7 Differences Between MES vs SCADA
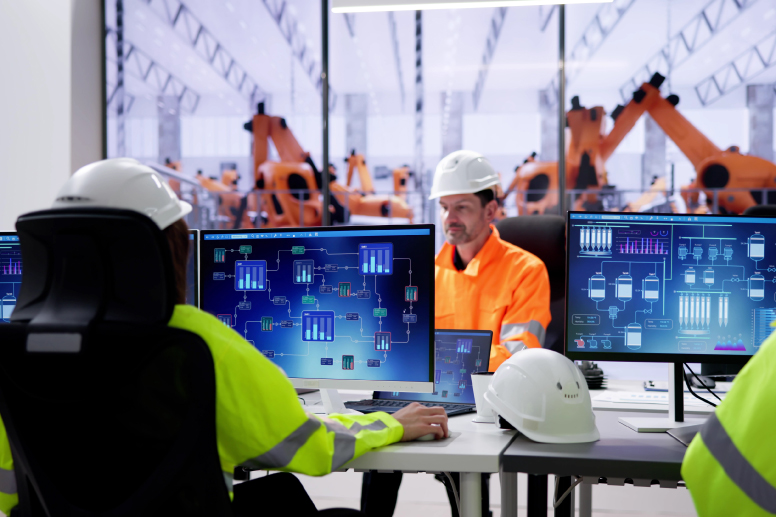
7 Differences Between MES vs SCADA
Manufacturers seeking to optimize operations and achieve sustainable growth face the challenge of selecting the right systems to manage production.
MES and SCADA, two essential manufacturing solutions, serve distinct but complementary purposes in ensuring efficiency and scalability. MES focuses on long-term optimization of the production lifecycle, while SCADA provides real-time monitoring and control of equipment. They enable manufacturers to meet modern demands with precision, agility, and strategic alignment.
What is an MES System?
"MES manages the entire production lifecycle, ensuring efficiency from planning to finished goods."
A Manufacturing Execution System (MES) is a software platform designed to monitor, control, and optimize the entire production lifecycle in manufacturing operations. Its primary function is to provide real-time insights and streamline processes from when raw materials are introduced into production to the delivery of finished products. MES bridges the gap between enterprise-level systems, such as Enterprise Resource Planning (ERP), and the operational level of the factory floor.
MES excels at resource allocation, production scheduling, quality management, and performance tracking. It transforms raw operational data into actionable insights, empowering managers to make strategic decisions that enhance productivity, reduce waste, and improve overall efficiency. MES is critical in enabling scalable and efficient manufacturing operations by offering end-to-end visibility and historical analysis.
What is a SCADA System?
A Supervisory Control and Data Acquisition (SCADA) system is designed to monitor and control industrial processes in real-time. It operates at the equipment and process level, helping operators to supervise machinery, sensors, and devices while ensuring seamless functionality. SCADA systems are widely used in manufacturing, energy, and utilities industries to oversee operations and respond to equipment or system changes instantly.
The system collects data from sensors and programmable logic controllers (PLCs) on the factory floor and displays it in an easy-to-understand interface for operators. This enables immediate responses to issues like equipment malfunctions or process deviations. SCADA focuses on maintaining consistent control and operation of processes rather than analyzing historical data or optimizing long-term performance. Its primary strength lies in real-time visibility and control of shop floor activities, making it indispensable for operational management.
7 Differences Between MES vs SCADA
The main differences between MES and SCADA lie in their scope, functionality, and the types of decisions they support. MES (Manufacturing Execution System) focuses on managing the entire production lifecycle, ensuring strategic alignment between shop floor operations and broader business objectives. SCADA (Supervisory Control and Data Acquisition), on the other hand, is designed for real-time monitoring and control of equipment, providing operators with visibility into machinery performance and process conditions.
While both systems are essential for manufacturing environments, understanding their distinct roles is critical for selecting the right tool or ensuring effective integration. Below are the seven key differences that highlight the unique strengths of MES and SCADA.
