The Role of MES in the Pharmaceutical Industry
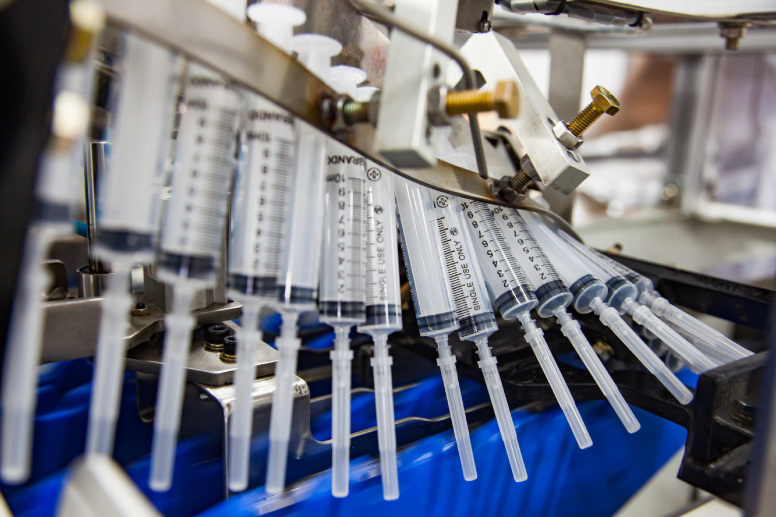
The Role of MES in the Pharmaceutical Industry
"Pharmaceutical MES assists manufacturers in maintaining strict process controls, enforcing regulatory requirements, and ensuring product quality through electronic batch records (EBRs) and automated compliance tracking."
Manufacturing Execution Systems (MES) have become a critical tool for pharmaceutical manufacturers aiming to improve efficiency, maintain regulatory compliance, and ensure product quality.
The pharmaceutical industry operates under strict regulations, requiring manufacturers to implement precise process controls and detailed traceability systems. Traditional manual workflows often introduce errors, inefficiencies, and compliance risks that can lead to costly recalls or production delays. MES addresses these challenges by digitizing and automating core manufacturing processes, creating a data-driven approach that enhances production consistency and visibility.
With the rise of complex drug formulations, personalized medicine, and globalized supply chains, pharmaceutical companies must adopt technologies that provide real-time process monitoring, batch record management, and seamless integration with other enterprise systems. MES streamlines these functions by capturing and analyzing production data, ensuring that each step meets predefined quality standards. Implementing MES allows manufacturers to improve operational efficiency while minimizing risks associated with regulatory audits and product recalls. As the industry continues shifting toward digital transformation, MES is a foundation for scalable, automated, and highly controlled pharmaceutical manufacturing.
What is MES in the Pharmaceutical Industry?
Manufacturing Execution Systems (MES) play a critical role in modern pharmaceutical production by providing real-time monitoring, control, and optimization of manufacturing processes. These software-driven solutions bridge the gap between enterprise resource planning (ERP) systems and plant-floor operations, seamless data flow, and process automation.
Pharmaceutical MES assists manufacturers in maintaining strict process controls, enforcing regulatory requirements, and ensuring product quality through electronic batch records (EBRs) and automated compliance tracking. By integrating MES into pharmaceutical production, companies can improve traceability, reduce errors, and optimize workflows while meeting stringent regulatory standards.
MES solutions also enhance production visibility, allowing manufacturers to track materials, equipment, and personnel activities in real-time. This level of control is essential for maintaining consistency across production batches, minimizing deviations, and streamlining reporting processes to align with Good Manufacturing Practices (GMP).
Importance of MES in Pharma
Pharmaceutical manufacturing requires precise control, strict documentation, and compliance with global regulatory standards. MES supports these requirements by digitizing and automating production processes, reducing manual interventions, and minimizing human error.
Electronic batch records (EBRs) replace paper-based documentation, streamlining record-keeping and audit readiness. With MES, manufacturers can monitor production in real-time, ensuring that all steps meet predefined quality and compliance standards. The system automatically flags deviations, reducing the risk of errors that could lead to costly recalls or regulatory violations.
