MES and SCADA Integration Explained
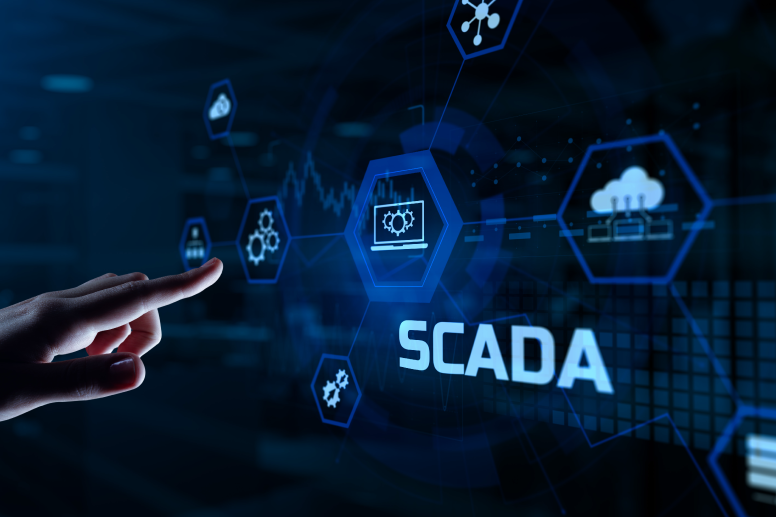
MES and SCADA Integration Explained
MES and SCADA systems are two of the most powerful technologies that are transforming manufacturing.
MES focuses on managing production workflows, while SCADA provides real-time control and monitoring of equipment and processes. They create a foundation for operational efficiency, quality assurance, and data-driven decision-making. Leveraging these systems allows manufacturers to meet industry demands for scalability, precision, and traceability while optimizing their resources and workflows.
What is a MES?
A Manufacturing Execution System (MES) is a comprehensive software solution designed to monitor, manage, and optimize manufacturing operations in real time. It bridges the gap between high-level business systems, such as Enterprise Resource Planning (ERP) platforms, and the shop floor, where production occurs. MES solutions track, document, and control the transformation of raw materials into finished goods, ensuring production processes are efficient, consistent, and of high quality.
The core purpose of an MES is to provide real-time visibility and control over manufacturing operations. It captures data from machines, operators, and processes, enabling manufacturers to improve production efficiency, enforce product traceability, and maintain compliance with industry regulations. By delivering insights into production performance, MES systems help manufacturers reduce downtime, improve cycle times, and meet quality standards.
In practice, MES solutions are highly versatile. They can manage workflows, enforce production schedules, track inventory in real-time, and monitor equipment performance. This makes them an essential tool for manufacturers aiming to streamline operations and meet the growing demands for customization, quality, and speed in production.
What is a SCADA System?
A Supervisory Control and Data Acquisition (SCADA) system is an industrial control system designed to monitor and control processes across large-scale operations. It gathers real-time data from sensors and devices across a facility, processes that data, and allows operators to monitor and manage operations through centralized interfaces. SCADA systems are essential for industries such as energy, water treatment, transportation, and manufacturing, where maintaining control over distributed systems is critical.
SCADA systems provide operators with a detailed view of equipment and process performance, ensuring they can quickly identify issues and take corrective action when necessary. These systems often include components such as programmable logic controllers (PLCs), remote terminal units (RTUs), and human-machine interfaces (HMIs) to collect and visualize data.
A defining feature of SCADA is its ability to support remote monitoring and control. Operators can use SCADA to manage systems located miles away, such as a network of pipelines or substations. This capability reduces the need for on-site personnel and enhances operational efficiency by providing real-time access to critical process data. SCADA systems are designed to improve reliability, prevent downtime, and maintain the seamless operation of complex industrial processes.
Key Differences Between SCADA and MES
The main difference between SCADA and MES lies in their scope and functionality. SCADA focuses on real-time monitoring and control of equipment and processes, while MES manages the entire manufacturing lifecycle, from scheduling and production tracking to quality assurance and compliance. These systems often complement each other but serve distinct roles within manufacturing operations.