Aspect | MES | SCADA |
Scope | Manages the entire production lifecycle, including planning, resource allocation, and quality control. | Focuses on real-time monitoring and control of equipment on the shop floor. |
Data Handling | Processes and analyzes data for actionable insights, supporting long-term optimization. | Collects real-time data from sensors and PLCs for immediate adjustments. |
Primary Users | Designed for managers and decision-makers to support strategic planning and performance tracking. | Used by operators and technicians for monitoring equipment and process control. |
Function | Connects shop floor operations to enterprise systems for holistic production management. | Ensures stability and control of machinery and production processes. |
Integration | Integrates with ERP and enterprise tools for end-to-end visibility across production. | Interfaces directly with sensors, PLCs, and shop floor equipment for real-time communication. |
Decision-Making | Supports tactical and strategic decisions based on production trends and resource optimization. | Facilitates operational decisions like responding to alarms and troubleshooting. |
Analysis Type | Focuses on historical data analysis for identifying trends and driving long-term improvements. | Provides real-time monitoring and immediate insights for quick responses. |
1. Scope of Operation
The primary distinction between MES and SCADA lies in their scope. MES covers the entire production lifecycle, including resource planning, production scheduling, quality control, and performance monitoring. It is designed to bridge the gap between shop floor operations and enterprise-level systems, ensuring that production processes align with broader business objectives. MES enables manufacturers to track, manage, and optimize every step, from raw materials to finished goods delivery.
SCADA, on the other hand, operates on a narrower scope, focusing exclusively on real-time monitoring and control of equipment and processes on the shop floor. It ensures machinery operates correctly and processes remain stable, safeguarding production continuity. Unlike MES, SCADA does not extend into areas like resource allocation or product lifecycle management.
2. Data Handling
SCADA specializes in collecting real-time data from sensors, actuators, and PLCs. The data is immediately processed and used for quick adjustments to maintain equipment performance and production stability. For example, SCADA might detect a temperature fluctuation in a machine and trigger a system response to stabilize it. This level of precision is essential for maintaining consistent operations.
MES takes data a step further by analyzing and processing it to uncover actionable insights. It uses historical data trends and production metrics to inform long-term decision-making. This includes identifying bottlenecks, predicting maintenance needs, and improving overall efficiency. MES provides manufacturers with the insights needed to move from reactive problem-solving to proactive optimization.
3. Primary Users
SCADA is designed for operators and technicians who focus on real-time equipment monitoring and control. These users rely on SCADA to detect issues, respond to alarms, and maintain uninterrupted production processes. Their primary concern is keeping the shop floor running smoothly and ensuring equipment performs as expected.
MES is tailored for managers and decision-makers who need a broader perspective on production operations. It provides tools for tracking performance metrics, managing resources, and ensuring quality standards are met. MES supports high-level planning, empowering leadership to align production processes with organizational goals and strategic priorities.
4. Control vs. Management
SCADA’s primary function is control. It ensures that machinery operates within predefined parameters, monitoring equipment for deviations and making adjustments to prevent downtime or inefficiencies. SCADA excels in maintaining process stability, focusing on the immediate needs of the shop floor.
MES emphasizes management, connecting production activities with higher-level business objectives. It oversees resource allocation, workflow optimization, and performance tracking to ensure production processes are efficient and aligned with organizational strategies. MES provides a more comprehensive view of operations, helping manufacturers to optimize their processes holistically.
5. Integration Capabilities
MES integrates seamlessly with ERP systems and other enterprise tools, creating end-to-end visibility across the production lifecycle. This integration allows manufacturers to link shop floor data with financial, logistical, and strategic goals. For example, MES can provide insights into production costs, helping businesses align their operations with budgetary requirements.
SCADA interfaces directly with shop floor equipment, such as sensors, PLCs, and actuators. Its integration capabilities are focused on unlocking communication between devices to ensure smooth operations. While effective for real-time control, SCADA lacks the broader integration capabilities of MES, which extend to enterprise-level systems.
