What Are OEE Systems in Manufacturing?
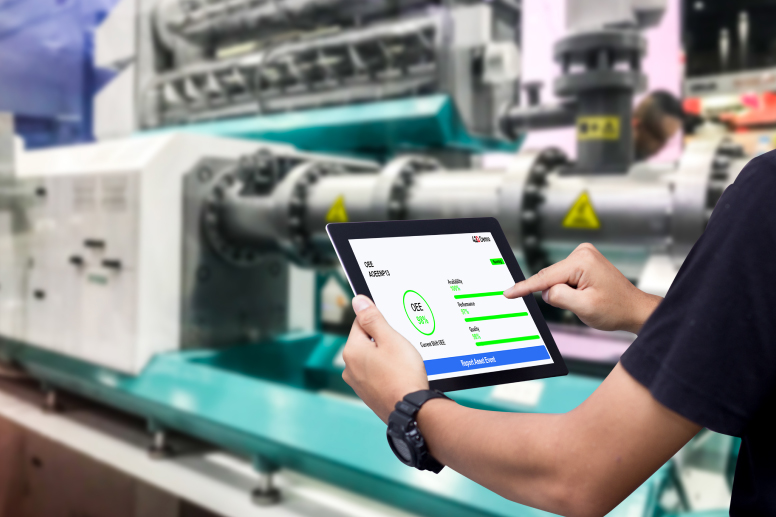
What Are OEE Systems in Manufacturing?
Manufacturers rely on Overall Equipment Effectiveness (OEE) to assess and improve production efficiency.
Measuring availability, performance, and quality helps identify bottlenecks, reduce unplanned downtime, and enhance productivity. Manufacturers struggle to maintain consistent output and operational reliability without accurate OEE tracking.
OEE systems in manufacturing provide actionable insights that allow businesses to improve machine utilization, streamline workflows, and optimize resource allocation. Understanding how to measure and apply OEE metrics reduces waste, improves product quality, and ensures production runs efficiently.
What Does OEE Stand For in Manufacturing?
Overall Equipment Effectiveness (OEE) is a standardized metric that quantifies manufacturing productivity by measuring how efficiently equipment operates. It evaluates three critical factors—availability, performance, and quality—to determine the percentage of planned production time that is genuinely productive. A perfect OEE score of 100% indicates flawless manufacturing: no unplanned downtime, no slow cycles, and zero defects.
Manufacturers rely on OEE to pinpoint inefficiencies, track continuous improvement initiatives, and optimize production output. By providing real-time visibility into equipment effectiveness, OEE systems in manufacturing help identify bottlenecks, reduce waste, and increase throughput. Understanding this metric is essential for improving operational efficiency and maintaining a driving edge in modern production situations.
Importance of OEE Systems in Manufacturing
OEE systems in manufacturing provide a structured approach to identifying and eliminating inefficiencies in production. Every unplanned stoppage, slow cycle, or defective product directly affects output and profitability. Without accurate data on these losses, manufacturers struggle to implement meaningful improvements. OEE systems quantify equipment effectiveness, offering clear insights into performance trends and production constraints.
Operational visibility is essential for improving production efficiency and reducing waste. OEE data helps manufacturers identify recurring downtime causes, assess equipment performance, and implement targeted maintenance strategies. Instead of reacting to breakdowns, businesses can shift to proactive measures that extend machine lifespan, optimize workforce utilization, and maximize throughput.
Key Components of OEE in Manufacturing
OEE systems in manufacturing evaluate equipment efficiency using three fundamental metrics: availability, performance, and quality. Each component identifies specific production losses and provides insight into areas requiring improvement. Understanding these factors helps manufacturers reduce downtime, optimize production speed, and improve product quality.
Availability: Minimizing Downtime and Maximizing Production Time
Availability measures the percentage of planned production time that equipment remains operational. Downtime caused by unplanned maintenance, changeovers, or raw material shortages reduces production efficiency. OEE systems track planned and unplanned stoppages, providing data that helps manufacturers address recurring issues.
Several factors contribute to availability losses, including unexpected equipment failures, lengthy setup times, and delayed material deliveries. Preventive maintenance programs, standardized changeover procedures, and better inventory management reduce disruptions. Increasing machine uptime ensures that production schedules remain consistent, improving manufacturing efficiency.