MES makes Process optimization easier, as the system captures and analyzes production data to identify inefficiencies. This data-driven approach allows manufacturers to adjust workflows, reduce waste, and improve overall equipment effectiveness (OEE). Automated workflows also shorten production cycles, accelerating time-to-market for new pharmaceutical products while maintaining strict quality control.
Benefits of Implementing MES in Pharmaceutical Industries
Pharmaceutical manufacturing requires strict control over production processes to ensure product quality, regulatory compliance, and operational efficiency. Manual documentation and outdated systems introduce risks, including data inconsistencies, human errors, and compliance challenges. MES automates these processes, reducing the likelihood of mistakes and ensuring accurate tracking of materials, equipment, and personnel. By integrating MES into production workflows, pharmaceutical manufacturers gain real-time visibility into operations faster and improve overall efficiency. MES integrates seamlessly with enterprise resource planning (ERP) and laboratory information management systems (LIMS), creating a connected digital ecosystem that enhances manufacturing intelligence.
- Improved Compliance: Automates data collection and ensures accurate documentation to meet regulatory requirements, reducing audit risks and compliance-related delays. Digital batch records replace manual paperwork, ensuring every production step is recorded in real-time and easily accessible for audits. Automated workflows enforce adherence to standard operating procedures (SOPs), minimizing the risk of non-compliance and regulatory scrutiny.
- Enhanced Product Quality: Enforces standardized procedures, reducing human error and ensuring consistent product integrity across all production batches. MES provides built-in quality control mechanisms, automatically flagging deviations from set parameters before defects occur.
- Real-Time Process Monitoring: Provides immediate insights into production performance, allowing operators to detect and address deviations before they impact product quality. MES continuously collects data from sensors, equipment, and production lines, offering a complete view of manufacturing operations. Alerts and notifications highlight temperature fluctuations, machine malfunctions, or unexpected process variations, ensuring quick corrective actions.
- Increased Efficiency: Reduces manual paperwork and streamlines workflows, leading to faster production cycles and optimized resource allocation. MES digitizes production records, reducing administrative burdens and freeing up time for value-added activities. Automated task sequencing ensures that production steps occur in the correct order, minimizing downtime and improving throughput.
- Reduced Waste and Rework: Identifies inefficiencies in production processes, minimizing material losses and improving overall yield rates. MES tracks raw material usage, reducing excess consumption and improving inventory management. Advanced analytics provide insights into recurring defects or inefficiencies, allowing manufacturers to optimize processes and improve overall equipment effectiveness (OEE).
- Seamless System Integration: Connects with enterprise resource planning (ERP) and laboratory information management systems (LIMS) to create a unified digital manufacturing framework. MES synchronizes production data across various departments, ensuring accurate material tracking, batch genealogy, and automated reporting. Integrating existing IT systems allows pharmaceutical manufacturers to streamline operations, reduce redundancy, and improve coordination between quality control, supply chain, and production teams.
Pharmaceutical manufacturers face mounting pressures to produce high-quality products while meeting regulatory requirements and maintaining cost efficiency. MES provides the tools to achieve these goals by offering real-time production insights, automating compliance tracking, and optimizing manufacturing workflows. Integrating MES with existing systems ensures a streamlined, data-driven approach to pharmaceutical production. Companies implementing MES gain an advantage through improved operational transparency, higher product reliability, and reduced risk of compliance-related setbacks. As manufacturing processes become more complex, MES remains a critical solution for improving efficiency, ensuring regulatory adherence, and maintaining high-quality production standards.
Core Components of Pharmaceutical MES
MES provides a structured approach to managing pharmaceutical production, integrating critical functionalities that enhance efficiency, compliance, and traceability. Each component is vital in optimizing operations and ensuring adherence to regulatory standards.
Electronic Batch Records (EBRs)
Electronic batch records replace paper-based documentation, improving accuracy, traceability, and compliance. The system automatically captures and stores production data, ensuring each batch follows predefined protocols. With automated record-keeping, manufacturers eliminate manual data entry errors and reduce the risk of missing critical compliance details. EBRs also simplify audits by providing digital access to historical production data, reducing the time and effort required for regulatory reviews.