SCADA is primarily a control system designed for operational tasks. It gathers data from sensors and devices on the production floor, enabling operators to monitor performance and adjust settings to maintain process efficiency. SCADA excels at providing insights into machine-level operations, making it ideal for detecting and responding to equipment malfunctions or process deviations.
Conversely, MES operates at a higher level, integrating data from multiple sources to optimize production workflows and ensure traceability. While SCADA systems are focused on guaranteeing equipment and processes run smoothly, MES provides a broader perspective by aligning shop floor activities with business goals. MES incorporates data from SCADA but also includes tools for production planning, inventory management, and performance analytics, making it indispensable for driving long-term operational improvements.
Aspect | MES | SCADA |
Core Purpose | Manages the entire production lifecycle, ensuring efficiency, quality, and traceability. | Monitors and controls real-time equipment performance and ensures process stability. |
Primary Function | Connects shop floor operations with enterprise systems for holistic management. | Provides real-time data and immediate control of machinery and processes. |
Focus Area | Strategic production planning, resource allocation, and performance tracking. | Operational control and ensuring equipment operates within specified parameters. |
Integration | Links with ERP systems for enterprise-wide visibility and alignment with business goals. | Interfaces with sensors, PLCs, and actuators for shop floor monitoring and control. |
Data Utilization | Analyzes data for trends, optimization, and long-term improvements. | Collects and uses real-time data for immediate operational adjustments. |
User Base | Designed for managers and decision-makers to drive high-level production strategies. | Primarily used by operators and technicians for equipment monitoring and stability. |
Integrating MES and SCADA provides manufacturers with a comprehensive solution for managing operations efficiently at all levels. SCADA ensures real-time process stability and equipment monitoring, while MES enhances long-term production strategies and aligns workflows with organizational goals. Leveraging both systems allows businesses to achieve scalability, minimize downtime, and maintain operational excellence in manufacturing environments.
Business Benefits of Integrating MES and SCADA Systems
"The synchronization of MES and SCADA ensures that production workflows are optimized based on machine performance and availability."
Integrating MES (Manufacturing Execution Systems) and SCADA (Supervisory Control and Data Acquisition) offers significant advantages for manufacturing operations. These systems work together to create a seamless connection between real-time process control and higher-level production management. The integration enhances efficiency, ensures consistent quality, and delivers actionable insights to optimize workflows and resource utilization. Manufacturers leveraging this integration can streamline their operations, reduce costs, and maintain operational resilience in dynamic production environments.
- Improved Real-Time Decision-Making: SCADA systems deliver real-time equipment performance data, while MES translates this into actionable insights for planning. This enables managers to identify inefficiencies, reduce response times, and make informed decisions to keep operations running smoothly.
- Enhanced Operational Efficiency: MES and SCADA integration ensures workflows are optimized based on machine performance and availability. MES dynamically adjusts production schedules in response to real-time SCADA data, minimizing delays and ensuring operations remain efficient as production scales.
- Increased Product Quality and Consistency: Combining SCADA’s real-time monitoring with MES-driven quality control ensures defects are detected early in the production process. This reduces waste, prevents defective products from reaching customers, and supports consistent delivery of high-quality goods.
- Comprehensive Traceability and Compliance: Integrated MES and SCADA systems provide detailed tracking of production processes, helps with compliance with industry regulations and supporting customer demands for transparency. This level of traceability helps manufacturers quickly trace issues back to their sources and address them efficiently.
- Predictive Maintenance and Reduced Downtime: SCADA monitors equipment performance, while MES uses this data to predict maintenance needs. This proactive approach prevents unexpected equipment failures, extends asset lifecycles, and reduces costly downtime, allowing steady production.
- Holistic Visibility Across Operations: Integration eliminates silos between shop floor data and enterprise systems, providing centralized visibility of the entire production process. This enhanced collaboration ensures shop floor data informs high-level business strategies effectively.
- Cost savings and ROI improvements: The operational efficiencies created by integrating MES and SCADA systems translate into tangible cost savings. Reduced material waste, optimized labor allocation, and lower energy usage all contribute to significant reductions in production costs. Additionally, better process control and traceability lessen the financial impact of product recalls or compliance violations.
