The Future of Automotive Manufacturing and MES
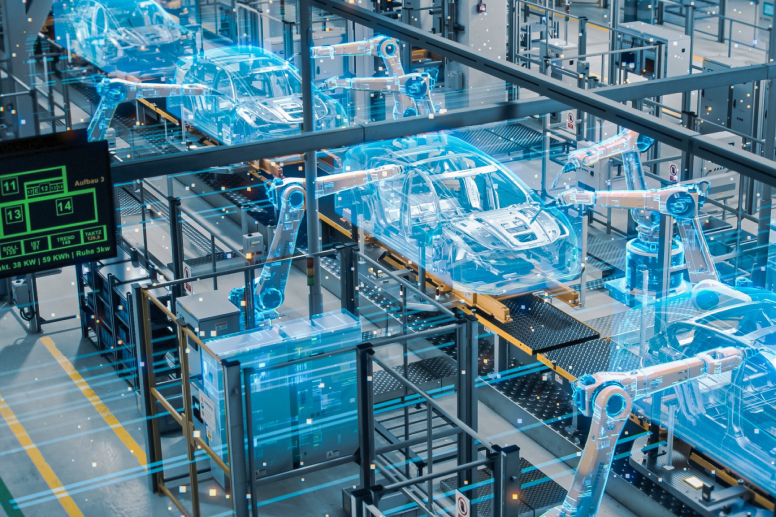
The Future of Automotive Manufacturing and MES
Manufacturing Execution Systems (MES) are forming automotive production, improving efficiency, quality, and traceability across the factory floor.
As manufacturing complexity increases, companies must manage production schedules, reduce waste, and meet regulatory requirements while maintaining cost control. MES bridges the gap between enterprise resource planning (ERP) systems and factory operations, providing real-time data, automation, and process optimization. Automotive manufacturers adopting MES gain improved visibility, streamlined workflows, and enhanced production capabilities, ensuring they meet the growing industry with greater precision and reliability.
What is Automotive Manufacturing in MES?
Automotive manufacturing involves complex processes that form raw materials into fully functional vehicles. This industry relies on precision engineering, supply chain coordination, and quality control to ensure production efficiency and product reliability. Manufacturers seek solutions to enhance operations while reducing costs and production timelines as technology advances.
A Manufacturing Execution System (MES) plays an essential role in modern automotive production by bridging the gap between enterprise resource planning (ERP) systems and factory floor operations. MES provides real-time monitoring, data collection, and process automation, helping manufacturers optimize production workflows, improve traceability, and ensure compliance with industry regulations. With increasing efficiency and scalability, MES solutions are now essential for manufacturers looking to streamline operations and meet customer expectations.
Benefits of MES in Automotive Manufacturing
Automobile manufacturers must maintain high production standards while adapting to shifting market conditions. MES improves factory operations by providing digital tools that track performance, optimize workflows, and enhance overall productivity. These benefits help manufacturers lower costs, reduce errors, and maintain consistency throughout production.
- Production efficiency: MES automates data collection, reducing manual errors and ensuring accurate process tracking. This improves workflow efficiency and minimizes production downtime.
- Quality control: Real-time monitoring allows manufacturers to detect and address defects before they escalate, improving product quality and reducing waste.
- Traceability and compliance: MES provides full product traceability, recording each manufacturing process step. This helps meet regulatory requirements and improves audit readiness.
- Workforce optimization: Operators receive digital work instructions, reducing training time and enhancing worker efficiency on the factory floor.
- Supply chain visibility: MES integrates with ERP and other business systems, providing better visibility into material availability and production schedules. This improves planning and reduces delays.
- Cost reduction: Process automation and predictive maintenance reduce material waste, energy consumption, and unplanned downtime, lowering production costs.
- Scalability: MES supports multi-plant operations, allowing manufacturers to standardize processes across multiple facilities while maintaining centralized control.
