7 Features of MES in Industrial Automation
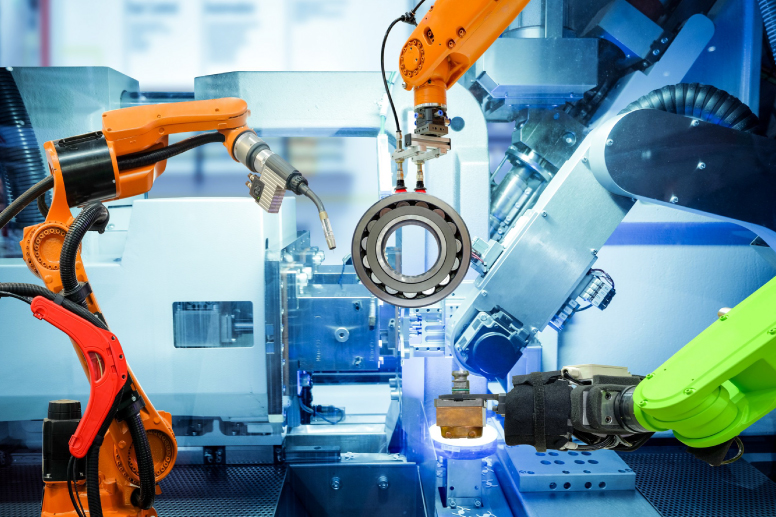
7 Features of MES in Industrial Automation
Manufacturers require efficient, data-driven systems to maintain productivity and quality in industrial automation.
Manufacturing execution systems (MES) bridge the gap between enterprise planning and shop floor control, providing real-time tracking, workflow automation, and compliance management. These systems integrate with industrial automation to streamline production processes, optimize resource allocation, and enhance product traceability.
As production increases, MES helps manufacturers improve efficiency while reducing errors and waste. These systems centralize production data, providing the visibility needed to make informed decisions. With advanced tracking, predictive maintenance, and seamless system integration, MES supports manufacturers in maintaining consistent operations while adapting to new production requirements.
Understanding MES in Industrial Automation
Manufacturing execution systems (MES) are essential in industrial automation, as they connect production processes, track operations, and ensure data-driven decision-making. These systems bridge the gap between enterprise resource planning (ERP) and shop floor control, delivering real-time insights that enhance efficiency, quality, and compliance. As industrial automation expands, MES provides a scalable solution for improving productivity while maintaining strict operational standards.
MES solutions collect, analyze, and interpret production data to optimize manufacturing workflows. By offering real-time visibility into work-in-progress (WIP), machine performance, and quality assurance, MES empowers manufacturers to reduce downtime, improve throughput, and maintain consistency across operations. With increasing for traceability and regulatory adherence, MES also supports industries that require stringent documentation and compliance measures.
Benefits of MES in Industrial Automation
Manufacturers use MES to improve production efficiency, reduce costs, and maintain consistency in manufacturing processes. These systems connect production operations, providing real-time insights that support better resource management, quality control, and compliance tracking. MES also integrates with industrial automation technologies to streamline operations and minimize manual intervention, improving accuracy and reducing delays.
The benefits of MES extend across multiple areas, from optimizing equipment utilization to enhancing supply chain visibility. These advantages allow manufacturers to maintain high output levels while ensuring product reliability and regulatory adherence. MES capabilities support automation, data-driven improvements, and overall operational efficiency.
- Real-time production monitoring: MES provides continuous visibility into production operations, tracking work-in-progress (WIP), material consumption, and machine performance. Operators receive instant updates, allowing them to identify and address bottlenecks before they disrupt workflows. Real-time tracking reduces unplanned downtime, improves response times, and ensures that production schedules remain on track.
- Optimized resource utilization: Manufacturing operations depend on efficiently using materials, labor, and equipment. MES analyzes production data to identify inefficiencies and optimize resource allocation. Automated scheduling ensures that machinery operates at peak efficiency while reducing idle time. Workforce management tools help balance labor distribution, preventing production slowdowns caused by underutilized or overburdened teams.
