How MES Supports Medical Device Manufacturing
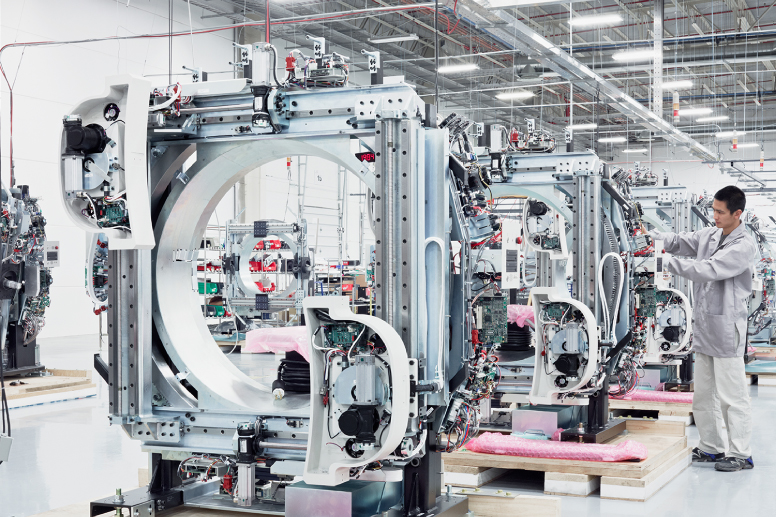
How MES Supports Medical Device Manufacturing
Manufacturing medical devices require absolute precision, strict compliance, and streamlined production processes.
Every stage, from raw material sourcing to final product assembly, must meet regulatory standards while maintaining efficiency and traceability. Errors in production can lead to costly recalls, regulatory violations, and compromised patient safety. As manufacturers work to balance quality control, cost management, and operational efficiency, technology plays a critical role in modernizing workflows.
A manufacturing execution system (MES) improves medical device manufacturing by optimizing production control, ensuring compliance, and enhancing traceability. With real-time monitoring, automated workflows, and seamless system integration, MES helps manufacturers meet the industry's highest standards while reducing inefficiencies. As regulatory requirements grow more complex and supply chains face ongoing disruptions, manufacturers must adopt digital solutions to maintain accuracy and productivity.
What is Medical Device Manufacturing?
Medical device manufacturing is designing, producing, testing, and distributing medical equipment used to diagnose, treat, monitor, and prevent diseases. This industry covers various products, including surgical instruments, imaging systems, implants, diagnostic devices, and wearable health monitors. Each product must meet stringent regulatory safety, accuracy, and reliability requirements.
Manufacturers operate under strict quality control systems due to the high-stakes nature of healthcare. Regulations such as those set by the U.S. Food and Drug Administration (FDA) and international standards like ISO 13485 outline precise criteria for design validation, process control, and documentation. As a result, companies in this sector require robust manufacturing execution systems (MES) to maintain efficiency, traceability, and compliance while meeting production requests.
Role of MES in Medical Device Manufacturing
A manufacturing execution system (MES) is essential in medical device manufacturing as it improves production efficiency, enforces process controls, and ensures product traceability. This technology bridges the gap between enterprise resource planning (ERP) systems and shop floor operations, providing real-time data on production workflows, equipment status, and quality metrics.
Regulatory compliance remains a significant challenge in medical manufacturing, and MES helps streamline data collection, electronic batch records, and audit trails. Automated workflows reduce the risk of human error while supporting strict documentation requirements. MES also integrates with quality management systems to track deviations, defects, and corrective actions, improving overall product consistency.
Advanced MES solutions support manufacturing optimization by monitoring key performance indicators (KPIs) such as cycle times, machine utilization, and yield rates. Manufacturers gain insights into production bottlenecks and inefficiencies, allowing them to refine processes and improve throughput while maintaining compliance with industry standards.
Benefits of MES in Medical Device Manufacturing
"MES enhances regulatory compliance, automates data collection, and improves production efficiency. It reduces human errors, enforces standardized workflows, and integrates with enterprise systems for seamless data sharing."