6. Decision-Making Levels
SCADA supports real-time operational decisions, such as troubleshooting equipment, responding to alarms, and making adjustments to maintain process stability. Operators rely on SCADA’s immediate feedback to keep production running without interruption.
MES enables more strategic and tactical decision-making. Managers use MES to analyze production trends, optimize resource allocation, and implement long-term improvements. MES helps manufacturers identify inefficiencies, improve productivity, and align production with business goals, supporting decisions that go beyond the shop floor.
7. Real-Time vs. Historical Analysis
"SCADA excels at real-time monitoring and control, giving operators immediate visibility into equipment performance and process conditions."
SCADA excels in real-time monitoring, providing immediate insights into equipment performance and process conditions. This enables quick responses to issues, such as machinery malfunctions or process deviations, preventing costly disruptions to production.
MES focuses on historical data analysis, compiling information over time to identify trends, inefficiencies, and areas for improvement. This data supports predictive maintenance, resource planning, and strategic optimization efforts, ensuring continuous improvement and long-term success. MES transforms raw data into actionable insights that drive sustained operational excellence.
MES and SCADA serve distinct but complementary roles in manufacturing environments. SCADA ensures real-time control and stability at the equipment level, enabling smooth operations and quick responses to process changes. MES, on the other hand, drives strategic improvements across the production lifecycle, optimizing workflows, resource allocation, and decision-making.
Understanding the difference between MES and SCADA helps manufacturers implement the right systems for their needs or integrate them effectively. Together, these tools create a powerful framework for operational excellence, scalability, and long-term success in modern manufacturing.
Benefits of MES for Scalable Manufacturing
Manufacturing Execution Systems (MES) are essential for manufacturers seeking to meet increasing production demands without compromising on quality or efficiency. These systems enable seamless coordination of processes, allowing businesses to adapt to changes, eliminate inefficiencies, and maintain consistent standards across production lines. MES supports scalability by delivering real-time insights, ensuring resource optimization, and fostering a culture of continuous improvement.
Whether addressing operational bottlenecks, improving scheduling, or integrating enterprise systems, MES provides the tools manufacturers need to achieve growth while maintaining reliability.
- Real-Time Production Visibility: MES provides real-time insights into production performance, bottlenecks, and resource use, ensuring smooth and efficient operations as production scales.
- Enhanced Quality Control: Built-in quality checkpoints ensure consistent standards and minimize defects, reducing waste and maintaining customer satisfaction.
- Optimized Resource Allocation: MES tracks and allocates materials, equipment, and labor efficiently, ensuring resources are deployed where they are needed most.
- Predictive Maintenance: Proactive equipment monitoring prevents unplanned downtime, extends machinery lifespan, and ensures uninterrupted production.
- Seamless ERP Integration: MES connects with ERP systems, aligning shop floor data with business objectives to enhance decision-making and scalability.
- Faster Decision-Making: Consolidated production data provides actionable insights, making quick adjustments to schedules, resources, and operations.
MES is a vital asset for manufacturers focused on scalability and operational efficiency. Its ability to enhance production visibility, streamline workflows, and ensure quality makes it indispensable in modern manufacturing environments. With tools like predictive maintenance, resource optimization, and ERP integration, MES allows manufacturers to scale their operations confidently while meeting market demands. Investing in MES systems creates a foundation for sustained growth and ensures businesses remain agile.
When to Use MES, SCADA, or Both?
Selecting the right system for your manufacturing operations is critical to achieving both immediate and long-term goals. MES and SCADA serve distinct purposes, with MES focusing on production management and efficiency and SCADA addressing real-time equipment monitoring and control. The decision to use one, the other, or a combination of both depends on your specific operational requirements, such as optimizing workflows, maintaining process stability, or aligning shop floor activities with enterprise objectives.
