Case Study
Weir Increased Throughput
& Reduced WIP
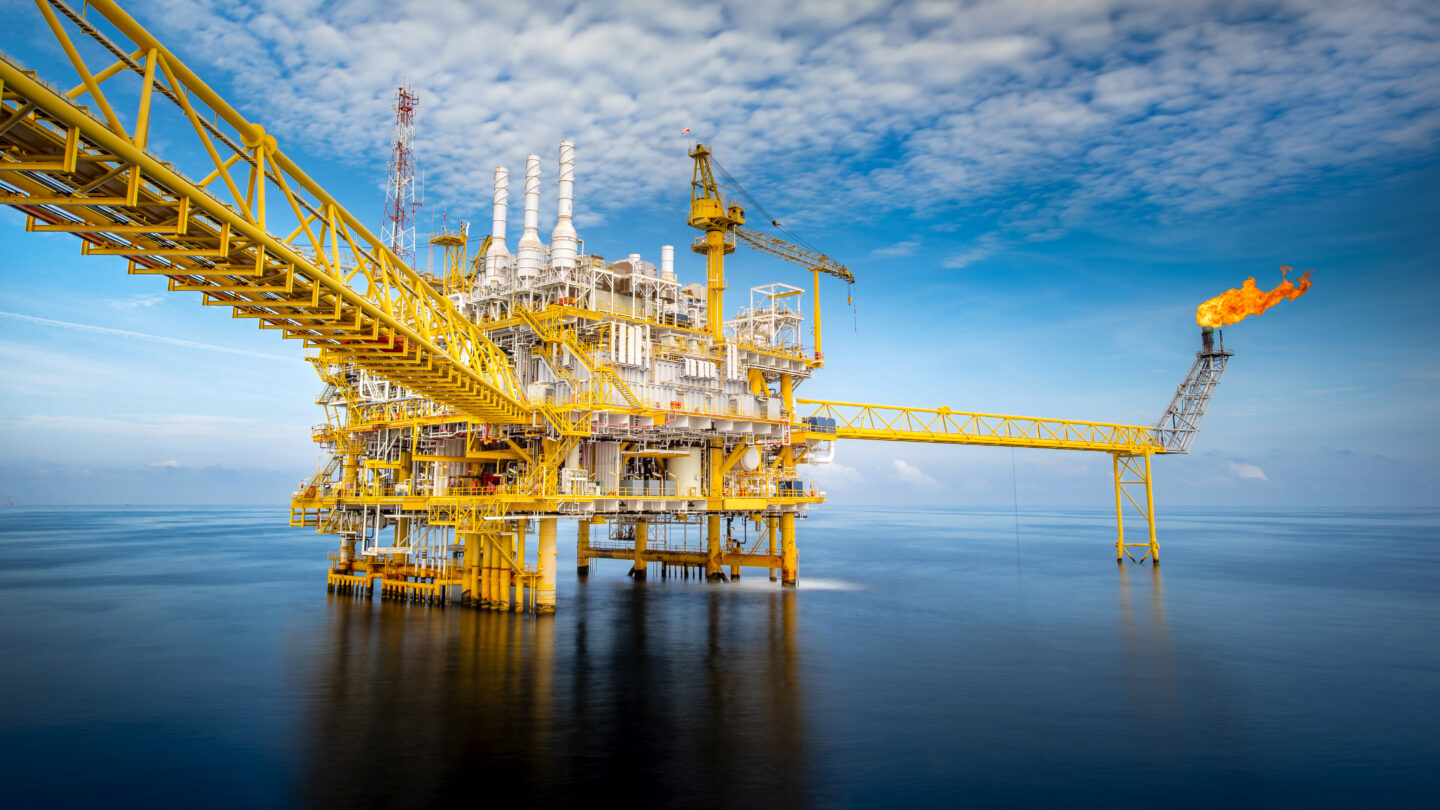
The Challenge
Weir Minerals European Manufacturing Headquarters is located in Todmorden, U.K.. The facility specializes in the manufacturing and assembly of specialist and high duty pumping systems. The product portfolio ranges in weight from around 3kg up to 19,000kg and when fully assembled can be in excess of 45,000kg. These products are made in a range of proprietary controlled alloys and service a global market.