Medical device manufacturing requires high precision, compliance, and efficiency. Every step of the production process must meet stringent regulatory requirements while maintaining cost control and product quality. A manufacturing execution system (MES) addresses these challenges by improving traceability, automating workflows, and enhancing overall operational efficiency. The ability to capture real-time data, enforce process controls, and integrate with other enterprise systems makes MES an essential tool for manufacturers looking to improve compliance and productivity while reducing risks.
- Regulatory Compliance Support: Meeting FDA, ISO 13485, and Good Manufacturing Practices (GMP) requirements requires strict documentation, audit readiness, and validation. MES automates record-keeping, ensuring that all production data, process deviations, and quality checks are documented in real-time. This significantly reduces the risk of non-compliance while simplifying regulatory reporting and inspections.
- Complete Product Traceability: Manufacturing medical devices require detailed tracking of every component and material used in production. MES provides complete product genealogy, capturing serial numbers, lot numbers, and material sources from raw materials to finished products. This level of traceability enhances recall management, allowing manufacturers to quickly isolate and address defective batches, minimizing patient risk and regulatory consequences.
- Error Reduction and Process Standardization: Human errors in medical manufacturing can lead to serious safety concerns and regulatory violations. MES enforces standardized operating procedures (SOPs), ensuring operators follow defined assembly, testing, and inspection workflows. Digital work instructions guide workers through each process step, reducing variability and minimizing mistakes that could compromise product quality.
- Production Efficiency and Resource Optimization: Optimizing manufacturing workflows requires real-time visibility into production status, machine utilization, and labor efficiency. MES provides live data on work-in-progress (WIP), cycle times, and equipment performance, helping manufacturers identify bottlenecks and improve overall throughput. This reduces downtime, increases yield rates, and maximizes resource utilization. Automated Quality Control and Defect Management: Quality assurance in medical device manufacturing requires proactive defect detection and corrective action tracking. MES integrates with quality management systems (QMS) to capture inspection results, detect process deviations, and enforce corrective actions. Real-time monitoring helps manufacturers address quality concerns before they escalate, reducing waste and rework costs.
- Shorter Time-to-Market for New Products: Bringing a new medical device to market requires extensive testing, documentation, and validation before regulatory approval. MES accelerates this process by centralizing production data, automating batch record creation, and streamlining validation procedures. Faster access to real-time data allows manufacturers to make informed adjustments and ensure compliance without delaying product launches.
- Cost Reduction Through Waste Minimization: Material waste, excessive rework, and unplanned downtime can significantly impact production costs. MES improves inventory tracking, prevents overuse of materials, and provides insights into waste reduction opportunities. Manufacturers can lower production costs by minimizing defects, rework, and inefficiencies while maintaining high-quality standards.
- Seamless Integration with Enterprise Systems: Medical manufacturers often use multiple systems, including enterprise resource planning (ERP), product lifecycle management (PLM), and warehouse management solutions. MES is a central hub connecting these systems, ensuring data consistency across departments. This integration improves communication between design, production, and supply chain teams, improving coordination and efficiency.
Implementing MES in medical device manufacturing enhances operational efficiency, reduces compliance risks, and improves product quality. With advanced process control, real-time monitoring, and seamless data integration, manufacturers can streamline their operations while maintaining the highest safety and reliability standards.
Key Features of MES for Medical Devices
Medical device manufacturing requires precision, compliance, and real-time visibility into production processes. A manufacturing execution system (MES) provides the necessary tools to maintain strict quality standards while improving efficiency across every production stage. The ability to track materials, enforce process control, and integrate with enterprise systems ensures that manufacturers can meet regulatory requirements while optimizing operations. Key MES features designed for medical manufacturing improve traceability, automate data collection, and enhance production reliability.
Electronic Batch Records (EBR) for Compliance and Documentation
Maintaining accurate and complete batch records is critical for medical device manufacturing. MES replaces manual documentation with electronic batch records (EBR), ensuring that every step of production is automatically logged in a secure and audit-ready format. These records capture operator actions, machine settings, material usage, and process deviations, reducing the risk of human error and compliance violations. Automated record-keeping simplifies regulatory reporting, providing manufacturers faster access to production data during inspections or audits.