Manufacturers implementing MES gain better control over production while improving agility in responding to operational challenges. These advantages make MES an essential tool for automotive companies looking to improve efficiency and maintain high-quality manufacturing standards.
Examples of MES in Automotive Manufacturing
Manufacturers rely on MES to improve efficiency, maintain product quality, and meet production goals. The system integrates with factory operations to support automation, provide real-time insights, and improve traceability. These capabilities address specific challenges in automotive manufacturing, ensuring consistent results across production lines.
1. Digital Work Instructions for Assembly Processes
Automotive production involves assembling thousands of components with precision. MES provides digital work instructions, guiding operators through each step with real-time updates. This reduces errors, minimizes rework, and ensures each vehicle meets quality standards. Operators can also receive automated alerts for process deviations, preventing defects before they affect production.
2. Production Monitoring and Performance Analytics
Factory performance depends on accurate data collection and analysis. MES tracks production rates, machine uptime, and operator efficiency, providing manufacturers with real-time insights into performance metrics. These analytics help identify bottlenecks and inefficiencies, allowing process adjustments that improve production speed and output quality.
3. Traceability for Compliance and Quality Assurance
Automotive manufacturing requires complete traceability of parts and materials to meet industry regulations. MES records each step of production, capturing data on material origins, assembly processes, and quality checks. If a defect occurs, manufacturers can trace the issue back to its source and take corrective action, reducing the risk of recalls and compliance violations.
4. Automated Inventory and Supply Chain Integration
Supply chain coordination is essential to prevent material shortages and production delays. MES integrates with inventory management systems, tracking material usage in real time and automating restocking processes. This prevents overstocking or understocking issues, ensuring materials arrive at the right time to maintain production schedules.
5. Predictive Maintenance to Reduce Downtime
Equipment failures cause unplanned downtime, delaying production and increasing costs. MES uses predictive maintenance tools to monitor machine performance and detect potential failures before they happen. Automated alerts notify maintenance teams when repairs or servicing are needed, preventing breakdowns and extending equipment lifespan.
Automotive manufacturers rely on MES to enhance production processes, improve quality control, and optimize resource allocation. These applications make MES a critical tool for increasing efficiency while reducing costs and minimizing operational risks.
Challenges in Automotive Manufacturing
Automotive manufacturers face complex operational challenges that affect production efficiency, cost control, and regulatory compliance. Meeting industry requirements while maintaining high output levels requires advanced solutions to manage factory operations effectively. MES helps address these obstacles by providing visibility, automation, and process control.
- Supply chain disruptions: Material shortages, supplier delays, and logistical constraints slow production. Manufacturers must adjust schedules and inventory levels to avoid production halts.
- Quality assurance and defect management: Identifying defects early in the process reduces rework and scrap costs. Without a formed tracking system, maintaining consistent product quality becomes difficult.
- Equipment downtime and maintenance inefficiencies: Unexpected equipment failures lead to production stoppages, increasing costs and delaying deliveries. Predictive maintenance and performance monitoring help minimize unplanned downtime.
- Regulatory compliance and traceability: Automotive manufacturers must meet strict safety regulations. Tracking materials, production steps, and testing data ensure compliance while reducing the risk of recalls.
- Production scalability: Expanding production capacity requires standardizing processes across multiple facilities. Without centralized control, scaling operations lead to inconsistencies and inefficiencies.
- Workforce training and process standardization: Operator errors and inefficient workflows reduce production speed. Digital work instructions and automated process controls improve training effectiveness and operational consistency.
- Energy consumption and sustainability requirements: Reducing waste and improving energy efficiency helps manufacturers lower costs and meet goals. Process optimization and resource monitoring provide better control over energy usage.
Manufacturers that address these challenges improve production efficiency, product quality, and overall operational stability. MES provides solutions that help factories optimize resources, reduce costs, and maintain compliance with industry regulations.
