What is a Computerized Maintenance Management System (CMMS) in MES?
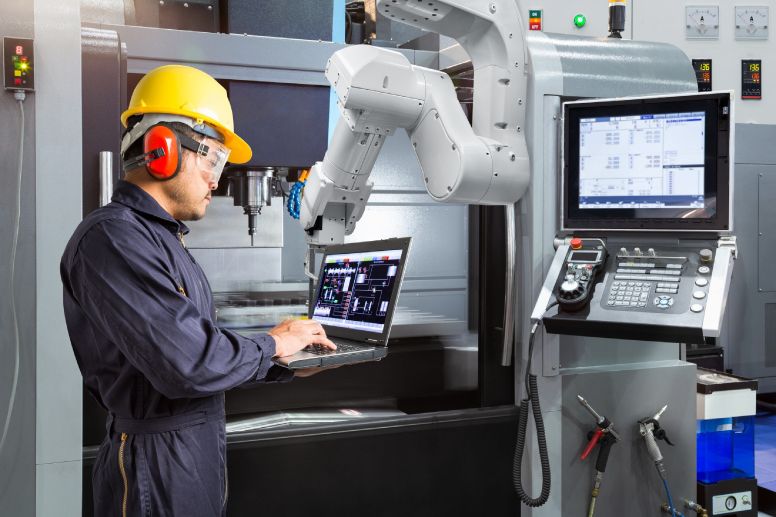
What is a Computerized Maintenance Management System (CMMS) in MES?
Equipment reliability is one of the most important factors in maintaining an efficient manufacturing operation.
A computerized maintenance management system (CMMS) ensures that maintenance activities are planned, tracked, and executed in a way that minimizes disruptions and maximizes uptime. Manufacturing facilities depend on these systems to automate work orders, manage asset lifecycles, and integrate maintenance workflows with production schedules.
The ability to monitor equipment health in real time and schedule proactive maintenance helps manufacturers prevent costly breakdowns and extend machine lifespan. A CMMS in manufacturing reduces maintenance costs, improves compliance, and enhances workforce efficiency. When integrated with a manufacturing execution system (MES), it creates a seamless connection between production and maintenance teams, ensuring that equipment remains operational without impacting output.
Key Features of CMMS Software in MES
A computerized maintenance management system (CMMS) plays a vital role in manufacturing execution systems (MES) by ensuring seamless maintenance operations, reducing equipment failures, and supporting continuous production. The right CMMS software provides essential tools to automate maintenance workflows, track asset performance, and optimize resource management. These features improve plant efficiency, extend machine lifespan, and help manufacturers meet compliance requirements.
- Automated Work Order Management: Generates, assigns, and tracks maintenance tasks, ensuring technicians receive real-time alerts for inspections and repairs. Automated workflows reduce manual scheduling errors, improve technician efficiency, and promptly address high-priority repairs.
- Preventive and Predictive Maintenance: Uses historical performance data, sensor readings, and condition-based monitoring to schedule maintenance activities before failures occur. This proactive approach minimizes costly unplanned downtime and prevents extensive damage to equipment.
- Asset Tracking and Equipment Management: Maintains a centralized database for machinery, tools, and infrastructure, allowing manufacturers to track usage, maintenance history, and depreciation. Keeping accurate records improves asset utilization and helps maintenance teams make informed repair or replacement decisions.
- Spare Parts and Inventory Control: Monitors stock levels, tracks usage patterns, and automates reordering processes to prevent supply shortages. Having the right spare parts available reduces repair wait times, ensuring minimal disruption to production.
- Failure Analysis and Root Cause Reporting: Identifies recurring issues by analyzing failure patterns and maintenance records. Data-driven insights help maintenance teams implement long-term solutions that reduce repeated breakdowns and lower repair costs.
- Compliance and Audit Support: Tracks maintenance records, inspection reports, and calibration logs to meet industry-specific regulatory requirements. Built-in compliance tools streamline audit preparation, ensuring manufacturers have accurate documentation readily available.