Production Scheduling and Workflow Management
Efficient production scheduling ensures that manufacturing resources, including equipment, raw materials, and personnel, are optimized to prevent delays. MES provides intelligent scheduling tools that align production timelines with material availability, reducing downtime and improving workflow efficiency. Automated workflows enforce adherence to standard operating procedures (SOPs), ensuring that each production step is executed according to regulatory requirements. These capabilities help manufacturers maintain a consistent production flow, minimize bottlenecks, and improve on-time delivery rates.
Quality and Compliance Monitoring
Maintaining product quality is essential in pharmaceutical manufacturing. MES integrates quality control functions that continuously monitor process parameters, ensuring that production remains within acceptable tolerances. The system automatically flags deviations, triggers corrective actions, and documents changes in compliance with Good Manufacturing Practices (GMP). By enforcing quality assurance measures throughout production, MES helps manufacturers maintain batch consistency while meeting stringent industry regulations.
Material and Inventory Tracking
MES provides real-time visibility into raw materials, in-process components, and finished goods inventory. This level of tracking prevents material shortages, reduces waste, and ensures accurate stock management. Traceability features allow manufacturers to track the genealogy of each batch, linking raw material usage to final product shipments. This transparency is critical for compliance with traceability requirements, allowing manufacturers to address any issues related to material quality or sourcing quickly.
Equipment and Asset Management
Manufacturing equipment must function efficiently to maintain production schedules and product quality. MES integrates with equipment monitoring systems to track machine performance, schedule preventive maintenance, and reduce unplanned downtime. Predictive maintenance capabilities analyze equipment data to detect early signs of wear, allowing manufacturers to address issues before they cause production disruptions. Effective asset management ensures all equipment operates at peak efficiency, extending machine lifespan and reducing operational costs.
Data Analytics and Reporting
MES collects production data from multiple sources, transforming raw information into actionable insights. The system generates reports on key performance indicators (KPIs), such as yield rates, cycle times, and compliance metrics. Manufacturers use these insights to optimize processes, improve efficiency, and enhance. Advanced analytics capabilities also support continuous improvement initiatives, allowing companies to refine production strategies and maintain operational excellence.
Each MES component contributes to a more efficient, compliant, and data-driven pharmaceutical manufacturing process. By integrating these functionalities, manufacturers can improve process control, enhance product quality, and maintain regulatory compliance while optimizing operations.
Challenges Faced in Implementing MES in the Pharmaceutical Industry
Pharmaceutical manufacturers recognize the benefits of MES, but integrating these systems comes with significant challenges. Technical limitations, regulatory requirements, and workforce adaptation must be addressed to ensure a smooth transition from manual or legacy systems to a digital manufacturing. Careful planning, investment in infrastructure, and proper training are necessary to overcome these obstacles.
- High Initial Costs: MES implementation requires a substantial financial commitment, covering software, hardware, IT infrastructure, and system customization. Many pharmaceutical manufacturers operate on tight budgets, and the cost of upgrading legacy systems can strain financial resources. Small and mid-sized manufacturers may struggle to allocate funds for MES while maintaining existing production lines.
- Complex System Integration: MES must seamlessly connect with enterprise resource planning (ERP), laboratory information management systems (LIMS), and various production control systems. Integrating MES with existing infrastructure presents a challenge, especially when dealing with legacy systems not initially designed for modern digital connectivity. Data silos, interoperability issues, and software incompatibilities often require extensive customization, leading to delays in implementation.
- Regulatory Compliance Adaptation: Pharmaceutical manufacturers must comply with strict regulations such as FDA 21 CFR Part 11, EU Annex 11, and Good Manufacturing Practices (GMP). MES plays a key role in supporting compliance by automating documentation, enforcing batch traceability, and maintaining secure audit trails. However, configuring MES to align with specific regional and international regulatory requirements presents a challenge. Customization may be needed to ensure electronic signatures, automated reporting, and process validation meet legal standards.
