9 Best Practices for Implementing MES in the Manufacturing Industry
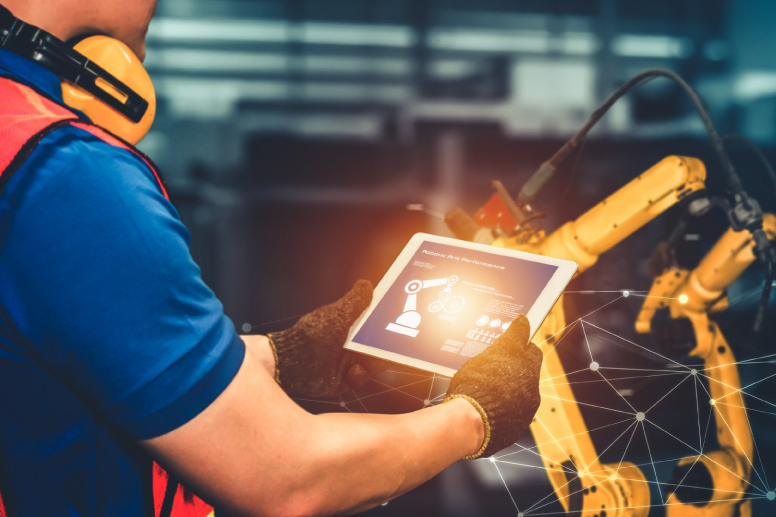
9 Best Practices for Implementing MES in the Manufacturing Industry
Manufacturers are optimizing production efficiency, improving quality control, and increasing operational visibility with Manufacturing Execution Systems (MES).
These systems provide real-time data tracking, automation, and process standardization, helping manufacturers reduce downtime, minimize waste, and maintain compliance with industry regulations. MES bridges the gap between enterprise resource planning (ERP) systems and factory-floor operations, ensuring seamless data exchange and enhanced production control.
Successful MES implementation requires a structured approach, strategic deployment, and continuous optimization to deliver measurable benefits. Companies that leverage MES effectively gain deeper insights into production performance, streamline workflows, and achieve consistent product quality across manufacturing sites.
Understanding MES in the Manufacturing Industry
Manufacturing Execution Systems (MES) play an essential role in modern production settings by providing real-time monitoring, control, and optimization of manufacturing operations. These systems bridge the gap between enterprise resource planning (ERP) and plant-floor automation, ensuring seamless data flow and improved operational efficiency.
MES manufacturing solutions track every aspect of production, from order release to final product delivery. They collect and analyze data on production cycles, machine performance, quality control, and compliance requirements. MES helps manufacturers improve process efficiency, reduce downtime, and maintain product quality by providing accurate, real-time insights. Implementing MES in manufacturing industry settings is crucial for companies seeking to enhance visibility, enforce process standardization, and increase overall productivity.
Benefits of MES in the Manufacturing Industry
"MES ensures real-time tracking of work-in-progress, machine status, and process performance across all production lines, allowing manufacturers to monitor efficiency, identify bottlenecks, and make informed decisions."
Manufacturing Execution Systems (MES) provide measurable improvements in efficiency, quality, and cost reduction. As manufacturing operations become more complex, MES ensures real-time visibility, standardization, and traceability across production processes. The ability to monitor, analyze, and optimize workflows results in streamlined operations, improved compliance, and enhanced production control. These benefits allow manufacturers to maintain consistent quality while reducing waste, downtime, and operational inefficiencies.
- Improved Production Visibility: MES provides real-time tracking of work-in-progress, machine status, and process performance across all production lines. Instant access to accurate production data allows supervisors and plant managers to monitor efficiency, identify bottlenecks, and make informed decisions to keep operations running smoothly. Enhanced visibility ensures that production targets are met, optimized resource utilization, and minimized unplanned disruptions.
- Enhanced Quality Control: Standardized processes, automated inspections, and digital traceability improve product quality and reduce defects. MES enforces quality checks at critical points in the production cycle, ensuring that defective products are identified before reaching later stages. Automated data collection helps detect patterns that may indicate potential quality issues, allowing manufacturers to implement corrective actions before defects escalate into costly recalls.
- Reduced Downtime and Equipment Failures: MES tracks machine performance in real-time, detecting anomalies that indicate potential equipment failures. Predictive maintenance alerts allow maintenance teams to address issues before they cause unplanned downtime. This proactive approach reduces repair costs, extends equipment lifespan, and improves overall equipment effectiveness (OEE).