- Mobile Access for Maintenance Teams: Provides technicians with mobile-friendly platforms to receive work orders, log maintenance activities, and update asset information in real-time. Mobile CMMS solutions improve response times and reduce communication delays.
- IoT and Sensor-Based Monitoring: Integrates with connected devices and industrial sensors to monitor equipment performance in real-time. Automated alerts notify maintenance teams of irregularities, predictive maintenance that prevents equipment failures.
- Customizable Dashboards and Reporting: Offers data visualization tools that help plant managers analyze key performance indicators (KPIs), track maintenance efficiency, and improve resource allocation. Custom reports provide insights into work order completion rates, asset reliability, and maintenance costs.
- Integration with MES and ERP Systems: Ensures seamless data exchange between maintenance, production, and business operations. Connecting CMMS software with MES and ERP platforms allows manufacturers to synchronize maintenance activities with production schedules, improving overall workflow efficiency.
A CMMS in manufacturing provides essential tools to streamline maintenance operations, prevent equipment failures, and improve cost control. These features help manufacturers optimize asset performance, minimize production disruptions, and maintain compliance with regulatory standards.
The Role of CMMS in Manufacturing
A CMMS in manufacturing serves as the foundation for effective equipment maintenance, helping facilities minimize disruptions and optimize productivity. Production lines rely on machinery operating at peak efficiency, and any unexpected breakdown can result in costly delays. A computerized maintenance management system ensures that all maintenance activities are scheduled, tracked, and executed in a way that maximizes uptime while keeping repair costs under control.
Manufacturers use a CMMS to implement proactive maintenance strategies that reduce the likelihood of unplanned downtime. Equipment sensors and historical performance data allow teams to anticipate failures and take corrective action before they impact production. Maintenance workflows are automated to assign tasks based on priority, resource availability, and machine usage patterns. This level of coordination helps manufacturing plants operate with fewer disruptions and lower operational risks.
Compliance with industry regulations is another critical function of a CMMS in MES. Manufacturing industries such as medical devices, automotive, and aerospace require meticulous tracking of maintenance records, calibration schedules, and component replacements. A CMMS software simplifies compliance efforts by documenting all maintenance activities and ensuring audit trails remain accurate and current.
Benefits of Manufacturing CMMS
A computerized maintenance management system (CMMS) improves manufacturing efficiency by automating maintenance workflows, tracking asset performance, and reducing equipment downtime. In an industry where operational delays lead to significant costs, a well-implemented CMMS in manufacturing ensures that maintenance teams work proactively rather than reacting to unexpected failures. The following benefits help manufacturers reduce expenses, optimize resource allocation, and improve production efficiency.
- Reduced Equipment Downtime: Scheduled maintenance tasks and predictive analytics allow maintenance teams to detect potential failures before they impact production. This proactive approach ensures equipment remains operational, minimizing disruptions to manufacturing schedules and preventing revenue loss.
- Lower Maintenance and Repair Costs: Optimized maintenance schedules prevent excessive wear and tear, reducing the need for costly emergency repairs. A CMMS in MES also helps allocate maintenance resources efficiently, preventing unnecessary labor and equipment expenditures.
- Extended Asset Lifespan: Routine inspections, timely repairs, and condition-based maintenance strategies help extend the life of machinery and production equipment. A maintenance approach reduces premature replacements, protecting capital investments.
- Improved Regulatory Compliance: Manufacturing industries, including medical devices and aerospace, require strict adherence to regulatory maintenance and safety standards. CMMS software automates documentation, ensuring that maintenance records, calibration logs, and audit trails remain accurate and readily accessible.
- Increased Workforce Efficiency: Automated work orders eliminate manual scheduling errors, ensuring technicians receive precise instructions based on equipment priorities. Mobile access to maintenance records allows teams to complete tasks more efficiently and respond to urgent repairs without delays.
- Optimized Spare Parts and Inventory Management: Automated stock level tracking ensures critical spare parts remain available. A manufacturing CMMS prevents overstocking while reducing risks associated with parts shortages, ensuring that repairs are completed on time.