Performance: Ensuring Optimal Production Speeds
Performance evaluates how efficiently equipment operates compared to its designed capacity. Machines running at slower-than-expected speeds or experiencing frequent micro-stoppages contribute to performance losses. These inefficiencies reduce output without directly halting production, making them difficult to detect without real-time monitoring.
OEE tracking helps manufacturers identify process inefficiencies such as slow cycle times, suboptimal machine settings, and worn-out tooling. Addressing these issues improves production rates while maintaining consistent quality. Proper operator training, proactive machine adjustments, and automated process monitoring support higher performance levels.
Quality: Reducing Defects and Improving Product Consistency
Quality measures the percentage of manufactured products that meet specifications without requiring rework or scrap. Defective products lead to waste, increased costs, and additional labor for corrections. OEE systems track defect rates, providing insights into production inconsistencies and recurring quality issues.
Several factors, including improper machine calibration, inconsistent raw materials, and operator errors, contribute to quality losses. Real-time quality monitoring, automated defect detection, and process standardization help manufacturers maintain high product standards. Identifying and addressing the root causes of defects reduces material waste, improves customer satisfaction, and enhances overall production reliability.
How These Components Work Together
Availability, performance, and quality are connected, with losses in one area often affecting the others. A machine experiencing frequent downtime (availability loss) may also struggle to maintain optimal cycle times (performance loss). Likewise, running equipment at maximum speed without proper quality controls may lead to increased defects (quality loss).
OEE systems in manufacturing provide a structured approach to measuring and improving these key components. Tracking and analyzing OEE data helps manufacturers implement targeted improvements that enhance equipment reliability, increase throughput, and maintain high-quality production standards.
Benefits of Implementing OEE Systems in Manufacturing
OEE systems in manufacturing provide valuable insights that help manufacturers improve efficiency, reduce production losses, and maintain consistent product quality. Measuring availability, performance, and quality allows businesses to identify inefficiencies and take targeted actions that enhance productivity. Tracking OEE metrics provides a structured approach to minimizing downtime, improving machine reliability, and increasing output without requiring additional resources.
- Reduced Downtime and Unplanned Stoppages: Equipment failures and unexpected maintenance issues disrupt production schedules and reduce output. OEE tracking provides real-time data on recurring downtime causes, allowing manufacturers to implement proactive maintenance strategies. Predictive maintenance based on historical trends helps reduce breakdowns, ensuring machines operate reliably and production schedules remain uninterrupted.
- Increased Production Efficiency: Machines that operate below optimal speeds or experience frequent micro-stoppages lead to performance losses. OEE monitoring identifies slow-running equipment, enabling manufacturers to make necessary adjustments. Process optimization, better operator training, and automated tracking tools help improve production rates, ensuring machines perform at their designed capacity.
- Improved Product Quality and Defect Reduction: Defective products lead to material waste, rework, and increased operational costs. OEE systems track defect rates and identify patterns that indicate process inconsistencies or equipment malfunctions. Early detection of quality issues allows manufacturers to implement corrective actions before large-scale defects occur, maintaining high product standards while reducing scrap and rework expenses.
- Lower Operational Costs and Better Resource Utilization: Production inefficiency wastes valuable resources, from raw materials to labor hours. OEE data helps manufacturers optimize resource allocation by ensuring equipment operates efficiently, and workforce utilization remains balanced. Reducing material waste, minimizing energy consumption, and optimizing production workflows contribute to significant cost savings over time.
- Data-Driven Regulating for Continuous Improvement: Accurate and detailed production data allows manufacturers to identify trends and measure the effectiveness of process improvements. OEE reports provide insights into production bottlenecks, enabling businesses to implement data-backed changes that drive continuous operational improvements. Historical data tracking helps assess long-term trends and ensures sustained productivity gains.
- Sustainability and Waste Reduction: Manufacturing operations generate excess waste when inefficient processes or production defects occur. OEE tracking helps minimize unnecessary waste by improving equipment reliability, reducing defective output, and streamlining production workflows. Efficient manufacturing practices contribute to lower energy consumption and a reduced footprint, aligning with sustainability goals while maintaining cost-effective operations.