- Employee Training and Adoption: Transitioning from manual or paper-based processes to an MES-driven production requires a shift in workforce skills and daily operations. Employees accustomed to traditional manufacturing methods may resist adopting digital workflows, especially if training programs are insufficient or lack hands-on engagement. The complexity of MES interfaces and functionalities can also present a learning curve for operators, technicians, and quality control personnel. Employees may struggle to use MES effectively without proper training, leading to operational inefficiencies and user errors.
- Customization and Scalability Issues: Pharmaceutical manufacturing processes vary significantly based on drug formulations, production volume, and regulatory requirements. A standard MES solution may not fully align with a manufacturer's specific needs, requiring customization to accommodate unique workflows and compliance protocols. Extensive customization can extend implementation timelines and increase costs, making it difficult to realize the benefits of MES in a reasonable timeframe.
- Data Security and Validation Requirements: MES manages highly sensitive production data, including batch records, equipment performance metrics, and compliance documentation. Protecting this data from cyber threats, unauthorized access, and potential corruption is essential for maintaining data integrity and regulatory compliance. MES must include robust encryption, user authentication controls, and secure access protocols to prevent security breaches. System validation is also necessary to confirm that MES meets industry regulations and maintains accurate record-keeping standards. Regular audits, software updates, and IT security measures help safeguard MES against potential vulnerabilities.
Pharmaceutical manufacturers must approach MES implementation with a strategic plan that addresses these challenges. Assessing financial feasibility, aligning MES with existing infrastructure, ensuring regulatory compliance, and providing comprehensive workforce training are essential for a successful deployment. A well-implemented MES improves efficiency and product quality and strengthens compliance and production reliability in the long run.
Successful MES Implementations in Pharma
Pharmaceutical manufacturers implementing MES gain a significant advantage in optimizing operations, ensuring compliance, and improving overall efficiency. MES addresses long-standing challenges such as manual errors, process inefficiencies, and production inconsistencies, allowing companies to achieve greater accuracy and consistency in drug manufacturing. Regulatory agencies impose strict documentation and traceability requirements, and MES plays a crucial role in maintaining accurate records, streamlining compliance audits, and reducing the risk of regulatory penalties.
- Large-Scale Vaccine Production: A global pharmaceutical company implemented MES to manage high-volume vaccine production. The system automated batch records, reduced manual data entry errors, and improved compliance tracking, allowing for faster regulatory approvals. Given the urgency and scale of vaccine distribution, MES played a critical role in ensuring that production met stringent quality standards while expediting batch releases.
- Gene and Cell Therapy Manufacturing: A biotech firm specializing in personalized medicine adopted MES to ensure precise process control. The system real-time monitoring of patient-specific treatments, reducing deviations and enhancing traceability. Unlike traditional pharmaceutical manufacturing, gene and cell therapy processes require extreme precision, as each batch may be tailored to an individual patient.
- Sterile Injectable Production: A manufacturer of sterile injectables integrated MES to improve batch release times. Electronic batch records reduced paperwork processing, cutting the release cycle from several days to a few hours. In sterile manufacturing, contamination risks must be minimized, and MES provides real-time al monitoring and automated reporting to ensure compliance with GMP regulations.
- Multi-Site API Manufacturing: An active pharmaceutical ingredient (API) supplier deployed MES across multiple facilities to standardize production workflows. The system provided centralized data visibility, ensuring uniform compliance with global regulatory standards. API manufacturing involves complex chemical processes that require strict control over raw material quality, reaction conditions, and final product specifications.
- Contract Manufacturing Organization (CMO) Optimization: A contract manufacturer integrated MES to handle multiple client requirements while maintaining strict quality standards. Automated workflows and digital documentation streamlined production across various drug formulations. CMOs must manage production from numerous pharmaceutical clients, each with different regulatory expectations.
- Compliance Enhancement for an Oncology Drug Manufacturer: A pharmaceutical company producing oncology treatments adopted MES to improve adherence to GMP regulations. The system automated deviation tracking, reducing the risk of compliance-related production delays. Oncology drug manufacturing requires stringent controls due to the toxicity and potency of active ingredients.