- Improved product quality: MES enforces quality control processes, tracking defects and ensuring that inspections are performed at the correct intervals. Automated alerts notify operators when quality deviations occur, allowing immediate corrective action. Historical quality data provides insights into recurring issues, making refining processes and maintaining product consistency easier. Manufacturers in regulated industries benefit from traceability features that document compliance with industry standards.
- Streamlined compliance tracking: Manufacturing industries must adhere to strict regulatory requirements, requiring accurate documentation of production activities. MES automates compliance tracking by recording process data, material genealogy, and quality inspection results. These records support audit readiness and reduce the time spent on manual reporting. Manufacturers in aerospace, medical devices, and automotive sectors benefit from MES features that simplify regulatory adherence.
- Reduced production costs: MES helps manufacturers minimize waste, optimize inventory, and improve energy efficiency, leading to lower operating costs. Automated production tracking reduces material overuse and prevents unnecessary downtime. Data-driven process optimization further reduces expenses by identifying areas where production time and labor can be minimized without sacrificing output quality.
- Seamless data integration: MES connects with enterprise resource planning (ERP) systems, industrial IoT (IIoT) devices, and production machinery to centralize data collection and reporting. This integration provides a comprehensive view of manufacturing operations, ensuring managers can access accurate, real-time insights. Improved data flow between systems enhances production planning, inventory control, and supply chain management.
- Enhanced supply chain visibility: MES supports material tracking, supplier coordination, and inventory management, preventing disruptions caused by stock shortages or misaligned production schedules. Automated updates provide real-time inventory adjustments, reducing the risk of overproduction or excess storage costs. Improved supply chain coordination ensures manufacturers meet production targets while reducing logistical challenges.
Manufacturers rely on MES to improve production visibility, reduce inefficiencies, and maintain consistent quality. These benefits help production teams meet output targets while minimizing costs and ensuring compliance with industry regulations. As industrial automation advances, MES continues to be an essential tool for optimizing manufacturing operations.
7 Features of MES in Industrial Automation
Industrial automation relies on precise coordination between machines, data systems, and human operators. Manufacturing execution systems (MES) provide the digital infrastructure to synchronize production processes, track real-time performance, and ensure quality control at every stage. These systems offer an advanced level of visibility, helping manufacturers optimize efficiency, reduce errors, and improve resource management.
MES features support critical production functions, including real-time monitoring, predictive maintenance, and compliance tracking. As manufacturers implement automation technologies, these capabilities allow them to maintain high output levels without sacrificing product quality or regulatory adherence. MES features are fundamental to improving efficiency, consistency, and data-driven manufacturing decisions.
1. Real-time Data Tracking
Production efficiency depends on continuously monitoring materials, equipment, and process execution. MES collects and processes real-time data from production lines, providing instant insights into work-in-progress (WIP), inventory levels, and machine performance. This data allows manufacturers to make informed adjustments, preventing bottlenecks and reducing downtime.
Automated data collection eliminates manual tracking errors and ensures operators receive accurate production status reports. With real-time visibility, manufacturers can monitor throughput, detect potential disruptions, and identify opportunities for improvement. These insights allow production teams to fine-tune processes, optimize scheduling, and maintain consistent operational output.
Beyond performance tracking, MES also analyzes historical data, helping manufacturers identify patterns that impact productivity. Trends in cycle times, equipment utilization, and defect rates become more straightforward to interpret, and production teams to refine operations and reduce inefficiencies.
2. Enhanced Production Efficiency
Manufacturers depend on MES to streamline workflows and improve resource utilization. These systems automate production scheduling, work order management, and process enforcement to minimize delays and maintain consistency. Automated scheduling ensures that workstations receive the correct instructions at the right time, reducing human errors and improving throughput.
Resource allocation becomes more effective with MES, providing real-time insights into equipment availability, workforce productivity, and material consumption. This data-driven approach minimizes idle time and prevents supply chain inefficiencies that could disrupt production. MES also supports automated adjustments to production schedules based on popular fluctuations, ensuring manufacturers maintain optimal output levels without excessive inventory buildup.
Process standardization further improves efficiency. MES enforces predefined workflows, ensuring that operators follow the correct steps and adhere to established quality control measures. Consistency in production methods reduces defects and rework, improving overall efficiency while maintaining product reliability.