- Better Equipment Performance Monitoring: IoT sensors and MES data provide real-time insights into machine conditions. Maintenance teams can rely on data-driven triggers for servicing, reducing reliance on static maintenance schedules that may not align with equipment needs.
- Enhanced Data Analytics and Reporting: Custom reports and dashboards help manufacturers track maintenance costs, technician productivity, and asset reliability. Data-driven insights support better long-term maintenance planning and strategic rationale.
- More substantial Safety and Risk Management: Regular maintenance inspections reduce the likelihood of equipment malfunctions that could pose safety hazards to employees. A CMMS software ensures that machinery remains in optimal working condition, lowering the risk of workplace incidents.
- Seamless Integration with Production Workflows: A CMMS in MES connects maintenance activities with production schedules, ensuring that planned maintenance does not interfere with critical manufacturing processes. Coordinated workflows improve efficiency without sacrificing output.
A CMMS in manufacturing ensures that production facilities remain efficient, safe, and cost-effective. Manufacturers improve asset reliability by centralizing maintenance operations and automating workflows, reducing unexpected expenses and compliance risks.
Integrating CMMS with MES
A computerized maintenance management system (CMMS) becomes more effective when integrated with a manufacturing execution system (MES). This connection allows manufacturers to align maintenance activities with production schedules, reducing unplanned downtime and improving overall operational efficiency. An integrated system ensures real-time asset performance monitoring, providing maintenance teams with data-driven insights to schedule preventive maintenance without disrupting manufacturing processes.
Seamless integration between CMMS software and an MES improves communication between maintenance and production teams. Equipment health data flows directly into the CMMS, allowing maintenance teams to prioritize repairs based on asset conditions rather than relying solely on time-based schedules. This coordination reduces production stoppages and prevents unnecessary maintenance activities, optimizing machine uptime and resource allocation.
Real-Time Equipment Monitoring
Machine performance data captured by IoT sensors, programmable logic controllers (PLCs), and MES platforms feed directly into the CMMS, allowing maintenance teams to assess asset health in real-time. If a piece of equipment starts showing irregular patterns, automated alerts trigger maintenance requests before failures occur. This prevents unexpected breakdowns while reducing unnecessary preventive maintenance, ensuring resources are used efficiently.
Automated Work Order Scheduling
An integrated system generates work orders based on machine conditions, production requirements, and technician availability. Maintenance tasks are scheduled in coordination with manufacturing workflows, ensuring that planned servicing does not disrupt critical operations. This approach eliminates the inefficiencies of manual scheduling and ensures that equipment receives service at the optimal time.
Enhanced Data Accuracy and Reporting
Manual data entry often leads to inconsistencies and errors that compromise maintenance efficiency. A CMMS in MES eliminates these challenges by automatically recording maintenance logs, repair history, and asset performance data. Accurate reporting gives maintenance managers insights into failure trends, labor efficiency, and cost-saving opportunities, improving long-term maintenance planning.
Optimized Spare Parts and Inventory Control
Connecting CMMS software with an MES directly links maintenance needs and spare parts inventory. Automatic inventory tracking ensures that necessary components are available before a maintenance task begins, reducing delays caused by missing parts. This also prevents overstocking, reducing inventory holding costs while providing critical supplies are always on hand.
Better Compliance and Audit Readiness
Manufacturers in regulated industries must maintain accurate maintenance records for compliance audits. An integrated CMMS in manufacturing streamlines this process by documenting all inspections, repairs, and calibrations in a centralized system. This improves audit readiness and helps manufacturing facilities meet regulatory standards without the burden of manual documentation.
A CMMS integrated with MES provides manufacturers with a connected maintenance strategy that enhances efficiency, reduces downtime, and extends asset lifespan. The ability to track machine health, automate scheduling, and optimize inventory ensures that maintenance operations align with production goals, improving overall plant performance.