End-to-end traceability and Genealogy Tracking
Full product traceability is essential for medical devices, where even minor defects can have serious consequences. MES provides detailed genealogy tracking, recording every component and material used in production. Serial numbers and lot tracking allow manufacturers to trace individual devices to their source materials, suppliers, and production batches. In the event of a recall or compliance review, MES authorize quick identification of affected products, minimizing risk and improving response times.
Process and Quality Control Enforcement
Manufacturing medical devices require adherence to strict process control measures. MES enforces standard operating procedures (SOPs) by guiding operators through predefined workflows, preventing deviations that could impact quality. Integration with quality management systems (QMS) allows MES to capture real-time inspection results, flag defects, and trigger corrective actions. Automated quality control ensures that defective products are identified before distribution, reducing waste and preventing costly rework.
Real-Time Production Monitoring and Performance Analytics
Real-time visibility into production processes allows manufacturers to make informed decisions and improve operational efficiency. MES provides live tracking of work-in-progress (WIP), machine performance, and operator productivity. Data-driven insights help identify bottlenecks, optimize cycle times, and improve resource allocation. Dashboards and automated alerts provide instant updates on critical production metrics, allowing manufacturers to address inefficiencies before they impact output.
Digital Work Instructions and Operator Guidance
Medical device manufacturing involves complex assembly and testing procedures that require precision. MES provides digital work instructions that guide operators through each production step, ensuring consistency and reducing training time for new workers. Instructions can be updated in real time to reflect process changes or regulatory updates, ensuring that employees always follow the latest approved procedures. Visual aids, interactive checklists, and automated validation steps help reduce human errors and improve overall production accuracy.
Regulatory Compliance Management with Secure Data Logging
Compliance with FDA regulations, ISO 13485, and Good Manufacturing Practices (GMP) requires detailed record-keeping and controlled workflows. MES ensures compliance by automating data collection, securing electronic signatures, and maintaining audit trails. Secure data logging prevents unauthorized changes to production records, reducing the risk of compliance violations. Electronic records simplify audit preparation, allowing manufacturers to retrieve necessary documentation quickly and accurately.
Seamless Integration with ERP and PLM Systems
Medical manufacturers rely on multiple enterprise systems, including enterprise resource planning (ERP) and product lifecycle management (PLM). MES bridges these systems, ensuring seamless data flow between design, production, and supply chain operations. Real-time integration improves material planning, reduces delays, and ensures production aligns with forecasts. Synchronizing MES with ERP and PLM enhances overall efficiency and eliminates data silos.
Predictive Maintenance and Equipment Efficiency Monitoring
Unplanned equipment failures can lead to costly downtime and production delays. MES collects machine performance data, tracks usage patterns, and identifies potential failures before they occur. Predictive maintenance scheduling ensures equipment is serviced at optimal intervals, reducing unexpected breakdowns. Monitoring machine efficiency also helps manufacturers maximize production capacity while minimizing maintenance costs.
These key MES features provide medical device manufacturers with the tools to maintain regulatory compliance, improve product quality, and optimize production efficiency. Automating critical processes and ensuring real-time visibility allows companies to reduce risks, control costs, and meet the highest industry standards for precision and reliability.
Applications of MES in Medical Device Manufacturing
Medical device manufacturing requires strict control over production processes, compliance management, and quality assurance. A manufacturing execution system (MES) plays a vital role in optimizing operations, improving traceability, and ensuring real-time visibility into every stage of production. The ability to automate workflows, enforce regulatory requirements, and integrate with other enterprise systems makes MES a valuable asset for manufacturers looking to improve efficiency while maintaining compliance.
Production Process Control and Standardization
Medical device manufacturing involves complex workflows that must adhere to strict regulatory standards. MES enforces production consistency by standardizing processes, ensuring that each step follows predefined specifications. Automated workflow controls prevent unauthorized process deviations, reducing the risk of human errors and production defects. MES also tracks and validates each step-in real time, providing instant verification that all manufacturing activities meet established quality standards.