- Better Regulatory Compliance: Meeting industry regulations requires meticulous record-keeping, process standardization, and strict adherence to quality standards. MES assists manufacturers with compliance by maintaining digital records of production activities, enforcing standard operating procedures (SOPs), and providing audit-ready documentation. Automated compliance tracking reduces the time and effort required for regulatory reporting while minimizing the risk of non-compliance penalties.
- Optimized Resource Utilization: MES ensures that labor, materials, and machine capacity are used efficiently by providing real-time data on production performance. Intelligent scheduling prevents resource bottlenecks, optimizes shift planning, and reduces material waste. Automated workflows and digital work instructions help operators follow best practices, reducing errors and maximizing productivity.
- Faster Time to Market: Delays in production processes can impact supply chain efficiency and customer satisfaction. MES accelerates production cycles by automating workflows, reducing manual reporting delays, and providing real-time process adjustments. Shorter cycle times ensure that products reach the market faster while maintaining consistent quality and compliance with industry standards.
- Lower Operational Costs: Increased automation and process optimization reduce waste, rework, and labor inefficiencies. MES helps manufacturers cut costs by eliminating redundant manual tasks, improving material traceability, and minimizing errors that result in defective products. Lower operational costs contribute to higher profit margins and improved overall business performance.
- Improved Traceability and Lot Tracking: Full traceability of raw materials, components, and finished goods ensures that manufacturers can track every aspect of production. MES captures detailed records of batch numbers, operator activities, and machine performance, providing a comprehensive history of each product. This level of traceability is essential for industries with strict compliance requirements, such as medical devices, automotive, and aerospace manufacturing.
- Better Data-Driven Decision Making: MES aggregates data from multiple sources, manufacturers to make informed decisions based on real-time insights. Advanced reporting and analytics tools clearly show production trends, efficiency metrics, and quality performance. This data-driven approach allows businesses to continuously optimize operations and maintain a dynamic advantage in the market.
MES in manufacturing industry settings provides measurable benefits that enhance operational efficiency, improve quality control, and optimize resource allocation. Manufacturers that implement MES effectively gain the ability to monitor and adjust processes in real-time, ensuring that production goals are met while reducing costs and maintaining compliance with industry regulations.
9 Best Practices for Implementing MES in the Manufacturing Industry
Implementing an MES manufacturing system requires careful planning, structured execution, and continuous refinement. A well-executed MES deployment maximizes system benefits, enhances production efficiency, and improves overall operational control. Manufacturers may face integration challenges, data inconsistencies, and user adoption issues without a clear strategy. These best practices ensure that MES implementation aligns with business objectives while minimizing disruptions to existing workflows.
1. Define Clear Objectives and Key Performance Indicators (KPIs)
A structured MES implementation begins with well-defined goals and measurable success criteria. Objectives should align with operational priorities such as improving production visibility, reducing cycle times, or enhancing quality control. Key performance indicators (KPIs) provide quantifiable benchmarks to track system effectiveness over time.
Identifying KPIs such as overall equipment effectiveness (OEE), defect rates, and production yield ensures that MES delivers tangible improvements. Regular performance monitoring helps refine implementation strategies, ensuring the system meets business needs.
2. Conduct a Thorough Process Assessment
Understanding current production workflows is essential before integrating MES into manufacturing operations. A comprehensive assessment identifies inefficiencies, bottlenecks, and areas for automation. Without a clear baseline, manufacturers risk configuring MES in a way that fails to address actual process challenges.
Engaging operators, engineers, and IT teams during the assessment phase ensures that MES implementation reflects real production needs. Mapping out workflows, documenting manual tasks, and analyzing machine utilization data provide valuable insights into system configuration requirements.
3. Ensure Seamless Integration with Existing Systems
MES must work harmoniously with ERP software, supervisory control and data acquisition (SCADA) systems, and industrial automation platforms. A well-planned integration strategy ensures that MES is part of a connected digital infrastructure rather than an isolated system.
Interoperability considerations include data exchange formats, system compatibility, and API availability. Addressing integration challenges early prevents data silos, ensuring that MES provides a unified view of production operations.
4. Standardize Data Collection and Reporting
Inconsistent data collection leads to inaccurate reporting, limiting MES effectiveness. Standardizing data capture protocols ensures that production metrics remain reliable across all manufacturing sites. Consistency in data formats, measurement units, and reporting structures eliminates discrepancies that could impact process analysis.
Standardized reporting enhances traceability, manufacturers to compare performance across facilities and identify trends. Clear data governance policies improve regulatory compliance by ensuring all production records meet industry documentation standards.