Weir needed to significantly improve manufacturing performance, and increase asset utilization. Their vision was to align value streams to enable a lean manufacturing philosophy. To do this they needed real-time data availability to enable critical decision making. They decided to digitally transform the management of their manufacturing operations from a mix of manual and paper-based processes as well as outdated systems to a cloud-based MES solution that could support the company’s Industry 4.0 strategy.
Different manufacturing operations: foundry, machine shop, laser cladding, assembly and a digital additive manufacturing center, needed the same MES solution to provide real-time data visibility, process and quality control. They also needed seamless integration with the ERP system and manufacturing equipment.
Why 42Q
Weir was looking for a partner that could not only solve their existing manufacturing problems but also support their global deployment strategy. After an extensive vendor selection process, 42Q was chosen as the new MES for Weir’s facility in Salt Lake City, U.S.A.. Implementation of 42Q’s Digital Factory Xcelerator at the facility enabled significant operational improvement including lead-time reductions of 30% for some products. As a result of the positive impact of 42Q on Weir’s manufacturing operation in Salt Lake City, the company decided to roll it out across all plants worldwide.
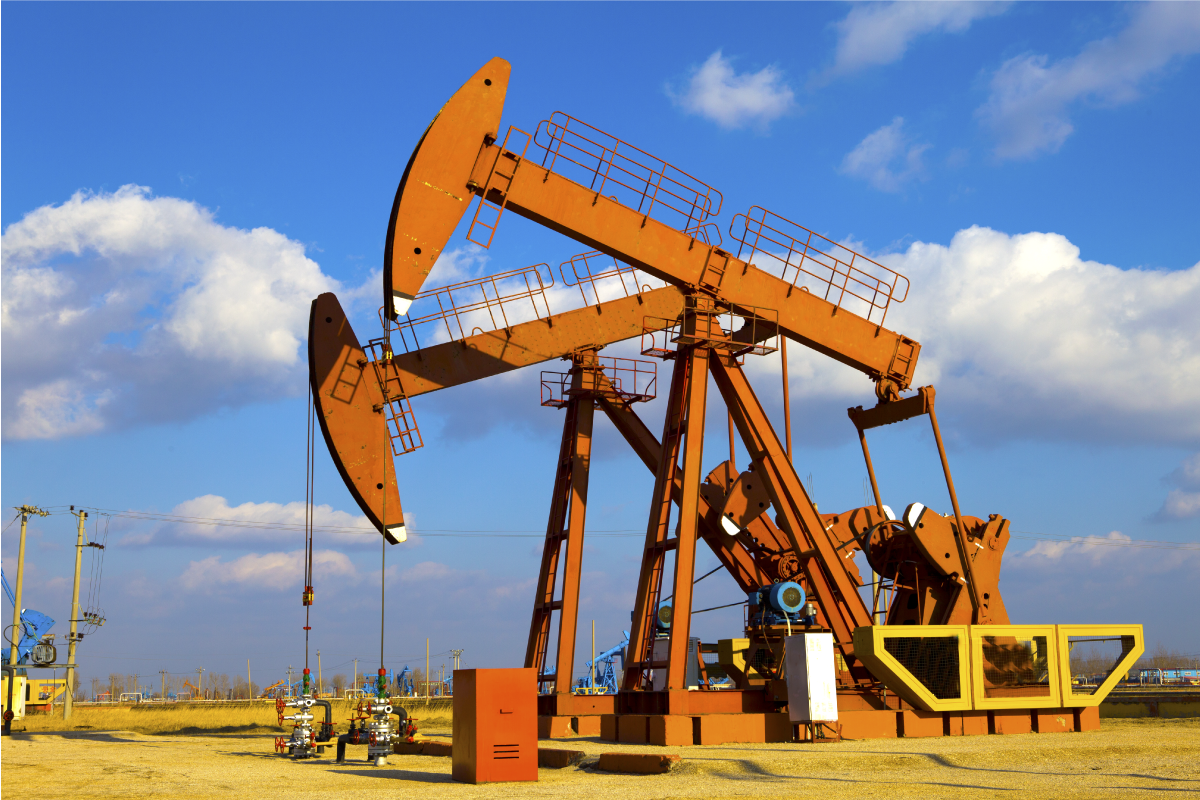
The Results:
- Increased foundry throughput by 53%
- Reduced WIP inventory by 37%
- Improved first pass yield from 90% to 99.1%