3. Quality Control and Assurance
Maintaining high product quality is a priority in industrial automation. MES integrates with quality management systems to track defect rates, enforce inspection protocols, and standardize compliance measures. Automated data collection helps detect quality deviations early, preventing defective products from progressing through production.
Automated alerts notify operators when production parameters fall outside acceptable ranges. Early detection allows manufacturers to take corrective action immediately, reducing waste and minimizing costly rework. Historical quality data also provides insights into recurring issues, helping manufacturers refine processes to prevent future defects.
Regulated industries benefit from MES-driven quality control, as these systems maintain electronic batch records, track material genealogy, and ensure that manufacturing processes align with industry standards. Traceability features allow manufacturers to provide detailed compliance reports, reducing the complexity of audits and regulatory reviews.
4. Supply Chain Management
Production stability depends on effective supplier coordination, inventory management systems, and manufacturing operations. MES strengthens supply chain efficiency by providing real-time updates on material consumption, supplier performance, and inventory levels. Automated tracking ensures manufacturers maintain optimal stock levels while avoiding shortages and overproduction.
Inventory synchronization is an essential function of MES, preventing production delays caused by missing materials. These systems automatically adjust stock levels based on usage rates, ensuring critical components are available when needed. Supplier coordination also improves, as MES provides insights into lead times, delivery schedules, and vendor performance, allowing manufacturers to make strategic purchasing decisions.
Data-driven supply chain management reduces excess costs and improves order fulfillment accuracy. With MES, manufacturers can align production schedules with increase in forecasts, minimizing waste and improving efficiency. These capabilities help maintain seamless operations while reducing logistical challenges.
5. Integration with Industrial IoT
Manufacturers are integrating industrial IoT (IIoT) technologies to improve automation, monitoring, and data collection. MES connects with IIoT-enabled devices, allowing production systems to gather performance data from smart sensors, robotics, and connected machinery. This integration improves real-time monitoring, predictive analytics, and automated solutions.
MES analyzes machine-generated data to provide insights into operational efficiency. Manufacturers can track energy consumption, equipment performance, and conditions, ensuring that production parameters remain within optimal ranges. These insights help detect inefficiencies and make data-driven adjustments to improve productivity.
Automated communication between MES and IIoT devices enhances process control. Innovative machinery can adjust production variables in response to MES instructions, improving precision and reducing variability. This level of automation ensures that production remains consistent while minimizing human intervention.
6. Predictive Maintenance
Equipment failures can cause costly production disruptions. MES provides predictive maintenance capabilities by analyzing machine performance data, detecting early warning signs of mechanical issues, and automating maintenance scheduling before breakdowns occur.
Continuous equipment monitoring allows MES to track temperature fluctuations, vibration levels, and operational deviations that indicate potential failures. Automated alerts notify maintenance teams when predefined thresholds are exceeded, allowing them to perform preventive maintenance before the issue escalates.
Optimizing maintenance schedules improves asset longevity and reduces unplanned downtime. Manufacturers can extend the lifespan of machinery, lower repair costs, and prevent unexpected production delays. Predictive maintenance reduces reliance on reactive repair strategies, improving overall equipment efficiency.
7. Regulatory Compliance
Manufacturers operating in regulated industries must maintain detailed production records to meet industry standards. MES simplifies compliance by automating documentation, tracking material usage, and enforcing process controls that align with regulatory requirements.
Traceability features provide a clear record of product genealogy, allowing manufacturers to trace components and production steps in case of audits or recalls. MES also generates electronic batch records that streamline regulatory reporting, reducing manual documentation efforts.
Industries such as medical devices, aerospace, and automotive manufacturing benefit from MES compliance tools, as these systems provide the documentation needed to verify adherence to quality and safety standards. Automated compliance tracking reduces the risk of nonconformities and improves audit readiness.
Manufacturing execution systems are essential in industrial automation, offering real-time tracking, efficiency improvements, and compliance support. These systems provide the digital infrastructure manufacturers need to manage complex production workflows while maintaining high product quality.