5. Prioritize User Training and Adoption
Operator engagement is critical to MES success. Employees may struggle to use the system efficiently without proper training, leading to underutilized features and inconsistent data entry. Training programs must address system navigation, data input procedures, troubleshooting techniques, and best practices for interpreting MES insights.
Hands-on workshops, digital training modules, and ongoing support resources ensure that employees gain confidence in using MES. Encouraging operators to provide feedback during training helps identify usability improvements, further increasing system adoption rates.
6. Implement Phased Deployment
Deploying MES in stages minimizes operational disruptions and allows teams to address issues before full-scale implementation. A phased rollout strategy ensures that manufacturers can test MES functionality, refine configurations, and train employees before extending the system to additional production lines or facilities.
Initial deployment should focus on high-priority areas with the greatest potential for efficiency gains. Lessons learned during early phases inform broader implementation strategies, reducing risks associated with large-scale adoption.
7. Establish a Strong Support and Maintenance Plan
MES requires continuous monitoring, updates, and technical support to remain effective. A proactive maintenance strategy ensures that the system stays aligned with progressive production requirements and technology advancements. Without proper maintenance, system performance may degrade over time, impacting manufacturing efficiency.
Support plans should include regular software updates, performance monitoring, and structured troubleshooting protocols. Dedicated IT and MES support teams help resolve technical issues quickly, preventing disruptions to production operations.
8. Leverage Data Analytics for Continuous Improvement
MES generates vast amounts of production data that can drive ongoing process optimization. Advanced analytics tools identify trends, pinpoint inefficiencies, and support predictive maintenance strategies. Manufacturers that actively analyze MES data gain deeper insights into production performance them to refine workflows and reduce waste.
Data-driven evaluation enhances productivity, ensuring that MES delivers long-term value. Customizable dashboards and real-time reporting features help supervisors monitor key metrics and implement targeted process improvements.
9. Ensure Compliance with Industry Regulations
Strict regulatory requirements in medical devices, automotive, and aerospace industries necessitate precise process controls. MES assists manufacturers in maintaining compliance by enforcing standard operating procedures, capturing electronic records, and generating audit-ready documentation.
Built-in traceability features track materials, monitor process deviations, and provide detailed production logs. Digital compliance management reduces the time and effort required for regulatory audits, improving quality assurance.
A structured MES implementation strategy supports long-term operational efficiency, enhances process visibility, and improves production control. These best practices ensure manufacturers maximize MES benefits while mitigating deployment risks, resulting in a more efficient and data-driven production setting.
Measuring the Efficiency of MES Manufacturing
Assessing the impact of MES in manufacturing industry settings requires a structured approach using measurable performance indicators. Manufacturers may struggle to identify process inefficiencies, evaluate system effectiveness, or justify MES investments without accurate data. Key metrics provide valuable insights into production performance, helping businesses refine workflows, improve quality, and reduce costs.
- Overall Equipment Effectiveness (OEE): This metric evaluates equipment utilization by measuring three key factors—availability, performance, and quality. Higher OEE scores indicate fewer machine stoppages, optimized cycle times, and lower defect rates. MES enhances OEE by automating downtime tracking, optimizing scheduling, and ensuring consistent process execution.
- Production Yield: The percentage of defect-free units compared to total production provides insight into quality control improvements. A higher yield indicates better process consistency, reduced scrap, and fewer rework instances. MES manufacturing solutions assist in maintaining high yield rates by enforcing standardized work instructions, capturing process deviations, and identifying root causes of defects.
- Cycle Time Reduction: The time required to complete a manufacturing process directly impacts production efficiency. MES reduces cycle times by automating data collection, eliminating manual reporting delays, and providing real-time insights for process adjustments. Faster cycle times translate to higher throughput and reduced lead times for customer deliveries.
- Downtime Tracking: Equipment downtime negatively impacts production schedules and operational costs. MES allows real-time monitoring of downtime events, classifying them by cause, duration, and frequency. This data helps maintenance teams address recurring issues, implement predictive maintenance strategies, and reduce unplanned disruptions.
- Work-in-Progress (WIP) Visibility: Tracking WIP inventory at each production stage ensures materials flow efficiently without bottlenecks. MES provides real-time WIP tracking, reducing delays caused by material shortages, unexpected machine stoppages, or inefficient workflows. Greater visibility into WIP improves production planning and resource allocation.
- Labor Productivity: Measuring workforce efficiency helps manufacturers identify training needs, optimize labor allocation, and improve productivity. MES captures operator performance data, ensuring tasks are completed on time and by standard procedures. Automated workflows and digital work instructions reduce reliance on manual processes, increasing operational consistency.