Understanding when to implement MES , SCADA, or both systems helps manufacturers unlock the full potential of their operations. Whether the goal is to improve scalability, reduce downtime, or gain better insights into production, these systems offer valuable solutions tailored to different needs.
When to Use MES
MES is an excellent choice for manufacturers focused on improving overall production efficiency, resource allocation, and long-term operational planning. It is instrumental in environments with complex production workflows, where seamless coordination across multiple processes is essential. MES enables consistent quality control, detailed performance tracking, and alignment with enterprise-level systems like ERP. Manufacturers looking to scale operations without compromising efficiency or quality benefit from the actionable insights MES provides, ensuring production remains aligned with business goals.
When to Use SCADA
SCADA is ideal for real-time equipment monitoring and process control. It is best suited for applications requiring immediate responses to operational changes or equipment performance issues. Industries that rely heavily on automation, such as energy, utilities, or high-volume manufacturing, depend on SCADA to maintain process stability and ensure operational consistency. SCADA systems excel at providing real-time data from sensors and machinery, enabling operators to make quick adjustments to avoid downtime or disruptions.
When to Use Both
Using MES and SCADA together delivers the most comprehensive solution for manufacturers looking to integrate real-time control with strategic production management. SCADA ensures smooth day-to-day operations by monitoring and controlling equipment, while MES provides insights into long-term performance, resource planning, and quality management. Together, these systems enable end-to-end visibility, supporting manufacturers in achieving innovative factory initiatives and leveraging advanced analytics for continued improvement. Integration of MES and SCADA is particularly beneficial for businesses that align shop floor activities with enterprise-wide goals, ensuring short-term operational stability and long-term efficiency.
MES and SCADA are complementary systems that cater to different manufacturing needs but offer the greatest value when used together. MES drives production efficiency and strategic alignment, while SCADA ensures equipment stability and immediate responsiveness. Implementing these systems in tandem enables manufacturers to achieve operational resilience, and meet production demands. Choosing the right approach allows businesses to address both present challenges and future growth opportunities effectively.
Manufacturers worldwide are embracing cloud-based solutions to achieve efficiency, precision, and scalability. At 42Q, we combine decades of manufacturing expertise with cutting-edge technology to deliver smart connected manufacturing. Our flexible, cloud-native MES platform enhances visibility, streamlines operations, and accelerates digital transformation. Discover how our solutions can empower your factory to achieve its full potential.
Key Takeaways
- MES optimizes the entire production lifecycle, enabling manufacturers to enhance efficiency, maintain quality, and scale operations seamlessly.
- SCADA provides real-time monitoring and control, ensuring equipment and processes run smoothly without interruptions.
- MES and SCADA serve different purposes but complement each other when integrated, offering end-to-end visibility and operational efficiency.
- Integrating MES with ERP systems provides strategic insights, helping manufacturers align production with business goals.
- Predictive maintenance, traceability, and brilliant factory support make MES critical for manufacturers pursuing scalable and sustainable growth.
FAQs
MES focuses on managing the entire production lifecycle, optimizing processes, and aligning operations with business goals. SCADA is designed for real-time monitoring and control of equipment, ensuring stability at the shop floor level. Both systems play distinct roles but can complement each other when integrated.
MES and SCADA can be integrated to provide end-to-end visibility across production and operations. SCADA manages real-time control, while MES handles strategic optimization and resource planning, making their combined use ideal for scaling and achieving long-term efficiency.
MES is particularly beneficial for large-scale manufacturers because it streamlines production processes, enhances resource management, and provides actionable insights. Its ability to handle complex workflows and integrate with ERP systems makes it a powerful tool for scaling operations.
SCADA improves operational efficiency by providing real-time monitoring and control of equipment. It allows operators to respond immediately to process changes or equipment issues, minimizing downtime and ensuring consistent performance on the shop floor.
Industries like automotive, aerospace, medical devices, and energy benefit significantly from MES and SCADA. MES provides robust traceability, quality control, and resource optimization, while SCADA supports real-time process control and automation, making both systems critical for modern manufacturing.