OEE systems in manufacturing provide structured insights that support efficiency improvements at every production stage. Tracking availability, performance, and quality metrics ensure manufacturers can pinpoint inefficiencies, reduce costs, and maintain a high standard of production output. Implementing OEE-driven improvements leads to measurable gains in productivity, operational stability, and long-term manufacturing success.
Real-World Applications of OEE in Manufacturing
OEE systems in manufacturing are widely used across industries to improve production efficiency, reduce downtime, and maintain high-quality standards. Manufacturers rely on OEE tracking to optimize processes, minimize losses, and ensure consistent output. Each industry applies OEE data to address specific challenges, from reducing machine failures in high-volume production to maintaining strict compliance in regulated sectors.
Automotive Production: Optimizing Assembly Line Efficiency
Automotive manufacturers depend on OEE tracking to maintain continuous production flow in high-speed assembly lines. Unplanned downtime in welding, stamping, and painting stations can cause costly delays and disrupt supply chain coordination. Monitoring availability helps manufacturers detect frequent stoppages, while performance tracking ensures robotic systems and conveyor lines run at optimal speeds. Quality metrics help identify production defects early, preventing faulty components from reaching final assembly. By applying OEE data, automotive manufacturers improve throughput while reducing waste and rework.
Medical Device Manufacturing: Ensuring Compliance and Quality
Medical device manufacturers operate under strict regulatory standards requiring precision, traceability, and consistency. OEE systems help track machine performance in critical operations such as injection molding, sterilization, and assembly. Availability data allows manufacturers to reduce downtime caused by maintenance or validation requirements, while performance monitoring ensures equipment operates within specified tolerances. Quality tracking helps detect defects in sensitive components, minimizing the risk of compliance issues and ensuring that all products meet the required specifications before distribution.
Semiconductor Fabrication: Enhancing Yield and Process Stability
Semiconductor manufacturing relies on OEE tracking to improve yield rates in highly complex and precise fabrication processes. Equipment availability is critical in wafer processing, where unexpected downtime leads to production losses and increased costs. Performance tracking ensures that lithography, etching, and deposition machines operate at optimal cycle times, reducing inefficiencies impacting product quality. Quality monitoring helps manufacturers detect process deviations that could lead to defective chips, allowing for real-time adjustments that protect overall yield.
Aerospace Component Manufacturing: Maintaining Production Reliability
Aerospace manufacturers use OEE systems to monitor production consistency in machining, composite fabrication, and surface finishing processes. Availability tracking helps reduce unplanned downtime in CNC machining and assembly operations, preventing disruptions in supply chain commitments. Performance monitoring ensures that materials such as aluminum and titanium are processed at the correct speeds to avoid defects of stress. Quality tracking supports precision manufacturing requirements, ensuring that critical aerospace components meet industry regulations and safety standards.
Industrial Equipment Manufacturing: Optimizing Multi-Line Production
Manufacturers producing heavy machinery, engines, and industrial components rely on OEE data to improve efficiency across multiple production lines. Availability tracking helps reduce production delays caused by long setup times and changeovers, while performance monitoring ensures machines operate at maximum capacity. Quality data allows manufacturers to detect recurring defects in castings, welded structures, and hydraulic components, leading to fewer warranty claims and improved product reliability.
OEE tracking provides manufacturers data-driven insights that improve efficiency, enhance quality, and support long-term operational stability. Industries implementing structured OEE measurement strategies gain higher production output, reduced waste, and more predictable manufacturing processes.
How to Effectively Measure OEE in Manufacturing
Measuring OEE in manufacturing requires a structured approach that captures accurate availability, performance, and quality data. A well-defined measurement system ensures manufacturers can identify inefficiencies, track production trends, and implement targeted improvements. Accurate OEE tracking provides a clear understanding of equipment effectiveness, helping businesses reduce downtime, improve production speed, and maintain product consistency.
- Define Equipment Availability: Availability measures the actual operating time of equipment compared to the planned production time. Calculating this metric requires subtracting all unplanned downtime, such as machine breakdowns, material shortages, and lengthy changeovers, from the total scheduled time. A lower-than-expected availability score signals recurring stoppages that must be addressed through preventive maintenance, better scheduling, or process adjustments.