How to Improve Efficiency in Automotive Manufacturing with MES
Manufacturers rely on MES to improve production efficiency, reduce operational risks, and optimize factory performance. The system provides data-driven insights, automation tools, and real-time monitoring to streamline processes. These capabilities help factories maintain quality while minimizing costs and production delays.
Automating Data Collection and Process Tracking
Manual data entry slows production and increases the risk of errors. MES automates data collection, capturing real-time production metrics from machines, sensors, and operators. This ensures accurate tracking of key performance indicators (KPIs) such as cycle times, defect rates, and machine utilization. Automated data reporting allows manufacturers to identify inefficiencies and adjust processes to improve productivity.
Optimizing Production Scheduling and Resource Allocation
Balancing production schedules with material availability and workforce capacity prevents delays and inefficiencies. MES synchronizes scheduling with inventory and labor management systems, ensuring that materials arrive on time and operators follow optimized workflows. This reduces bottlenecks, minimizes idle time, and maximizes overall production output.
Enhancing Quality Control with Real-Time Monitoring
Defects impact production costs and customer satisfaction. MES integrates with quality control systems to monitor product specifications, detect anomalies, and flag defects as they occur. Automated alerts notify operators when deviations happen, allowing immediate corrective actions. This reduces waste, improves product consistency, and lowers rework costs.
Implementing Predictive Maintenance to Minimize Downtime
Equipment failures lead to unplanned downtime and increased repair costs. Some MES solutions offer capabilities that address equipment downtime. These systems are capable of collecting data on machine performance and, depending on their features, may be able to predict maintenance requirements using historical data and real-time sensor inputs. This allows for proactive maintenance, with alerts being sent when servicing is needed, which can reduce unexpected failures. The goal of such features is to improve equipment reliability and prolong machine lifespans, minimizing production disruptions.
Standardizing Work Instructions for Consistent Operations
Operators need clear instructions to follow best practices and maintain process consistency. MES provides digital work instructions, ensuring each step of production is performed correctly. These instructions update in real-time based on machine status, production requirements, or regulatory changes. Standardizing workflows improves worker efficiency and reduces errors across multiple shifts and facilities.
Improving Traceability for Compliance and Supply Chain Visibility
Tracking materials, parts, and production processes ensures compliance with industry regulations. MES records each manufacturing stage, linking product batches to raw material sources and assembly data. This improves supply chain visibility and allows manufacturers to trace defects to their origin, reducing liability and improving quality control.
Reducing Waste and Improving Sustainability Efforts
Material waste and energy consumption increase production costs. Some Manufacturing Execution Systems (MES) can offer features that help manufacturers track things like energy use, material waste, and how efficiently materials are being used. This data can then be used to find ways to make processes better, reduce resource consumption, and be more environmentally friendly. If done well, this can help lower costs and meet environmental rules
Manufacturers using MES gain better control over production, improving efficiency while maintaining quality and compliance standards. The system provides the tools to optimize factory operations and reduce costs in an industry.
Evolution of Automotive Manufacturing and MES
Automotive manufacturing has advanced through technological innovations that improve efficiency, safety, and product quality. MES has adapted to support these advancements, providing digital tools that connect production processes and optimize factory operations. The industry's progression reflects a shift toward automation, data-driven strategy, and integrated manufacturing systems.
- Early mass production: The introduction of assembly lines standardized vehicle manufacturing, reducing production time and increasing output. Manual processes dominated, relying on human oversight and repetitive tasks.
- Introduction of automation: Robotics and computer-controlled machinery improved precision and consistency, reducing human error and increasing production speed. Automation helped streamline repetitive tasks while improving safety and efficiency.
- Integration of digital monitoring systems: Manufacturers adopted early versions of MES to track production metrics, monitor machine performance, and manage work orders digitally. These systems provided essential real-time insights but lacked full integration capabilities.
- Expansion of data-driven manufacturing: Advanced MES platforms integrated with ERP and supply chain systems allow manufacturers to analyze performance data and optimize workflows across multiple facilities. Predictive analytics and process automation further improved production efficiency.