Choosing the Right CMMS Software for MES
Selecting a computerized maintenance management system that integrates effectively with an MES requires careful evaluation of key factors that impact operational efficiency, scalability, and cost-effectiveness. Manufacturing operations rely on a CMMS that automates maintenance workflows and aligns with existing production processes.
Compatibility with MES software is essential for seamless data exchange between maintenance and production teams. A system that integrates with IoT devices, machine sensors, and enterprise resource planning (ERP) platforms ensures real-time equipment monitoring and accurate maintenance tracking. Cloud-based deployment options offer flexibility by reducing on-site infrastructure costs while providing secure remote access to maintenance records.
User-friendly interfaces and mobile accessibility improve adoption rates among maintenance teams. A well-designed CMMS allows technicians to access work orders, submit reports, and update asset records from any location. Customization options further enhance usability, allowing manufacturers to tailor features such as automated scheduling, compliance tracking, and spare parts management to fit their specific needs.
Scalability is another important factor when selecting a CMMS in manufacturing. A system that supports multiple facilities, production lines, and asset categories ensures long-term usability as business operations expand. Generating detailed reports and analytics also enhances maintenance planning, helping manufacturers optimize performance and reduce operational risks.
EAM vs CMMS: Key Differences
The main difference between an enterprise asset management (EAM) system and a computerized maintenance management system (CMMS) lies in their scope and functionality. A CMMS focuses on maintenance-related tasks, while an EAM provides a broader approach to asset management, covering the entire lifecycle of equipment from procurement to disposal.
Feature | CMMS | EAM |
Primary Focus | Maintenance scheduling and tracking | Full asset lifecycle management |
Scope | Equipment maintenance and repairs | Procurement, maintenance, and asset utilization |
Integration | Works with MES and maintenance teams | Connects with ERP, MES, and financial systems |
Asset Lifecycle | Limited to the operational phase | Covers acquisition, operation, and decommissioning |
Inventory Management | Tracks spare parts for maintenance | Manages asset-related inventory and procurement |
Compliance Support | Ensures regulatory maintenance tracking | Covers audits, compliance reporting, and documentation |
A CMMS in manufacturing is primarily designed to manage maintenance operations, focusing on scheduling, work orders, and spare parts tracking. It helps manufacturers prevent downtime and maintain regulatory compliance through detailed maintenance logs and automated workflows.
An EAM system takes a more comprehensive approach, tracking assets throughout their lifecycle, from initial acquisition to retirement. This system integrates with financial and procurement modules, making it a better choice for manufacturers that require enterprise-wide asset management.
Future Trends in CMMS for Manufacturing
Advancements in computerized maintenance management system (CMMS) software continue to improve manufacturers' management of maintenance operations, reduce downtime, and optimize asset performance. As manufacturing facilities adopt more innovative technologies, CMMS in MES solutions incorporate automation, real-time analytics, and predictive capabilities to improve efficiency. The following trends are shaping the future of CMMS software in manufacturing.
- AI-Powered Predictive Maintenance: Artificial intelligence (AI) analyzes machine performance data to identify patterns that indicate potential failures. Instead of relying on fixed maintenance schedules, AI-driven insights help maintenance teams anticipate issues before they lead to breakdowns, improving equipment reliability and reducing repair costs.
- IoT-Connected Maintenance Systems: Industrial IoT (IIoT) devices collect real-time sensor data from machines, continuously monitoring temperature, vibration, and energy consumption. A CMMS in manufacturing processes this data and generates automated alerts when equipment conditions deviate from normal operating ranges, allowing maintenance teams to act before failures occur.
- Cloud-Based CMMS Deployment: Cloud-based CMMS software allows manufacturers to manage maintenance operations without requiring extensive on-site infrastructure. Cloud solutions offer better accessibility for maintenance teams, secure data storage, automatic updates, and the ability to scale across multiple facilities without expensive hardware investments.