Material and Inventory Management for Accuracy and Efficiency
Raw materials and components used in medical device production must be precisely tracked to ensure compliance and product integrity. MES provides real-time visibility into inventory levels, reducing waste and preventing shortages that could disrupt production. Advanced tracking capabilities allow manufacturers to manage lot numbers, expiration dates, and supplier information, ensuring that only approved materials are used in production. Automated inventory updates improve material planning and reduce excess stock, optimizing warehouse efficiency.
Quality Assurance and Regulatory Compliance Enforcement
Ensuring that medical devices meet regulatory requirements is a top priority for manufacturers. MES integrates with quality management systems (QMS) to automate quality checks, inspection results, and deviation tracking. Real-time data collection allows for immediate detection of defects, triggering corrective actions before faulty products reach the market. Compliance enforcement features like electronic batch records (EBR), and digital signatures help manufacturers maintain audit-ready documentation while simplifying regulatory reporting.
Product Traceability and Recall Management
A strong traceability system is essential in medical manufacturing to track the entire lifecycle of a product. MES captures detailed genealogy data, recording every material, component, and process step involved in device production. Serial number and lot tracking provide complete visibility into each product’s history, ensuring rapid identification of affected devices in case of a recall. Automated traceability functions improve recall readiness, helping manufacturers respond quickly while minimizing patient risk and regulatory penalties.
Equipment Performance Monitoring and Predictive Maintenance
Unplanned equipment failures can disrupt production schedules and increase costs. MES collects real-time machine performance data, tracking usage patterns to predict potential failures before they occur. Predictive maintenance scheduling reduces unplanned downtime by servicing machines at optimal intervals. Monitoring equipment efficiency also helps manufacturers extend asset lifespan, reduce maintenance costs, and improve production reliability.
Operator Training and Certification Management
Medical device manufacturing requires skilled operators trained in industry regulations, safety standards, and process-specific tasks. MES tracks operator certifications, ensuring only qualified personnel perform critical manufacturing activities. Automated alerts notify managers when certifications are due for renewal, preventing compliance issues related to unqualified labor. Digital work instructions and real-time guidance further support operator training, reducing onboarding time and improving accuracy in production tasks.
These MES applications improve medical device manufacturing by enhancing process control, improving compliance readiness, and reducing production inefficiencies. Automating data collection, enforcing quality standards, and providing real-time production insights allow manufacturers to maintain high product quality while optimizing operational costs.
Challenges in Medical Device Manufacturing
Medical device manufacturing presents unique challenges due to strict regulatory requirements, complex production processes, and the need for absolute precision. Every product must meet rigorous safety and quality standards while maintaining efficiency in manufacturing operations. Companies in this sector must balance compliance, cost control, and product innovation while addressing ongoing industry challenges.
- Regulatory Compliance Complexity: Meeting FDA, ISO 13485, and Good Manufacturing Practices (GMP) standards requires extensive documentation, validation, and audits. Regulatory agencies impose strict guidelines on production processes, material traceability, and product testing. Failure to adhere to these requirements can result in costly delays, product recalls, or legal penalties.
- Supply Chain Disruptions and Material Sourcing Issues: Medical devices rely on specialized components and high-quality raw materials, which must meet strict regulatory and performance standards. Supply chain disruptions, geopolitical factors, and shortages of critical materials can slow production and increase costs. Manufacturers must develop contingency plans, establish reliable supplier networks, and implement real-time inventory tracking to minimize risks.
- Stringent Quality Control and Risk Management: Every medical device must be manufactured to exact specifications, leaving no room for errors or defects. Strict quality control measures must be enforced to detect potential deviations before products reach the market. Automated inspection systems, real-time monitoring, and corrective action tracking are essential for ensuring product reliability and patient safety.
- High Production Costs and Cost Control Pressures: Developing and manufacturing medical devices requires substantial investment in research, materials, equipment, and regulatory compliance. Production costs can rise due to material waste, inefficient workflows, and labor-intensive processes. Optimizing manufacturing efficiency through automation, MES integration, and predictive analytics helps companies maintain cost control without compromising quality.