Integrating MES and SCADA systems transforms manufacturing processes by aligning real-time equipment control with comprehensive operational oversight. This combined approach improves efficiency, reduces costs, and supports production flexibility, positioning manufacturers to succeed. MES and SCADA together create a unified framework that allows businesses to scale operations, maintain consistent quality, and adapt seamlessly to future challenges.
When to Use MES or SCADA
Selecting the appropriate system for your manufacturing operations depends on your specific needs and goals. MES (Manufacturing Execution Systems) and SCADA (Supervisory Control and Data Acquisition) serve different yet complementary roles. MES is designed to optimize production workflows, manage resources, and ensure compliance, while SCADA focuses on real-time monitoring and control of equipment. Each system addresses unique challenges, offering distinct benefits that cater to various aspects of manufacturing processes.
Understanding the differences between MES and SCADA enables manufacturers to implement the right solution or combination of systems to meet operational requirements. Whether ensuring precision at the equipment level or aligning production with strategic objectives, both systems provide critical tools to improve productivity and scalability.
MES: Ideal for Comprehensive Production Management
MES is the go-to solution for manufacturers aiming to streamline and optimize complex production processes. It enables centralized management of production workflows, ensuring seamless coordination between multiple manufacturing stages. MES is particularly valuable in industries with intricate production schedules, where efficient resource allocation and real-time tracking are essential for meeting demand.
Another critical use case for MES is regulatory compliance. Industries such as medical devices and aerospace often require detailed documentation of production processes to meet strict regulatory standards. MES ensures full traceability by capturing raw materials, production activities, and finished goods data. This facilitates compliance and enhances customer confidence by guaranteeing product quality.
MES also shines in multi-plant operations. Manufacturers managing production across multiple facilities benefit from MES’s ability to standardize workflows, centralize data, and ensure consistent quality. The insights gained from MES reporting tools allow businesses to identify inefficiencies and implement data-driven improvements.
SCADA: Best for Real-Time Process Monitoring and Control
SCADA systems are indispensable for manufacturers and industries requiring precise, real-time control of equipment and processes. They excel in environments where operational safety and reliability are non-negotiable. SCADA provides operators with a live view of equipment performance, making it easier to detect and respond to anomalies immediately. This capability is especially critical in the energy, water treatment, and utilities industries.
Remote system management is another area where SCADA stands out. SCADA enables centralized monitoring and control for geographically distributed operations, such as pipelines or multi-site manufacturing facilities. Operators can manage systems without being on-site, reducing travel and response times while improving operational efficiency.
SCADA also supports critical process control by maintaining precise control over temperature, pressure, and flow rates. This makes it an essential tool for industries where maintaining consistent process parameters is key to producing quality outputs and avoiding safety risks.
Integrating MES and SCADA for Optimal Results
Integrating MES and SCADA creates a powerful combination that leverages the strengths of both systems. MES utilizes the granular, real-time data captured by SCADA to enhance production planning, quality control, and compliance efforts. For example, SCADA data on machine performance can inform MES decisions about production scheduling, ensuring workflows remain efficient even during maintenance or downtime.
This integration mainly benefits manufacturers aiming to scale their operations or manage complex, multi-site networks. The combined capabilities of MES and SCADA offer comprehensive visibility into operations, enabling organizations to align shop floor performance with broader business goals.
MES and SCADA systems are essential tools for modern manufacturing, each addressing specific needs within the production process. MES ensures efficient management of resources and workflows, while SCADA delivers precise, real-time equipment control. Integrating the two systems enables manufacturers to achieve a balance between operational stability and strategic scalability. With their combined strengths, businesses can improve efficiency, maintain compliance, and meet production demands with confidence.