- Augmented Reality (AR) for Maintenance Support: AR technology assists technicians by overlaying real-time visual instructions onto equipment during inspections and repairs. This helps reduce downtime, minimize human errors, and improve training for new maintenance personnel, ensuring tasks are performed correctly without delays.
- Mobile CMMS Applications for On-the-Go Maintenance: Maintenance teams benefit from mobile-friendly CMMS software that provides instant access to work orders, asset records, and real-time machine data. Mobile solutions improve response times by allowing technicians to diagnose and resolve issues without being tied to a desktop interface.
- Automated Workflows and AI Chatbots: AI-powered virtual assistants help maintenance teams schedule and manage tasks by automating routine processes such as work order creation and equipment status updates. These tools reduce administrative burdens, allowing technicians to focus on critical maintenance tasks instead of manual data entry.
- Integration with ERP, MES, and Supply Chain Systems: Future CMMS solutions are improving integration with manufacturing execution systems (MES), enterprise resource planning (ERP), and supply chain platforms. This parallel approach ensures maintenance planning aligns with production goals, inventory management, and procurement schedules, reducing downtime caused by equipment failures or spare part shortages.
- Sustainability-Focused Maintenance Strategies: Manufacturers prioritize energy-efficient and sustainable maintenance practices to reduce waste and lower operational costs. A CMMS and a capable MES can support these initiatives by tracking energy usage, optimizing maintenance schedules, and ensuring compliance with fit regulations.
- Automated Compliance and Safety Audits: Compliance tracking tools within CMMS software simplify audits by maintaining digital records of inspections, certifications, and regulatory maintenance requirements. Automation reduces non-compliance risk while ensuring that all equipment remains appropriately working.
Advancements in CMMS technology are reshaping maintenance strategies by improving efficiency, increasing automation, and reducing costs. Combining AI, IoT, and real-time data analytics ensures manufacturers can optimize maintenance operations while keeping production lines running smoothly.
Manufacturers worldwide are adopting digital solutions to improve efficiency, precision, and scalability. At 42Q, we combine decades of manufacturing expertise with cutting-edge technology to deliver smart connected manufacturing. Our flexible, cloud-native MES platform enhances visibility, streamlines operations, and accelerates digital transformation. Discover how our solutions can empower your factory to achieve its full potential.
Key Takeaways
- A computerized maintenance management system (CMMS) automates maintenance tracking, work order scheduling, and asset management, reducing downtime in manufacturing.
- Integrating CMMS software with an MES ensures seamless coordination between maintenance and production, improving efficiency and reducing operational risks.
- Predictive maintenance powered by IoT and AI helps manufacturers schedule repairs based on real-time equipment data, preventing costly failures.
- Compliance tracking within a CMMS in manufacturing simplifies audits by maintaining digital records of maintenance activities, inspections, and regulatory requirements.
- Cloud-based CMMS solutions provide manufacturers with remote access, automated updates, and scalable deployment, making maintenance operations more efficient and cost-effective.
FAQs
A computerized maintenance management system (CMMS) is a software tool that automates maintenance tracking, schedules repairs, and manages asset lifecycles. It helps manufacturers reduce downtime, improve efficiency, and optimize maintenance resources.
A CMMS in MES connects maintenance activities with production schedules, ensuring real-time equipment monitoring and automated work order management. This integration helps maintenance teams prevent disruptions while optimizing machine uptime.
Industries such as automotive, aerospace, medical devices, and consumer electronics rely on CMMS software to maintain regulatory compliance, improve asset reliability, and reduce maintenance costs. Any industry that depends on continuous production benefits from a CMMS.
Predictive maintenance in a CMMS in manufacturing uses IoT sensors and historical performance data to identify early signs of wear or failure. Maintenance tasks are scheduled based on actual asset conditions, reducing unnecessary servicing and preventing unexpected breakdowns.
A manufacturing CMMS lowers maintenance costs by preventing equipment failures, reducing emergency repairs, and optimizing spare parts inventory. Automated maintenance scheduling ensures resources are used efficiently, helping manufacturers control expenses while improving productivity.