- Adoption of smart factories: Modern MES solutions incorporate artificial intelligence, machine learning, and cloud computing to connect production lines with enterprise systems. Smart factories use real-time data to improve traceability, automate and improve production control.
- Sustainability and energy-efficient manufacturing: MES often includes tools for tracking resource consumption, optimizing energy use, and reducing material waste. These capabilities help manufacturers meet standards while lowering operational costs.
Automotive manufacturing continues to grow with advancements in automation, digital connectivity, and sustainability initiatives. MES is vital in supporting these developments, ensuring manufacturers achieve higher efficiency, lower costs, and improved production outcomes.
Key Trends in Automotive Manufacturing and MES
Manufacturers continue integrating innovative technologies into production, improving efficiency and reducing costs through automation and data-driven insights. MES is essential in optimizing factory operations by incorporating artificial intelligence, Internet of Things (IoT) connectivity, and predictive analytics. Cloud-based MES solutions allow greater scalability and system accessibility, reducing the need for expensive on-premise infrastructure. Sustainability initiatives drive the adoption of energy-efficient manufacturing practices, with an MES capable of monitoring real-time resource consumption to minimize waste. Cybersecurity measures remain a priority as factories connect more systems and data sources, ensuring that production information remains secure. MES-ERP integration strengthens business continuity, aligning production workflows with broader enterprise objectives for better inventory control, planning, and efficiency. Automotive manufacturers rely on these advancements to improve quality, reduce downtime, and maintain compliance with industry regulations.
Manufacturers worldwide are adopting cloud-based solutions to improve efficiency, precision, and scalability. At 42Q, we combine decades of manufacturing expertise with cutting-edge technology to deliver innovative, connected manufacturing. Our flexible, cloud-native MES platform enhances visibility, streamlines operations, and accelerates digital transformation. Discover how our solutions can empower your factory to achieve its full potential.
Key Takeaways
- MES improves efficiency in automotive manufacturing by automating workflows, reducing downtime, and providing real-time visibility into production processes.
- Traceability features help manufacturers maintain compliance by tracking materials, components, and assembly processes throughout the production cycle.
- Predictive maintenance reduces machine failures and unplanned downtime by monitoring equipment health and scheduling repairs before breakdowns occur.
- Cloud-based MES solutions enhance scalability and flexibility by integrating factory operations across multiple facilities and improving data accessibility.
- MES-ERP integration strengthens manufacturing operations by aligning production schedules, resource planning, and inventory control with business objectives.
FAQs
MES improves efficiency by automating data collection, optimizing production scheduling, and reducing downtime through predictive maintenance. The system provides real-time monitoring, allowing manufacturers to adjust workflows, minimize bottlenecks, and maintain consistent output. With MES, production processes become more reliable, scalable, and cost-effective.
A comprehensive MES includes production tracking, quality management, resource planning, and traceability features. These components ensure real-time visibility into factory operations, helping manufacturers maintain compliance, reduce waste, and optimize machine utilization. Integrated digital work instructions also enhance operator efficiency and process consistency.
Traceability ensures compliance with safety regulations, reduces liability, and improves quality control by tracking each step in the manufacturing process. MES provides a digital record of materials, assembly processes, and testing data, allowing manufacturers to quickly identify and correct defects. This level of oversight helps prevent costly recalls and production delays.
MES uses machine data and sensor inputs to detect potential equipment failures before they happen. Predictive maintenance strategies reduce unplanned downtime, extend machine lifespan, and lower repair costs. By analyzing performance trends, MES ensures maintenance teams receive timely alerts for servicing, improving overall equipment efficiency.
MES focuses on real-time production management, process automation, and shop-floor monitoring, while ERP handles higher-level business operations like finance, procurement, and supply chain management. MES works with ERP to provide manufacturers with complete operational visibility, ensuring factory processes align with business goals.