacturers can use to improve decision-making processes. Analyzing this data helps identify trends, anticipate challenges, and identify growth opportunities. Manufacturers can optimize production schedules, fine-tune resource allocation, and predict maintenance needs based on historical insights.
The strategic use of traceability data empowers businesses to move away from reactive problem-solving and toward proactive planning. Decision-making backed by reliable data reduces risks and enhances outcomes across production, quality control, and supply chain management. This level of precision drives innovation and keeps manufacturers innovative.
7. Strengthens Customer Trust and Brand Reputation
Modern customers value transparency and accountability, and manufacturers that can demonstrate these qualities gain a significant edge. Traceability systems ensure manufacturers can provide customers with detailed information about product origins, quality assurance, and compliance with ethical standards. This visibility builds trust and reassures consumers that their purchases align with their values.
Establishing a reputation for transparency and reliability strengthens customer loyalty and boosts brand reputation. A manufacturer’s ability to respond effectively to quality concerns or recalls reinforces its commitment to consumer safety. By prioritizing trust and accountability, businesses can differentiate themselves in crowded markets and secure long-term customer relationships.
Traceability is a vital component for manufacturers striving to achieve higher standards in quality, compliance, and operational efficiency. It empowers businesses to address challenges with confidence, mitigate risks, and deliver consistent results that align with customer and regulatory expectations. Through its ability to streamline processes, reduce costs, and foster trust, traceability plays an indispensable role in strengthening supply chain performance and positioning manufacturers as reliable and ethical leaders in their industries.
Organizations adopting traceability systems are better equipped to adapt to demands while safeguarding their brand reputation. With the right tools and processes in place, manufacturers can create a culture of accountability and precision that fuels long-term growth. Traceability ensures manufacturers remain agile, proactive, and prepared to meet the challenges and opportunities.
Implementing a Scalable Manufacturing Traceability System
Implementing a scalable traceability system in manufacturing requires careful planning and the right technology to ensure success. A robust traceability solution should provide real-time visibility, integrate seamlessly with existing systems, and adapt to the unique needs of your operations. Prioritizing scalability ensures the system can grow with your business, accommodating increased production volume, expanded product lines, or additional facilities without significant disruptions.
Choosing the right tools is essential to achieving effective traceability. Cloud-based solutions, for example, enable centralized data collection and global visibility across multiple locations. Integration with Enterprise Resource Planning (ERP) systems, production equipment, and quality management platforms allows streamlined workflows and more accurate tracking. Automation further enhances traceability by reducing manual errors and ensuring data consistency.
Training employees and fostering a culture of accountability are also critical to a successful implementation. Teams should be well-versed in using the system to track, document, and analyze production processes effectively. Additionally, clear communication of the system's benefits encourages buy-in from all stakeholders, ensuring the long-term success of your traceability efforts. A well-implemented traceability system is not just a technical investment—it’s a strategic decision that drives operational excellence and builds trust throughout your value chain.
Manufacturers worldwide embrace cloud-based solutions to achieve efficiency, precision, and scalability. At 42Q, we combine decades of manufacturing expertise with cutting-edge technology to deliver smart, connected manufacturing. Our flexible, cloud-native MES platform enhances visibility, streamlines operations, and accelerates digital transformation. Discover how our solutions can empower your factory to achieve its full potential.
Key Takeaways
- Traceability ensures product quality and consistency by identifying and addressing defects early in production.
- Supply chain transparency improves accountability and helps mitigate risks such as delays or material disruptions.
- Efficient recall management reduces costs and protects brand reputation by precisely isolating issues.
- Regulatory compliance is streamlined through detailed tracking and documentation of production workflows.
- Data-driven insights enable proactive decision-making, optimizing operations and fostering innovation.
FAQ's
Manufacturing traceability ensures that every product’s lifecycle is accurately tracked and documented. This approach provides manufacturers with insights into production processes, enhances product quality, and ensures compliance with regulatory standards. Traceability also helps businesses address operational challenges, such as recalls or inefficiencies, in a more targeted and efficient manner.
Traceability creates a data flow across the supply chain, allowing stakeholders to monitor materials and products at every stage. This level of transparency helps businesses reduce delays, improve accountability, and quickly address disruptions. Additionally, supply chain visibility ensures compliance with ethical and quality standards, which builds trust among partners and customers.
Industries such as automotive, aerospace, medical devices, and food manufacturing benefit significantly from traceability due to strict compliance requirements and the need for high-quality standards. However, any manufacturing sector can leverage traceability to improve operational efficiency, enhance product quality, and reduce risk.
Technology is a critical enabler of traceability, providing tools like cloud-based platforms, automation, and real-time data collection. These technologies streamline processes, reduce human errors, and ensure the accuracy of tracking and documentation efforts. Integration with ERP systems and production equipment further enhances the effectiveness of traceability systems.
Traceability systems provide detailed documentation of materials, production conditions, and quality assurance measures. This information helps manufacturers meet regulatory standards more efficiently, simplifying audits and reducing the risk of penalties. Compliance with regulations also enhances brand reputation and builds trust with customers and stakeholders.