Integration Aspect | Key Benefit |
Real-Time Data Utilization | SCADA captures live equipment data, which MES uses to optimize production schedules and workflows. |
Seamless Decision-Making | SCADA provides immediate feedback on process performance, while MES translates this into actionable insights for both tactical and strategic decisions. |
Enhanced Operational Visibility | Integration bridges the gap between shop floor data (via SCADA) and enterprise-level management (via MES), creating a unified view of production. |
Predictive Maintenance | SCADA tracks machine wear and tear, while MES analyzes the data to forecast maintenance needs, reducing unplanned downtime. |
Scalability Across Sites | MES consolidates SCADA data from multiple locations, enabling centralized control and efficient scaling for complex networks. |
Improved Quality Control | SCADA detects real-time process deviations, and MES integrates this data into quality assurance processes for consistent output. |
Streamlined Compliance | MES leverages SCADA’s detailed process data to support traceability, ensuring regulatory requirements are met across production stages. |
Challenges in Implementing SCADA and MES
Integrating SCADA and MES systems into manufacturing operations presents immense opportunities but also comes with significant challenges. These systems are crucial for improving efficiency, assisting with compliance, and streamlining production, but their successful implementation requires overcoming obstacles like integration complexities, high costs, and workforce readiness. Tackling these challenges effectively ensures manufacturers unlock the full potential of these advanced systems and achieve long-term operational success.
Navigating these challenges demands a careful approach, addressing both technical and organizational barriers to ensure smooth adoption. Below are some of the most common hurdles manufacturers face during SCADA and MES implementation and how they can be mitigated.
- Integration Complexity: Connecting SCADA and MES to legacy equipment, outdated software, or diverse infrastructure often requires overcoming compatibility issues. Establishing seamless data communication across facilities is critical but can demand significant resources and technical expertise.
- High Upfront Costs and Resource Allocation: Implementing SCADA and MES systems involves investments in hardware, software, and support services. Smaller manufacturers, in particular, may face financial strain when managing infrastructure upgrades and customization. Strategic planning ensures these costs yield measurable ROI.
- Data Security Concerns: SCADA and MES systems often rely on internet connectivity, increasing the risk of data breaches or cyberattacks. Encryption, firewalls, and continuous monitoring are essential to protecting sensitive production data and assisting with compliance with industry regulations.
- Workforce Readiness and Training Needs: Employees must adapt to new systems and workflows, which requires effective training programs and support. Lack of technical expertise or resistance to change can hinder implementation. Comprehensive training reduces these risks and ensures smooth adoption.
- Implementation Downtime and Disruption: Deploying SCADA and MES systems may require production halts for installation and testing. Poor planning can disrupt schedules and affect customer commitments. Phased rollouts minimize these disruptions while maintaining productivity.
Overcoming the challenges of SCADA and MES implementation ensures that manufacturers achieve maximum value from their investment. A successful deployment requires strategic planning, collaboration with stakeholders, and comprehensive employee training. When these barriers are addressed effectively, manufacturers gain enhanced visibility, operational efficiency, and the ability to meet production demands with confidence.
Real-World Applications of MES and SCADA
MES and SCADA systems have become essential tools across various industries, addressing unique operational challenges and driving measurable results. MES excels in managing production workflows, resource allocation, and compliance, while SCADA specializes in real-time equipment monitoring and control. Together, they create a seamless framework that enhances efficiency, maintains quality, and ensures process stability.
Different industries apply these systems in distinct ways to meet their specific needs. From helping with compliance in highly regulated sectors to optimizing large-scale manufacturing processes, MES and SCADA integration plays a pivotal role in modernizing operations and delivering consistent value.
Medical Device Manufacturing
Medical device manufacturers rely on MES systems to meet strict regulatory requirements and ensure product quality. MES enables complete traceability of materials and processes, from raw materials to finished goods. SCADA systems complement this by providing real-time monitoring of production environments, ensuring critical parameters such as temperature and pressure are maintained. This combination supports with compliance with industry standards while minimizing risks associated with defective products.
Automotive Manufacturing
Automotive production lines benefit significantly from the integration of MES and SCADA systems. MES ensures production workflows remain efficient and aligned with delivery schedules, while SCADA monitors the performance of robots, conveyors, and other machinery in real-time. Together, these systems enable faster issue detection, optimize cycle times, and improve production consistency, which is essential for meeting the high demands of this industry.
Energy and Utilities
SCADA systems are central to managing energy grids, water treatment plants, and other utilities, where real-time data is critical to maintaining system reliability. MES adds value by analyzing SCADA data to optimize workflows, schedule maintenance activities, and forecast operational demands. This integration enhances system resilience, reduces downtime, and ensures service continuity for millions of users.