- Product Traceability and Recall Preparedness: Medical device manufacturers must maintain complete traceability of all components and production processes. In case of a defect or safety concern, companies must quickly identify and recall affected products to minimize patient risk. MES solutions provide real-time tracking and batch genealogy, allowing manufacturers to trace products back to their source and take corrective action immediately.
- Workforce Training and Certification Management: Manufacturing medical devices requires a highly trained workforce understanding complex assembly processes and regulatory requirements. Keeping employees up to date with certifications, process changes, and safety protocols is essential to maintaining compliance. MES solutions help track training records, ensuring that only qualified personnel perform specific tasks.
- Spread Technological and Regulatory View: New medical technologies, advanced manufacturing techniques, and updated regulatory frameworks require companies to adapt continuously. Staying ahead of industry changes while maintaining compliance and production efficiency requires ongoing investment in research, process improvements, and workforce training.
Medical device manufacturers must these challenges while maintaining quality, compliance, and efficiency. Implementing an MES helps companies address these concerns by improving production visibility, automating compliance tasks, and optimizing manufacturing workflows.
Understanding Medical Device Manufacturing Costs
Medical device manufacturing involves substantial costs due to regulatory compliance, material sourcing, labor, and technology investments. Companies must carefully manage these expenses to maintain profitability while ensuring product quality and safety.
Regulatory requirements contribute significantly to manufacturing costs. Compliance with FDA standards, ISO 13485, and Good Manufacturing Practices (GMP) require extensive documentation, process validation, and ongoing quality assurance. Failure to meet these regulations can lead to costly rework, fines, or product recalls. Investing in an MES helps manufacturers streamline compliance efforts, reducing manual labor and documentation errors.
Material and equipment expenses also affect overall costs. High-grade materials, such as biocompatible metals and medical-grade polymers, are essential for device performance and patient safety. Precision manufacturing equipment, cleanroom facilities, and automation systems increase capital expenditures. Implementing MES allows manufacturers to optimize material usage, track inventory in real-time, and reduce waste, leading to cost savings.
Labor costs remain a key factor in medical device production. Skilled technicians, engineers, and quality control personnel must ensure that products meet strict standards. MES helps improve workforce efficiency by automating repetitive tasks, providing digital work instructions, and tracking operator performance. Reducing manual interventions lowers labor costs and minimizes human errors.
Managing these cost factors effectively requires data-driven and process optimization. MES provides real-time insights into production efficiency, resource utilization, and waste reduction, allowing manufacturers to control expenses while maintaining high product standards.
Emerging Trends in MES and Medical Device Manufacturing
Medical device manufacturing continues progressing as new technologies and process innovations improve efficiency, compliance, and production quality. Manufacturing execution systems (MES) are advancing to meet these requests, incorporating automation, data-driven insights, and enhanced connectivity. These trends shape how manufacturers produce, monitor, and manage medical devices, allowing for greater precision, lower costs, and improved regulatory adherence.
- AI-Powered Analytics and Predictive Quality Control: Artificial intelligence (AI) and machine learning (ML) are being integrated into MES to analyze production data, detect defects, and predict potential failures before they occur. AI-powered insights help manufacturers proactively improve quality control, reduce rework, and optimize production efficiency by identifying patterns that human operators may miss.
- Cloud-Based MES for Scalable Operations: Cloud-based MES solutions provide manufacturers with real-time access to production data across multiple facilities, better coordination and faster response times. Cloud integration reduces the need for on-premises IT infrastructure, making MES deployment more cost-effective while ensuring secure, centralized data storage and remote accessibility.
- Digital Twins for Process Optimization: Digital twin technology is used in medical device manufacturing to create virtual replicas of production. These digital models allow manufacturers to simulate, test, and refine production processes before implementation. Using MES-driven digital twins helps companies optimize workflows, improve product design, and minimize costly trial-and-error adjustments on the shop floor.
- IoT Smart Manufacturing for Real-Time Monitoring: Internet of Things (IoT) sensors enhance MES capabilities by providing continuous real-time data on equipment performance, and production metrics. These connected devices help manufacturers detect inefficiencies, schedule predictive maintenance, and ensure process parameters remain within strict regulatory limits.