- Compliance and Traceability Metrics: Industries such as medical devices, automotive, and aerospace require strict adherence to regulatory standards. MES manufacturing systems maintain digital records of production activities, enforce process controls, and generate audit-ready documentation. Improved traceability ensures manufacturers can track every component and process step, reducing compliance risks and audit preparation time.
- Scrap and Rework Rates: Defective or discarded materials represent wasted resources and higher production costs. MES minimizes scrap and rework by identifying defects early, enforcing quality control measures, and capturing real-time process deviations. Lower scrap rates lead to cost savings, improved sustainability, and enhanced product consistency.
- Energy Consumption Efficiency: Energy usage directly impacts production costs and sustainability goals. MES tracks energy consumption at the equipment level, identifying inefficiencies and opportunities for cost reduction. Insights from MES data help manufacturers optimize machine settings, schedule production during lower-cost energy periods, and reduce overall resource consumption.
Consistently tracking MES performance through these key metrics helps manufacturers optimize production efficiency, enhance quality, and improve cost-effectiveness. A data-driven approach allows continuous process improvements, ensuring that MES delivers measurable benefits across all manufacturing stages.
Looking Ahead for MES in Manufacturing
Manufacturers are adopting MES faster to improve operational visibility, streamline production, and maintain quality standards. Increased automation, artificial intelligence, and data-driven decision support systems are shaping the future of MES manufacturing solutions, making them more intelligent and adaptable. Cloud-based MES is gaining traction due to its scalability, real-time data accessibility, and lower upfront costs than on-premise systems.
Predictive analytics and machine learning capabilities will continue to enhance MES functionality by detecting patterns in production data, predicting equipment failures, and optimizing workflows. More excellent connectivity between MES, ERP, and IoT-allowed devices will improve manufacturing efficiency by ensuring seamless data exchange and real-time monitoring. As compliance regulations become stricter across industries, MES will remain a key tool in maintaining traceability, enforcing standard operating procedures, and reducing audit preparation time.
Manufacturers investing in MES will benefit from higher production efficiency, more substantial quality control, and improved regulating capabilities. Future advancements in MES technology will provide even greater automation, data accuracy, and process optimization, ensuring that manufacturing operations remain efficient and resilient in a growingly complex production setting.
Manufacturers worldwide are adopting cloud-based solutions to achieve efficiency, precision, and scalability. At 42Q, we combine decades of manufacturing expertise with cutting-edge technology to deliver innovative, connected manufacturing. Our flexible, cloud-native MES platform enhances visibility, streamlines operations, and accelerates digital factory transformation. Discover how our solutions can empower your factory to achieve its full potential.
Key Takeaways
- MES enhances production visibility and efficiency. Real-time tracking and automated workflows provide manufacturers with accurate data for optimizing operations and minimizing waste.
- Data standardization ensures consistency and accuracy. Uniform data collection and reporting improve process monitoring, governance, and regulatory compliance.
- MES reduces downtime and maintenance costs. Predictive maintenance and automated alerts prevent equipment failures, improving overall productivity.
- Seamless integration with existing systems is critical. Successful MES deployment requires compatibility with ERP, SCADA, and industrial automation platforms.
- User adoption and training determine MES success. Comprehensive training programs and phased deployment strategies ensure smooth system implementation and long-term efficiency gains.
FAQs
MES manufacturing refers to the use of a Manufacturing Execution System to monitor, control, and optimize production processes in real time. It improves efficiency by automating data collection, reducing manual tasks, and ensuring standardized workflows. This reduces cycle times, lower defect rates, and higher overall equipment effectiveness (OEE).
MES tracks machine performance, detects anomalies, and provides predictive maintenance alerts to prevent unexpected breakdowns. It identifies recurring issues that cause production delays and allows maintenance teams to schedule repairs proactively. This minimizes unplanned stoppages and extends equipment lifespan.
Industries with strict quality control and regulatory requirements benefit the most, including medical device manufacturing, automotive, aerospace, semiconductors, and consumer electronics. MES ensures traceability, process standardization, and compliance with industry regulations.
Common challenges include system integration with existing ERP and SCADA systems, standardizing data collection methods, and ensuring user adoption. A phased deployment approach, comprehensive training, and ongoing system support help address these challenges effectively.
MES maintains digital records of production activities, enforces standard operating procedures (SOPs), and provides audit-ready documentation. This ensures full traceability of raw materials, batch tracking, and adherence to industry regulations, reducing compliance risks and audit preparation time.