Food and Beverage Production
In the food and beverage industry, SCADA systems monitor and control temperature, humidity, and production line speeds, ensuring product safety and quality. MES provides end-to-end traceability and manages workflows to prevent cross-contamination and waste. These systems help manufacturers comply with stringent safety standards and maintain product consistency.
Semiconductor Manufacturing
Semiconductor production involves complex processes that require precision and control. SCADA systems provide real-time data on critical variables such as temperature, vacuum levels, and process times, ensuring the integrity of production runs. MES leverages this data to track lot histories, manage scheduling, and ensure that every chip produced meets quality specifications. This integration supports the high accuracy and traceability demanded by the semiconductor industry.
The adoption of MES and SCADA systems continues to enhance industries by solving complex operational challenges and enabling smarter, more efficient processes. Whether improving regulatory compliance, ensuring product traceability, or optimizing equipment performance, these systems provide manufacturers with the tools needed to succeed. Tailored to the unique requirements of each industry, MES and SCADA integration delivers long-term operational stability and business growth.
Measuring ROI of MES and SCADA Integration
Measuring the return on investment (ROI) of MES and SCADA integration involves assessing their impact on operational performance, cost savings, and scalability. One of the most immediate benefits comes from enhanced efficiency. Real-time data from SCADA enables MES to dynamically adjust production schedules, ensuring optimal use of labor and equipment while minimizing waste. These improvements reduce downtime and operational inefficiencies, delivering measurable cost savings over time.
Improved product quality is another significant ROI driver. MES leverages SCADA data to monitor processes and enforce quality standards, reducing defects and ensuring consistency. High-quality outputs minimize costs associated with rework and compliance violations while boosting customer satisfaction and loyalty. This, in turn, supports revenue growth by maintaining trust and reliability in production.
Scalability and predictive maintenance further contribute to ROI. MES and SCADA systems provide the tools manufacturers need to expand operations efficiently, whether adding new production lines or managing multi-site networks. Additionally, SCADA tracks equipment performance data, enabling MES to schedule proactive maintenance, reducing repair costs and preventing production disruptions. These benefits are measurable through key performance indicators (KPIs), such as defect rate reductions, maintenance cost savings, and cycle time improvements, showcasing the significant value MES and SCADA systems bring to modern manufacturing.
Manufacturers worldwide embrace cloud-based solutions to achieve efficiency, precision, and scalability. At 42Q, we combine decades of manufacturing expertise with cutting-edge technology to deliver smart, connected manufacturing. Our flexible, cloud-native MES platform enhances visibility, streamlines operations, and accelerates digital transformation. Discover how our solutions can empower your factory to achieve its full potential.
Key Takeaways
- SCADA focuses on real-time monitoring and control, while MES manages production workflows and ensures traceability.
- Integrating MES and SCADA systems optimize production efficiency, quality, and resource utilization across operations.
- SCADA excels in environments requiring precision control and monitoring, while MES is essential for managing complex manufacturing lifecycles.
- Real-world applications include automotive production, semiconductor manufacturing, and food safety compliance.
- Challenges like integration complexity, data security, and workforce readiness must be addressed for successful implementation.
FAQ's
SCADA systems monitor and control real-time equipment and process performance in manufacturing environments. They collect data from sensors and devices across production lines, enabling operators to manage operations remotely, detect issues early, and maintain consistent output. This system is essential for industries that rely on precision and uninterrupted production.
MES is focused on managing the entire production lifecycle, including workflows, inventory, and quality, while SCADA handles real-time equipment control and monitoring. MES integrates data from SCADA to optimize production processes, but it also includes broader management tools such as scheduling and performance analytics.
Yes, SCADA systems can operate independently for real-time monitoring and control of equipment. However, integrating SCADA with MES provides enhanced benefits, such as improved decision-making, end-to-end traceability, and alignment between shop floor performance and business objectives.
Industries such as automotive, semiconductor manufacturing, energy, medical devices, and food production gain significant advantages from integrating MES and SCADA. These sectors rely on precise process control, traceability, and the ability to adapt quickly to production demands.
MES and SCADA integration delivers ROI through increased efficiency, reduced downtime, improved product quality, and predictive maintenance. Manufacturers also benefit from enhanced traceability, regulation compliance, and scalability to support business growth, leading to long-term financial and operational advantages.