- Monitor Performance Efficiency: Performance evaluates how well equipment operates at its designed speed. Machines that run slower than expected, experience frequent micro-stoppages or require frequent operator intervention reduce overall efficiency. Tracking cycle times helps manufacturers pinpoint performance issues caused by incorrect machine settings, worn-out tooling, or inconsistent material feed rates. Addressing these inefficiencies ensures machines produce at optimal speeds without compromising quality.
- Track First-Pass Quality Rates: Quality measures the percentage of products that meet specifications without requiring rework or scrap. To calculate this metric, manufacturers must track defect rates and analyze patterns in production errors. Common causes of quality losses include misaligned machine calibration, raw material inconsistencies, and operator errors. Identifying recurring quality issues requires manufacturers to implement corrective actions such as improved quality control procedures, automated defect detection, and stricter process standards.
- Use Automated Data Collection Systems: Manually tracking OEE metrics increases the risk of data errors and inconsistencies. Automated monitoring solutions, such as machine sensors, manufacturing execution systems (MES), and IoT tracking devices, provide real-time data on equipment performance. These systems capture production information more accurately, allowing manufacturers to respond to inefficiencies immediately rather than relying on retrospective analysis.
- Analyze OEE Trends and Historical Data: Measuring OEE once provides a snapshot of performance, but long-term tracking offers more profound insights into production patterns. Historical OEE data helps manufacturers assess the effectiveness of process improvements, compare performance across different shifts, and identify recurring inefficiencies. Regularly analyzing trends ensures that manufacturing operations continuously improve and that productivity gains are maintained over time.
- Set Benchmarks and Target Goals for Improvement: OEE measurement becomes more effective when manufacturers establish clear benchmarks based on industry standards or internal historical performance. Setting achievable OEE goals allows businesses to track progress and measure the success of process optimizations. Comparing OEE scores across different machines, production lines, or factory locations provides valuable insights into areas that require further refinement.
Implementing a structured OEE measurement process ensures manufacturers collect reliable data, identify inefficiencies, and improve production outcomes. Accurate tracking of availability, performance, and quality metrics supports continuous improvement efforts, helping manufacturers achieve higher efficiency and more consistent operational results.
Manufacturers worldwide are adopting data-driven solutions to improve efficiency, quality, and operational visibility. At 42Q, we combine decades of manufacturing expertise with cutting-edge technology to deliver innovative, connected manufacturing. Our flexible, cloud-native MES platform enhances visibility, streamlines operations, and accelerates digital factory change. Discover how our solutions can empower your factory to achieve its full potential.
Key Takeaways
- To assess manufacturing efficiency, OEE measures three key components—availability, performance, and quality.
- Reducing unplanned downtime through predictive maintenance and optimized changeovers improves equipment availability.
- Optimizing machine performance by addressing micro-stoppages and slow cycle times increases production output.
- Minimizing defects and rework ensures higher product quality while reducing material waste and operational costs.
- Implementing OEE tracking systems gives manufacturers data-driven insights to support continuous process improvements.
FAQs
OEE has been widely used in manufacturing since the 1980s when companies began adopting lean production methodologies. As digital tools and automation improved, OEE became a standard metric for evaluating production efficiency. Today, manufacturers rely on OEE tracking systems to optimize workflows and reduce operational losses.
OEE stands for Overall Equipment Effectiveness and is a key metric to assess manufacturing efficiency. It measures availability, performance, and quality to determine how effectively equipment is utilized. Tracking OEE helps manufacturers identify inefficiencies, reduce downtime, and improve product output.
OEE systems track machine availability and analyze unplanned downtime causes such as equipment failures, long setup times, and material shortages. Manufacturers can reduce stoppages and maintain a stable production flow using predictive maintenance and real-time monitoring. Preventing frequent breakdowns leads to increased uptime and higher productivity.
OEE is a comprehensive metric that combines three key factors—availability, performance, and quality—into a single effectiveness score. Unlike standalone metrics such as machine utilization or defect rate, OEE provides a holistic view of production efficiency. Using OEE alongside other key performance indicators (KPIs) gives manufacturers deeper insights into overall productivity.
Manufacturers can improve OEE scores by addressing availability losses, optimizing machine performance, and reducing quality defects. Strategies such as preventive maintenance, automated process monitoring, and workforce training help enhance efficiency. Using real-time OEE tracking systems allows businesses to make data-driven decisions that lead to continuous improvements.