Manufacturers can optimize production processes and reduce operational risks by integrating MES with IIoT, predictive maintenance, and supply chain management. The ability to monitor and control every stage of manufacturing ensures consistent output, lower costs, and improved regulatory compliance. MES continues to be a vital tool for industrial automation, supporting manufacturers in achieving efficiency and reliability across production operations.
Implementing MES in Industrial Automation
Manufacturers rely on MES to improve efficiency, standardize workflows, and enhance production visibility. Successful implementation requires strategic planning, alignment with existing infrastructure, and seamless integration with enterprise systems. MES solutions must support production goals while minimizing disruptions during deployment. Implementation begins with assessing production workflows, identifying inefficiencies, and defining key performance indicators (KPIs). Understanding current operational challenges helps manufacturers configure MES to address specific needs, such as reducing downtime, improving quality control, or enhancing supply chain coordination. Establishing clear objectives ensures that MES delivers measurable improvements across production operations.
System integration plays a vital role in MES deployment. MES must connect with ERP, industrial IoT (IIoT) devices, and manufacturing equipment to provide accurate, real-time data. Compatibility with existing hardware and software solutions ensures smooth data exchange, preventing information silos and delays in production monitoring. MES also requires configuration to align with regulatory requirements, providing accurate documentation and traceability in compliance-driven industries.
Training and adoption strategies determine the success of MES implementation. Operators, engineers, and managers must understand how to use MES tools effectively. User-friendly interfaces, automated reporting, and role-based access help teams transition to digital workflows without disruptions. Ongoing support and training ensures employees maximize MES capabilities, improving production efficiency and operational control.
Continuous optimization allows manufacturers to refine MES performance over time. Real-time monitoring and historical data analysis provide insights into production trends, equipment performance, and process bottlenecks. Manufacturers can adjust MES configurations to improve efficiency, reduce costs, and enhance productivity. As industrial automation advances, MES is a scalable solution that adapts to new manufacturing needs.
Manufacturers worldwide embrace cloud-based solutions to achieve efficiency, precision, and scalability. At 42Q, we combine decades of manufacturing expertise with cutting-edge technology to deliver smart, connected manufacturing. Our flexible, cloud-native MES platform enhances visibility, streamlines operations, and accelerates digital transformation. Discover how our solutions can empower your factory to achieve its full potential.
Key Takeaways
- Manufacturing execution systems (MES) provide real-time visibility into production processes, reducing downtime and optimizing efficiency.
- MES enhances quality control and compliance tracking by automating inspections, documentation, and traceability reporting for regulated industries.
- Resource optimization features in MES reduce costs by improving inventory management, automating scheduling, and minimizing material waste.
- Integrating industrial IoT (IIoT) devices strengthens automation, continuously monitoring machine performance and predictive maintenance alerts.
- MES improves supply chain coordination by synchronizing material tracking, supplier performance, and inventory levels, reducing disruptions in production.
FAQs
MES improves industrial automation by monitoring real-time production, reducing downtime, and optimizing resource utilization. These systems automate data collection, streamline workflows, and support predictive maintenance, ensuring smooth manufacturing operations. MES also enhances compliance tracking and quality control, reducing errors and improving efficiency.
MES is widely used in industries such as automotive, medical devices, aerospace, semiconductor manufacturing, and consumer electronics. These industries require strict process control, compliance tracking, and efficiency improvements. MES helps manufacturers maintain traceability, manage production schedules, and enhance product quality.
MES focuses on shop floor operations, providing real-time tracking and automation, while ERP (Enterprise Resource Planning) handles business-wide functions such as finance, procurement, and logistics. MES integrates with ERP to ensure seamless data exchange between production and business processes, improving overall operational visibility.
MES records detailed production data, including material usage, work instructions, and inspection results, simplifying compliance tracking. These systems generate audit-ready reports, automate traceability, and ensure adherence to industry standards in regulated sectors such as aerospace and medical device manufacturing.
MES integrates with industrial IoT (IIoT) devices to enhance automation and real-time monitoring. Connected sensors and smart machinery feed data into MES, providing insights into equipment performance, energy consumption, and predictive maintenance needs. This integration improves process control and reduces manual intervention.