- Paperless Manufacturing and Automated Documentation Compliance: The transition to fully digital manufacturing processes eliminates paper-based documentation, reduces errors, and improves compliance. MES solutions automate electronic batch records (EBR), digital work instructions, and real-time data collection, ensuring manufacturers maintain audit-ready documentation without relying on manual record-keeping.
- Cybersecurity Enhancements for Data Protection: As MES platforms become more connected through cloud computing and IoT integration, cybersecurity measures are strengthening to protect sensitive manufacturing and patient-related data. Advanced encryption, multi-factor authentication, and compliance with industry security frameworks help safeguard MES systems from cyber threats and unauthorized access.
- Advanced Robotics and Automation in Manufacturing: Integrating robotics with MES improves production accuracy and reduces manual labor requirements in medical device manufacturing. Automated assembly lines, robotic-assisted inspections, and AI-driven automation are increasing throughput while maintaining stringent quality control standards. MES synchronizes with these automation technologies to track performance, optimize workflows, and ensure compliance.
These emerging MES trends reshape medical device manufacturing by improving operational visibility, reducing waste, and increasing efficiency. As technology advances, manufacturers that adopt these innovations will be better equipped to manage compliance, reduce costs, and enhance overall production performance.
Manufacturers worldwide embrace cloud-based solutions to achieve efficiency, precision, and scalability. At 42Q, we combine decades of manufacturing expertise with cutting-edge technology to deliver innovative, connected manufacturing. Our flexible, cloud-native MES platform enhances visibility, streamlines operations, and accelerates digital transformation. Discover how our solutions can empower your factory to achieve its full potential.
Key Takeaways
- Regulatory compliance is a significant challenge in medical device manufacturing, requiring strict documentation, process validation, and traceability. MES automates these processes, reducing errors and ensuring audit-ready records.
- Traceability plays a critical role in medical manufacturing by tracking components, materials, and production history. MES improves recall readiness and enhances product quality by providing complete genealogy tracking.
- Production efficiency is optimized through MES by enforcing standard operating procedures, reducing downtime, and monitoring equipment performance in real time. Manufacturers can improve output while maintaining precision.
- Medical device manufacturers face challenges such as supply chain disruptions, high production costs, and workforce training requirements. MES addresses these concerns by automating workflows, improving resource planning, and supporting operator certification management.
- Emerging trends in MES include AI-driven analytics, cloud-based solutions, and IoT smart manufacturing. These innovations improve quality control, enhance process automation, and provide real-time production insights.
FAQs
Medical device manufacturing involves designing, producing, and testing medical equipment used for diagnosis, treatment, and patient monitoring. Regulations such as FDA requirements and ISO 13485 ensure that these devices meet strict safety, quality, and reliability standards. Compliance with these regulations minimizes the risk of defective products that could harm patients or lead to costly recalls.
An MES tracks materials, components, and production processes in real time, ensuring complete product genealogy. This traceability allows manufacturers to quickly identify and isolate defective batches, making recall management more efficient. By capturing serial numbers, lot data, and operator actions, MES provides a transparent record of every step-in manufacturing.
MES enhances regulatory compliance, automates data collection, and improves production efficiency. It reduces human errors, enforces standardized workflows, and integrates with enterprise systems for seamless data sharing. These capabilities help manufacturers control costs, increase product quality, and accelerate time-to-market for new medical devices.
MES minimizes waste, optimizes resource allocation, and prevents production inefficiencies. Automated tracking of inventory and materials reduces excess stock and prevents shortages that lead to production delays. By improving machine utilization and reducing rework, MES helps manufacturers lower operational costs while maintaining high standards.
Advancements such as AI-powered analytics, cloud-based MES, and IoT smart manufacturing are growing medical device production. Predictive maintenance, digital twins, and automated documentation compliance enhance efficiency and reduce downtime. As cybersecurity improves, manufacturers can securely adopt these innovations while ensuring compliance with regulatory standards.