Successful MES adoption depends on aligning system capabilities with production goals, regulatory requirements, and operational workflows. Pharmaceutical companies integrating MES effectively can streamline manufacturing processes while maintaining complete traceability across production batches. From vaccine production to personalized medicine, MES solutions help companies maintain quality control, standardize processes, and ensure seamless compliance with regulatory standards. As the industry moves toward increased automation and digitalization, MES will continue to play a critical role in shaping the future of pharmaceutical manufacturing.
Future Trends for MES in the Pharmaceutical Industry
Advancements in digital manufacturing continue to shape the future of MES in pharmaceutical production. As regulations tighten and production complexity increases, manufacturers seek solutions that enhance efficiency, improve compliance, and support data-driven. Artificial intelligence (AI) and machine learning (ML) are becoming integral to MES by optimizing predictive maintenance, process monitoring, and quality control. AI-driven analytics provide deeper insights into production trends, helping manufacturers reduce waste and enhance operational efficiency. Cloud-based MES solutions are also gaining adoption, offering scalability and real-time access to production data across multiple facilities.
Pharmaceutical companies are integrating MES with the Industrial Internet of Things (IIoT) to improve real-time equipment monitoring and automation. Smart sensors and connected devices track production parameters with greater precision, reducing manual interventions and enhancing process control. Blockchain technology is also being explored to strengthen data integrity, ensuring tamper-proof batch records and supply chain transparency. Regulatory agencies continue to emphasize data integrity, driving the adoption of electronic batch records and digital signatures within MES. These systems will be crucial in maintaining compliance with Good Automated Manufacturing Practice (GAMP) guidelines, ensuring that all production data is securely stored and easily auditable.
Future MES advancements will focus on increasing automation, integrating emerging technologies, and improving interoperability with other manufacturing systems. These innovations will help pharmaceutical companies enhance product quality, streamline operations, and maintain compliance with regulatory standards.
Pharmaceutical manufacturers must adopt advanced solutions to meet production while maintaining precision and compliance. At 42Q, we deliver smart connected manufacturing with a cloud-based MES platform that enhances visibility, automates workflows, and accelerates production efficiency. Our flexible, scalable solutions give manufacturers real-time insights to optimize processes and meet regulatory requirements. Discover how 42Q can support your digital manufacturing strategy and drive efficiency in pharmaceutical production.
Key Takeaways
- MES enhances compliance and traceability by digitizing batch records, enforcing procedural adherence, and ensuring regulatory audit readiness.
- Real-time process monitoring reduces errors and improves efficiency, allowing manufacturers to detect and correct deviations before they impact product quality.
- MES minimizes waste and optimizes resource utilization by automating workflows, reducing manual interventions, and streamlining production scheduling.
- Integration with existing manufacturing systems seamless data exchange between MES, ERP, LIMS, and quality management systems for improved operational visibility.
- Implementing MES supports scalability and automation, helping pharmaceutical companies adapt to regulatory requirements and increasing production complexity.
FAQs
MES helps pharmaceutical manufacturers maintain regulatory compliance by automating batch record management, enforcing procedural adherence, and generating audit-ready documentation. The system ensures data integrity, reduces human errors, and simplifies compliance with industry regulations such as FDA 21 CFR Part 11 and EU Annex 11.
MES minimizes material waste and rework by providing real-time data on production performance and batch deviations. The system detects inefficiencies, optimizes resource allocation, and prevents overproduction, ensuring that materials are utilized efficiently while maintaining product quality.
MES integrates seamlessly with enterprise resource planning (ERP), laboratory information management systems (LIMS), and quality management systems (QMS). This connectivity allows manufacturers to streamline operations, maintain accurate inventory tracking, and enhance process automation across the entire production cycle.
When implementing MES, pharmaceutical manufacturers must consider system compatibility, regulatory compliance, workforce training, and long-term scalability. Ensuring that MES aligns with existing workflows and production goals is crucial for maximizing its benefits and achieving a smooth transition from manual processes.
MES continuously collects and analyzes production data from equipment, sensors, and batch records for real-time monitoring. Operators receive instant alerts on process deviations, equipment malfunctions, or quality concerns, proactively minimizing production disruptions.